You have reached your limit of 3 free stories. A story preview is shown instead.
To view more stories
(If your subscription is current,
click here to Login or Register.)
Grain Dryer Runs Quiet, Uses 1/3 Less Fuel
A revolutionary grain dryer design is on the ground and running this fall. The first commercial DryTech units came out of the factory in early October. If they live up to the performance of an earlier prototype, the new design will catch on fast with commercial grain producers.
"Our numbers indicate that with LP
..........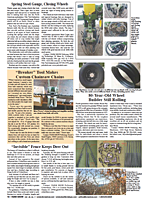
You must sign in, subscribe or renew to see the page.
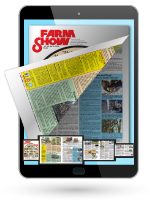
You must sign in, subscribe or renew to see the flip-book
Grain Dryer Runs Quiet, Uses 1/3 Less Fuel GRAIN DRYERS Grain Dryers (29E) 29-6-33 A revolutionary grain dryer design is on the ground and running this fall. The first commercial DryTech units came out of the factory in early October. If they live up to the performance of an earlier prototype, the new design will catch on fast with commercial grain producers.
"Our numbers indicate that with LP at $1.28 per gallon, our costs, including electricity, run between 1.2ó and 1.3ó per bushel per point," says Brad Ross, sales manager, DryTech. "Most people tell us that drying in a conventional dryer costs them between 2ó and 5ó per bushel per point."
With LP prices projected to soar by as much as 60 percent this year, DryTech's cost savings will soar, too. Ross reports the new dryer may also qualify for energy rebate credits.
Equally exciting is the new dryer's affect on grain quality. The flow-through design eliminates the potential for hot spots and even makes it possible to add moisture to over-dried grain and beans.
Ross compares the dryer design to the conveyer belt used in pizza ovens or hamburger grills. The grain continuously moves from a 125-bu. surge hopper through the 35-ft. long dryer unit or a 24-in. wide chain mesh conveyer belt. Hot air is pulled through the stainless steel belt by fans, the biggest of which requires a 3-hp motor. Total fan power is only 15 hp.
Ross says the key to the low power usage is that the fans are pulling the heat through, not pushing it. The lower power fans also reduce noise levels. Unlike most commercial drying systems, conversations can be carried on in a normal voice within 10 to 15 ft. of the dryer.
While it's not legal to add moisture to over dried grain directly, it is acceptable to add moisture to the heated air. With the DryTech dryer, moisture can be added to the hot air to "humidify" grain or beans.
"If you take $8 beans out of a bin at 8 to 10 percent moisture and can enhance moisture levels a couple of points, clean them and send them to town, you've added 16ó per bushel to your price," says Ross.
Grain quality is also enhanced by the built-in screens that remove dirt and chaff and the design of the cores that pull the conveyer belt. As the belt passes over the core, its irregular surface cleans out any fines or seeds that have lodged and could impede airflow. Fines are collected in a lower chamber area equipped with a built-in auger.
A touch screen control panel lets the operator set moisture levels and walk away. Humidity sensors read incoming and outgoing air and adjust the dryer to meet desired target moisture levels.
DryTech dryers are designed as grain drying modules. Each unit is capable of fully drying 600 bu./hour, with each burner capable of heating two modules. Hooked up in tandem, a single control panel can handle up to four modules for a 2,400 bu./hour capacity.
"If a farmer prefers to steep his grain instead of running it through a cooling chamber, capacity increases to 800 to 825 bu. per hour," says Ross. "We also offer the DT 1200 that has a 48-in. wide belt and a 1,000 bu./hour capacity cooled or 1,200 to 1,300 bu./hour steeped."
An added advantage of the compact design is portability. DryTech is offering three variations on their units. A permanent, stationary unit hooked into a standard 120-amp system will retail for about $65,000. Their Farm-duty Mobile unit is designed for use at remote grain bins. It will retail for up to $8,000 more, depending on whether the buyer has his own flatbed and generator. A third unit, the Interstate Highway Mobile, is equipped to meet all DOT regulations.
"Farmers can take our dryer to the grain bins on a remote farm instead of hauling grain back and forth to a dryer on a second farm and then back to the first farm's bins," says Ross.
While DryTech is a new company, the parent company CemenTech is well established and ships products to 41 countries. Ross says dryer customers like knowing an established company is behind the dryer business. It is CemenTech's expertise in volumetric proportioning and conti
To read the rest of this story, download this issue below or click
here to register with your account number.