You have reached your limit of 3 free stories. A story preview is shown instead.
To view more stories
(If your subscription is current,
click here to Login or Register.)
Brake-Drum Forge
If you need a small forge for a little bit of blacksmith work, you can make one quick from an old pickup brake drum.
"Most people already have all the bits and pieces they'd need to make a good small forge," says Jock Dempsey, blacksmith, consultant, guru and operator of anvilfire.com, a web-based blacksmith inf
..........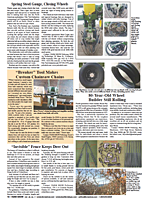
You must sign in, subscribe or renew to see the page.
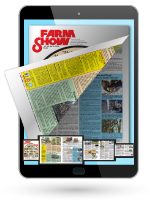
You must sign in, subscribe or renew to see the flip-book
Brake-Drum Forge FARM SHOP Miscellaneous 29-2-39 If you need a small forge for a little bit of blacksmith work, you can make one quick from an old pickup brake drum.
"Most people already have all the bits and pieces they'd need to make a good small forge," says Jock Dempsey, blacksmith, consultant, guru and operator of anvilfire.com, a web-based blacksmith information service. He says the basic requirement is that the material you use be able to withstand the heat of the forge. The high quality cast iron used to make brake drums is more than adequate.
Once you have the drum on a stand, you need a way to blow air through your fire to create the high temperatures needed to soften and work steel.
"There are millions of variations for making a basic forge," Dempsey continues. "They all work, as long as you can get air to the fire."
He suggests cutting a 1 1/2 to 2 1/2 in. hole in the forge as an air inlet. Automotive exhaust pipe can be used to make a manifold to carry air to the fire from your blower. "You'll need an air source that can supply a minimum of 150 cu. ft per minute for a small forge," he adds.
You can use an electric hair dryer for an air source, as long as you plumb it in properly, which includes making your air duct long enough that heat from the forge doesn't melt the plastic case of the dryer.
You can also use a small squirrel-cage fan or an air pressure line from your shop.
Another way to make a small forge is to use two disc blades.
"You use one blade for the base, weld on a length of pipe the right height for your forge, and weld the second blade on to hold your fire," Dempsey says.
Contact: FARM SHOW Followup, Jock Dempsey, Dempsey's Forge, 1684 Mitchell Mill Rd, Gladys, VA 24554-2938 (ph 434 283-5671; email: guru@anvilfire.com; website: www.anvilfire.com).
To read the rest of this story, download this issue below or click
here to register with your account number.