You have reached your limit of 3 free stories. A story preview is shown instead.
To view more stories
(If your subscription is current,
click here to Login or Register.)
Grapple Fork Made From Old Cultivator Shanks
Heavy duty, loader-mounted grapple forks can be made from old cultivator shanks, says David McKenzie, Delisle, Sask., who uses his home-built grapple on a Zetor tractor equipped with a Buhler front-end loader and a 7-ft. bucket.
"I saved a lot of money and it's a great grapple. Cultivator shanks are always buil
..........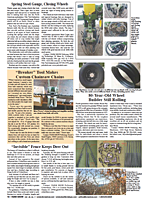
You must sign in, subscribe or renew to see the page.
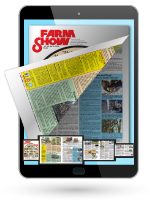
You must sign in, subscribe or renew to see the flip-book
Grapple Fork Made From Old Cultivator Shanks CULTIVATORS Cultivators (58C) 30-1-26 Heavy duty, loader-mounted grapple forks can be made from old cultivator shanks, says David McKenzie, Delisle, Sask., who uses his home-built grapple on a Zetor tractor equipped with a Buhler front-end loader and a 7-ft. bucket.
"I saved a lot of money and it's a great grapple. Cultivator shanks are always built strong so they stand up to a lot of tough use," says McKenzie, who used scrap metal to build the grapple fork's frame.
The grapple fork has four 2-ft. long curved shanks spaced 2 ft. apart. Each shank measures 1 in. thick by 2 in. wide. After cutting the shanks off the cultivator, he straightened them slightly in a press. Then he cut the ends down to points. The shanks are clamped to a length of 4-in. sq. tubing, which in turn is clamped to a metal frame that bolts onto the back of the bucket.
A pair of hydraulic cylinders are used to raise and lower the entire unit.
"I've used it for years but have never had a shank bend or break," says McKenzie. "I use the grapple fork on my cow-calf operation to handle everything from round bales to manure to loose chopped hay. The forks open up about 7 ft. high. I came up with the idea after I saw neighbors bending or breaking the teeth on their commercial grapple forks.
"I spent only about $500 to build it, whereas commercial models sell for $2,000 or more. I paid $400 for the two hydraulic cylinders."
McKenzie had earlier built another grapple fork for his Case tractor equipped with a Massey Ferguson loader. "The loader came equipped with a combination bucket, in which you could unbolt a steel plate from forks at the bottom of the bucket. However, the forks were too small so I made longer forks."
Contact: FARM SHOW Followup, David McKenzie, P.O. Box 614, Delisle, Sask., Canada S0L 0P0 (ph 306 493-8127).
To read the rest of this story, download this issue below or click
here to register with your account number.