How To Calibrate A Torque Wrench
Using a torque wrench to get just the right pressure on a bolt head is great if your torque wrench is calibrated correctly. What if it's not? Joseph Cannon found that three out of five of his torque wrenches were 5 to 15 lbs. off. A friend's new Craftsman clicker wrench was 20 lbs. off. When exchanged for a new wrench, they found it was off by 10 lbs. So the torque wrench tester Cannon had just built more than paid for itself.
"I made it from several pieces of scrap and an old slave cylinder," explains Cannon. "I needed a bolt that the wrench could exert pressure on and a link that would exert a force on the piston and fluid in the slave cylinder. I also needed a pressure gauge to interact with the fluid in the cylinder."
An engineer by training and by trade, Cannon understood the math behind his deviceàTorque = Force X Distance. To turn a psi pressure gauge into a torque gauge, he needed to determine how much force would be applied over the length of the link he had chosen to achieve 60 lbs. of torque. Once he had that, he could revise the dial on a pressure gauge to correlate to torque instead of psi.
He used a hex bolt inserted through a square tube and linked to the slave cylinder by a piece of scrap metal. A shear pin connected the link to the bolt. The slave cylinder was secured in place and mounted to the steel tube with a second piece of scrap.
When the hex bolt is turned, it exerts pressure on the slave cylinder. To calculate the pressure-torque equivalent, he needed to first know the length of the link.
With his device, the length of the link is 0.3 ft. When placed in his equation of Torque = Force X Distance, with the torque being 60 ft. lbs, and distance being 0.3 ft., the only unknown was force. By dividing both sides by 0.3, force was shown to be 200 lbs.
He also needed the area of the cylinder. To determine that, he multiplied 3.14 times the radius of the cylinder (0.4 in.) and squared it. This gave him an area of 0.502 sq. in.
Once he had this information he could divide the force (200 lbs.) required for 60 ft. lbs. of torque by the area of the piston (0.502 in.) it was exerted against to get the pounds psi. In this case it was 298 psi.
It became a simple matter to install a 300 psi pressure gauge and put a home made face on it replacing the 300 psi mark with a 60 ft. lbs. mark and dividing the remainder of the dial accordingly.
"The important thing to remember is to use the same units of measurement throughout. If you start with feet, stay with feet. If you start with pounds, stay with pounds," says Cannon. "If you know the area of the cylinder you are using and the length of the link, you can figure out everything else."
Contact: FARM SHOW Followup, Joseph Cannon, Fairfax, Va. (Please contact via email address only: jpc8904@yahoo.com).
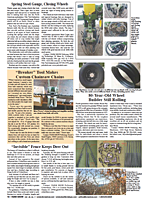
Click here to download page story appeared in.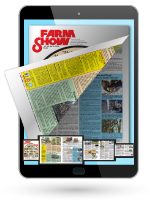
Click here to read entire issue
How To Calibrate A Torque Wrench FARM SHOP Handy Hints 29-3-38 Using a torque wrench to get just the right pressure on a bolt head is great if your torque wrench is calibrated correctly. What if it's not? Joseph Cannon found that three out of five of his torque wrenches were 5 to 15 lbs. off. A friend's new Craftsman clicker wrench was 20 lbs. off. When exchanged for a new wrench, they found it was off by 10 lbs. So the torque wrench tester Cannon had just built more than paid for itself.
"I made it from several pieces of scrap and an old slave cylinder," explains Cannon. "I needed a bolt that the wrench could exert pressure on and a link that would exert a force on the piston and fluid in the slave cylinder. I also needed a pressure gauge to interact with the fluid in the cylinder."
An engineer by training and by trade, Cannon understood the math behind his deviceàTorque = Force X Distance. To turn a psi pressure gauge into a torque gauge, he needed to determine how much force would be applied over the length of the link he had chosen to achieve 60 lbs. of torque. Once he had that, he could revise the dial on a pressure gauge to correlate to torque instead of psi.
He used a hex bolt inserted through a square tube and linked to the slave cylinder by a piece of scrap metal. A shear pin connected the link to the bolt. The slave cylinder was secured in place and mounted to the steel tube with a second piece of scrap.
When the hex bolt is turned, it exerts pressure on the slave cylinder. To calculate the pressure-torque equivalent, he needed to first know the length of the link.
With his device, the length of the link is 0.3 ft. When placed in his equation of Torque = Force X Distance, with the torque being 60 ft. lbs, and distance being 0.3 ft., the only unknown was force. By dividing both sides by 0.3, force was shown to be 200 lbs.
He also needed the area of the cylinder. To determine that, he multiplied 3.14 times the radius of the cylinder (0.4 in.) and squared it. This gave him an area of 0.502 sq. in.
Once he had this information he could divide the force (200 lbs.) required for 60 ft. lbs. of torque by the area of the piston (0.502 in.) it was exerted against to get the pounds psi. In this case it was 298 psi.
It became a simple matter to install a 300 psi pressure gauge and put a home made face on it replacing the 300 psi mark with a 60 ft. lbs. mark and dividing the remainder of the dial accordingly.
"The important thing to remember is to use the same units of measurement throughout. If you start with feet, stay with feet. If you start with pounds, stay with pounds," says Cannon. "If you know the area of the cylinder you are using and the length of the link, you can figure out everything else."
Contact: FARM SHOW Followup, Joseph Cannon, Fairfax, Va. (Please contact via email address only: jpc8904@yahoo.com).
To read the rest of this story, download this issue below or click
here to register with your account number.