You have reached your limit of 3 free stories. A story preview is shown instead.
To view more stories
(If your subscription is current,
click here to Login or Register.)
Garbage Truck Cattle Feeder
Tired of fixing broken floor chains in silage wagons and making multiple trips to fill cattle bunks with silage, Tracy Palechek and his son Chris went looking for alternatives. When Palechek saw the box from a garbage truck at a local salvage yard, he figured it might work.
"At 650 cu. ft., it had nearly three t
..........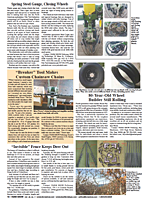
You must sign in, subscribe or renew to see the page.
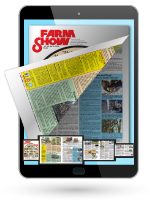
You must sign in, subscribe or renew to see the flip-book
Garbage Truck Cattle Feeder LIVESTOCK Feeding Equipment 30-1-11 Tired of fixing broken floor chains in silage wagons and making multiple trips to fill cattle bunks with silage, Tracy Palechek and his son Chris went looking for alternatives. When Palechek saw the box from a garbage truck at a local salvage yard, he figured it might work.
"At 650 cu. ft., it had nearly three times the capacity of our silage wagon," explains Palechek. "With the double acting cylinder in it to push the silage to the front, we could get away from floor chains that always seemed to break when the wagon was full."
The first step was to cut the top off to make it easy to fill. They then mounted it on a Deere 300 stackwagon bed. Palechek figured that the walking beam axle would spread out the load on soft ground in the spring.
They built a beater system for the front of the box out of salvaged pto shafts. The shafts had come from silage cutters and been replaced due to faulty bearings. Sections of angle iron were welded to the shafts. Worn silage cutter knives welded to the angle irons serve as teeth on the beaters.
A gearbox from a silage cutter mounts on the beater and provides power through an old truck transmission. The same system also powers the elevator that Palecheck mounted in front of the beater.
"We can change speeds of the elevator and the beater," says Palechek.
Just when the two thought they were finished, they discovered that more modifications were needed. The hydraulic system on their tractors couldn't pump out the 40-gpm flow rate needed by the 12-ft. double acting cylinder.
"We took it out and replaced it with a single acting cylinder from a gravel truck that only needed about 20 gpm," says Palecheck. "That would push the silage out, but we still needed to pull the cylinder back."
The solution was a seemingly complex system involving a second cylinder and a set of pulleys mounted vertically to the back wall of the box. Palecheck hooked an 8-in. cylinder with a 2-in. rod and a reach of 36 in. next to the push cylinder and connected to the same hydraulic circuit. He attached a length of cable to the end of the rod and ran it through four pulleys for a 4 to 1 multiplier and a fifth one to change direction, finally attaching it to the push wall. As a result, when the rod extends 3 ft., the cable moves 12 ft., enough to return the large cylinder and its push wall to the rear of the box again.
"The competing hydraulic pressures keep the cables tight," explains Palechek. "Once we got the two cylinders working, the thing worked pretty good. Even with replacing the cylinders, we probably don't have $4,000 in it. A new wagon would cost around $35,000 and wouldn't hold nearly as much."
Contact: FARM SHOW Followup,
Tracy Palechek, RR 2, Ponoka, Alberta, Canada T4J1R2 (ph 403 783-2708).
To read the rest of this story, download this issue below or click
here to register with your account number.