2005 - Volume #29, Issue #5, Page #35
[ Sample Stories From This Issue | List of All Stories In This Issue | Print this story
| Read this issue]
On-Farm Firewood Processor
![]() |
![]() |
![]() |
![]() |
![]() |
![]() |
"It's safe and simple enough for my teenage daughter to operate," Bubnick says. "It'll handle a log that's up to 18-in. in dia. and 60-ft. long. I actually engineered it to handle trees up to 80-ft. long, but I have yet to see any that long in this area."
He made the unique wood processing machine using common, off-the-shelf parts wherever possible, and mounted the unit on a 930 Case tractor.
"Some machine work was necessary, but almost all of it was built in my small farm shop with basic tools," Bubnick explains. "I also work fulltime as a millwright and I used to farm, so machinery is pretty much my life."
He says he designed and built the processor to handle crooked tree trunks that aren't suitable for his home-built sawmill, but he's starting to use the rig to get into the firewood production business.
"The trees are cut, limbed and skidded to the processor. I run these through the processor and they come out as finished, cut-to-length, and split firewood," Bubnick says. "The only hands-on part is putting tongs onto the logs to lift them, and also pulling levers on the machine. Aside from cleaning out screenings and sawdust, the rest is done mechanically."
The unit is almost maintenance-free, he says, and does not require the aid of a loader tractor.
"I use it day after day and do little more than check the oil," says Bubnick.
To process a log, the tongs are attached to the butt of the tree and a winch is used to drag it up over the hydraulic-driven feed rollers.
The feed roll frame tilts back, causing the entire log to lift in the air and onto the machine. Then it's fed into the buzz saw blade opening until it hits the stop, which can be adjusted to cut in lengths from 24 to 12 in.
The feed rollers have aggressive carbide-tipped teeth, which prevent the log from turning while the 48-in. hydraulically-driven circular blade is lowered to make the cut.
The logs are then pushed into the splitter chamber where a hydraulic splitter is manually-activated, pushing the wood through a 10-way closed grate with up to 50 tons of force.
Once the log reaches a maximum 6-in. diameter, another lever manually stops the splitter in the closed position, blocking the chamber opening. This causes the wood to now bypass the splitter. After it passes through or over the grate, it passes over a 2-stage clean-out grate to rid it of small pieces of bark and other trash before it's pushed onto the 30-ft. elevator, which takes the wood up into a truck, trailer or pile.
The tractor hydraulics run everything except the splitter and blade, which have a shared 35-gal. pressure-compensated piston pump driven off the pto. An oil-bath chain drive boosts the pto up to 2,000 rpm's.
This pump automatically de-strokes, should something jam or stall, and this makes for a very smooth operation with little heat build-up.
The blade drive uses two 16-gal. piston motors, running at about 2,000 rpms, which drive the blade through an oil bath chain drive at 800 rpms.
"I have a 5-gauge set tooth, 44-in. blade on the machine now, which looks like it will last through about 75 cords of gritty logs between sharpenings," says Bubnick, who plans to eventually replace the blade with an IKS/Simmonds Kodiak 2-gauge inserted carbide tooth blade.
"The splitter has what I call mechanical automation. You pull a lever which locks, and the 7-in. dia. splitter cylinder extends until it strokes to the preset limit (and then stops if the bypass lever is pulled). It then automatically cycles back to return with no hands on," he says. "There is an emergency stop that halts the cycle at any point and causes the cylinder to retract and wait."
The splitter cylinder itself has a 4-in. dia. piston controlled by “load sensing” valves
that cycles it out fast in a single acting mode, with the force of a 4-in. dia. cylinder, and
then automatically shifts to the power of the 7-in. dia. cylinder bore, as needed. A 3 1/2-
in. cylinder is used for the return stroke to keep it all cycling fast.
Other valves ensure that both sides of the 7-in. cylinder get filled when retracting.
“One problem I encountered was the weight overhanging the rear of the tractor.
Although I engineered the framework to handle it, I miscalculated the balancing of the
tractor, which needed approximately 2,750 lbs. of front weight to correct,” Bubnick admits.
The output of this system varies with the size and age of the logs. For example, 2 or 3-
year-old logs go through at a faster rate.
“I am doing 3 cords per hour of trembling aspen - green 12-in. by 40-ft. logs - at a leisurely but steady pace. Dry burr oak goes through slightly slower. If the splitter was in
bypass mode, and had someone working the tongs, I would think production might as
much as double in a perfect run,” he says.
Contact: FARM SHOW Followup, Perry Bubnick, Box 455, Esterhazy, Sask., Canada
S0A 0X0 (ph 306 745-2429; perrys_email@myway.com).
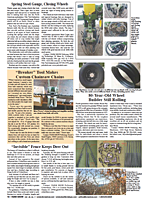
Click here to download page story appeared in.
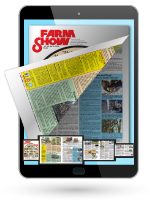
Click here to read entire issue
To read the rest of this story, download this issue below or click here to register with your account number.