You have reached your limit of 3 free stories. A story preview is shown instead.
To view more stories
(If your subscription is current,
click here to Login or Register.)
"Tempest" Turns Waste Streams Into Profit
Run hog manure through a Tempest Air Drying System, and you get compost-type fertilizer ready to bag. Run dried distillers grain with solubles through the same machine, and you'll get a golden puffed grain product that rivals soy meal.
In the case of hog manure, all pathogens are killed, the water is pulled off,
..........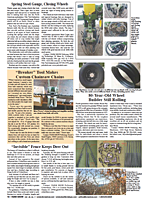
You must sign in, subscribe or renew to see the page.
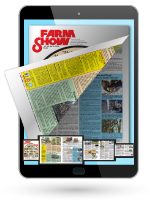
You must sign in, subscribe or renew to see the flip-book
"Tempest" Turns Waste Streams Into Profit FERTILIZER APPLICATION Fertilizer Application (58f) 29-6-10 Run hog manure through a Tempest Air Drying System, and you get compost-type fertilizer ready to bag. Run dried distillers grain with solubles through the same machine, and you'll get a golden puffed grain product that rivals soy meal.
In the case of hog manure, all pathogens are killed, the water is pulled off, 95 to 96 percent of the nutrients are captured and the odor is gone. With the processed distillers grain, there is a shelf life in the 4 to 7-week range and a protein level of 34 to 38 percent.
The same magic seems to hold true for waste from water treatment plants, papermaking, wine making and nearly any other high moisture material that the manufacturer, Global Resource Recovery Organization (GRRO), has tried.
"We can take about any waste stream and dry it down," says Loran Balvanz, president, GRRO.
The hog manure test system has been operating on a conventional hog farm for more than a year and a half. Now a new 2,400-head unit is being built specifically to work with the new technology. GRRO has also processed grape residue for cattle feed, sludge cake (sewage) for fuel and even dairy bedding sand.
"We can take sand used for bedding in dairies, heat it to kill the pathogens, remove the water, vibrate out the waste and give back the sand," he says. "This technology creates a whole new road map when it comes to recycling. Why haul water if you can remove it."
GRRO's technology utilizes airflow to shear cell walls, which aids in releasing water. The airflow, akin to a controlled tornado, also removes the moisture to the desired level, as low as 15 percent.
The modular systems range in size from 5 to 10 wet tons per hour processing and can be designed to fit any size operation. An entire mobile system can fit on an 8 1/2 by 48-ft. semi-trailer or be skid-mounted if stationary. Pretreatment units can be used to heat materials to kill pathogens. Air scrubbers can be used to capture odors.
In the past, cyclonic drying systems relied on high temperature, which can destroy nutrient values.
An advantage to the system is the module design with volumes as low as 5 tons per hour, processing volume, adds Balvanz. If an ethanol plant needs to process 20 tons of distillers grains per hour, it can use four units.
"This gives them redundancy," he explains. "If one unit shuts down, the other three continue operating. It also allows them up to four different end product streams, taking the product off at different moisture and/or protein levels."
The system offers huge savings as well. Balvanz reports that capital costs for his system are less than half that of alternative drying systems and operating costs are 50 to 75 percent less.
GRRO is now working with a number of companies to evaluate the technology in their industries. And the company is working on recovering heat to power generators and also reducing the size of the modules. "Our goal is to get a unit no bigger than a desk," says Balvanz.
Contact: FARM SHOW Followup, Loran Balvanz, Global Resource Recovery Organization, 1707 21st Street, Eldora, Iowa 50627 (ph 641 939-7476 or 800 800-1812; fax 641 939-7539; info@grrotempest.com; www.grrotempest.com)
To read the rest of this story, download this issue below or click
here to register with your account number.