You have reached your limit of 3 free stories. A story preview is shown instead.
To view more stories
(If your subscription is current,
click here to Login or Register.)
Bale Cushion Saves Tub Grinder
Last year, when Phil Schalin dropped the first of his 3,000-lb. silage bales into his hay shredder, he knew the unit wouldn't last long if he couldn't find a way to cushion the drop.
"Dropping something that heavy from above the 5-ft. tub, easily has the potential to break the tub away from the table and weaken
..........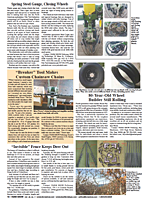
You must sign in, subscribe or renew to see the page.
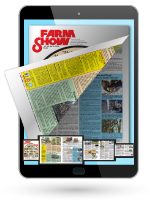
You must sign in, subscribe or renew to see the flip-book
Bale Cushion Saves Tub Grinder LIVESTOCK Feeding Equipment 29-2-33 Last year, when Phil Schalin dropped the first of his 3,000-lb. silage bales into his hay shredder, he knew the unit wouldn't last long if he couldn't find a way to cushion the drop.
"Dropping something that heavy from above the 5-ft. tub, easily has the potential to break the tub away from the table and weaken the frame," Schalin explains. "I decided right away to design and build a bale cushion, and it has worked great."
The frame of the bale cushion sits on the outside front of the Haybuster's frame. Angle braces run up the front wall of the tub, then extend at a right angle across the top for about 10 in., where there's a hinge connecting to the cushion's 3 1/2-ft. arm, which hangs down (when retracted) inside the tub. The arm is only about 3 in. inside the bale chamber itself, so there's still plenty of room for the bale to turn. The hydraulic cylinder that controls the arm, passes through a hole that Schalin cut through the mesh in the front wall of the shredder.
When Schalin lifts the cushion arm up in preparation for receiving a bale, it extends toward the back at a 90? angle.
"As you lift the bale up with the shredder fork, it slides forward until it contacts the hydraulic bale cushion arm, which breaks the fall. Then, you let it down by retracting the cushion arm," Schalin says.
The force of the bale is transferred from the arm to the cylinder, to the cushion arm's frame.
"We only had two hydraulic controls on the tractor, so I had to put in a splitter valve. I used the one I had sitting on the shelf from a Schulte Rock Picker," he says. "Because of the way it was designed on the rock picker, it's controlled by ropes, so I just transferred the idea to the shredder. You pull one rope and it activates the arm of the cushion; the other rope controls the shredder's floor chains, which rotate the bale."
Schalin used 4-in. square tubing for the cushion's framework, and 2 3/8 tubing for the arm itself. The device incorporates a 3 1/2 by 20-in. cylinder off Schalin's cultivator.
The project's design and construction took him 2 to 3 days.
"To buy new materials, you'd probably be looking at $1,500 to $2,000 to build it," he says, "but I didn't spend much because I used scrap that I already had."
Contact: FARM SHOW Followup, Phil Schalin, Box 13, Hylo, Alta., Canada T0A 1Z0 (ph 780 623-7255).
To read the rest of this story, download this issue below or click
here to register with your account number.