You have reached your limit of 3 free stories. A story preview is shown instead.
To view more stories
(If your subscription is current,
click here to Login or Register.)
Rope Maker With A Mission
Skip Wise has a passion for making ropes and he wants to expose as many young people as possible to the craft. Best of all, the rope-making demonstrations he puts on are paying his way around the country.
"Shows bring me in to do demonstrations and I make and sell ropes to cover my expenses," explains Wise. "At
..........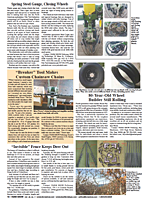
You must sign in, subscribe or renew to see the page.
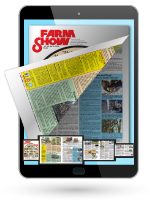
You must sign in, subscribe or renew to see the flip-book
Rope Maker With A Mission AG WORLD 29-4-24 Skip Wise has a passion for making ropes and he wants to expose as many young people as possible to the craft. Best of all, the rope-making demonstrations he puts on are paying his way around the country.
"Shows bring me in to do demonstrations and I make and sell ropes to cover my expenses," explains Wise. "At larger shows, someone may pay my expenses and I will give the ropes away."
Wise first saw a rope making demonstration 15 years ago in Texas and got hooked on the craft. Since then, he has made literally thousands of ropes. Most of the ropes he makes are 15-ft. toy lassos made from 12 strands of poly hay bale twine. As he finishes them, he burns off the ends and then ties a hondo at one end.
"It takes about 5 to 7 minutes to make one," says Wise. "In two days at the Cowboy Hall of Fame, with two machines running, I give away 800 to 900 ropes."
The longest rope he ever made was 175 feet and the thickest had three sets of 16 strands each. In rope making language, strands are called yarn, and as the rope twists together, it is called laying the rope. Through his work, Wise hopes to maintain awareness of how ropes are made as well as the language of the craft.
He has bought several rope-making machines from Fred Mueller, Sheridan, Wyo. Mueller holds the patent on the Rope Master (featured in FARM SHOW Vol. 22, No. 6).
Key to rope making is keeping the right tension on the rope and keeping the fibers turning at the same speed as they twist together. Normally it requires three people to make rope. One turns the crank on a machine that has three hooks. The three turn independently of each other to place a twist on the strands hooked to each. At the other end of the three strands is a second helper. His job is to make sure the hook attached to the strands swivels properly. He also maintains approximately 20 lbs. of pressure on the strands. Humidity and temperature can affect the amount of tension required.
In between is a third worker with a triangular shaped guide. A circle in each corner of the guide keeps the three twisting strands apart until they have twisted sufficiently to begin "laying by." It is gradually moved toward the twisting hooks as the rope forms behind it.
With the addition of a sliding swivel hook, Wise has reduced the rope making team to two. The device consists of a foldable sawhorse, which he has reinforced with a cross piece on each side. A 5 1/2-ft. 2 by 6 attaches to the sawhorse, wide side up. The swivel hook is attached to the back end of a 15-in. long box made from 1/2-in. plywood. The inside dimensions of the box are 6 by 6 in., while two sides are 8 in. wide. When placed on the 2 by 6, this allows them to guide the box. As the rope forms, it draws the box down the length of the 2 by 6. The friction of the wood against wood and weights hung on the box provide the required 20 lbs. of tension.
"The length of the 2 by 6 is important as material loses 10 to 30 percent of its length as it twists together, depending on the material used," explains Wise.
While the length of the 2 by 6 is sufficient for the 15-ft. ropes he normally makes, it might not work for longer ropes.
Wise has also experimented with a variety of swivels for the rope forming end. His favorite is fashioned from the front axle of a Schwinn racing bike.
Contact: FARM SHOW Followup, Skip Wise, RR2, Box 63, Elmore City, Okla. 73433 (ph 580 788-2734).
To read the rest of this story, download this issue below or click
here to register with your account number.