Mini Biodiesel Refinery Up And Running
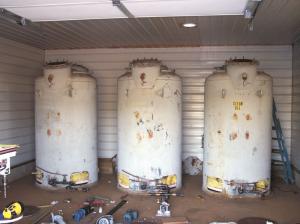 ✖  |
Every community could have its own biodiesel plant if they followed the lead of Jay Idzorek and Ryan Hunt. The two have pieced together tanks and pipe to start a biodiesel refinery in northern Minnesota called Green Range Renewable Energy.
"Anybody can produce biodiesel for themselves," says Idzorek. "All you need is a 55-gal. barrel, an agitator like a paint paddle, lye for a catalyst, a barrel of methanol, and the grease or oil you're going to refine."
Idzorek admits the process of doing batch refining is a little complicated, but not too difficult to master. He had been making biodiesel in his garage for several years before he and Hunt decided to build a large-scale batch system. They hope to be in full production soon with initial goals of a quarter million gallons per year.
"We hope to get to a million gallons a year, producing for the local market," says Idzorek, who plans to sell direct to several local trucking fleets and interested individuals.
Whether your goal is 50 gallons or 250,000 gallons, the process is essentially the same. If local restaurants have used fryer oil and grease that they want to get rid of, your feedstock may even be free. Idzorek adds that some lab equipment, such as a pH tester and a scale accurate to 1/10 of a gram, are also required.
"You need to wear a good respirator, eye protection, apron and gloves," says Idzorek. "When you add the catalyst lye (sodium hydroxide) to the methanol, you create sodium methoxide which is an extremely caustic liquid, and vapors can burn mucous membranes. I always mix mine outdoors and stand upwind just to be sure."
The goal of the process is to use the catalyst to separate the glycerin in the oil from the refined oil or biodiesel. Once it has separated, it can be siphoned off. An easier way, suggests Idzorek, is to install ball valves on the sides of the barrel, one at the bottom of the barrel and one about 8 to 10 in. up.
For a 50-gal. batch, collect about 40 gal. of used vegetable oil. First determine the pH of the oil. This requires heating it. Idzorek uses a barrel band heater that goes around the base of a barrel and plugs into any outlet. Once it has been heated and stirred, he checks the pH level, which tells him how much catalyst is needed.
This is perhaps the most complicated step in the entire process. Idzorek highly recommends visiting the website: http://www.journeytoforever.org/biodiesel.html for detailed directions.
Once the amount of lye has been determined, it is added to the methanol and the mix is added to the oil. Idzorek adds 20 percent, or in this case 10 gal. of methanol to 40 gallons of oil.
Using the paint paddle or other agitator, the oil mixture is then agitated for about 2 hours. Then Idzorek lets it sit over night until the glycerin separates out. The barrel and contents are again warmed before either draining off the glycerin from the bottom valve or the biodiesel from the top valve. He runs the biodiesel through a 30-micron screen to remove large particles and into a second barrel. After sitting for about a week, excess or free methanol will collect on the surface. Commercial grade biodiesel requires that all of the free methanol be removed. Idzorek uses the two-valve barrel system to remove most of it.
"I have never had any problems with a little free methanol floating around in the biodiesel I use in my pickup, skid steer or backhoe," he says. "For $30 worth of methanol, I get about 40 gallons of biodiesel and 10 gallons of glycerin."
Contact: FARM SHOW Followup, Green Range Renewable Energy, Attn: Jay Idzorek, P.O. Box 354, Ironton, Minn. 56455 (ph 218 545-2186; fax 218 545-7337; greenrange@ emily.net; www.greenrange energy.com).
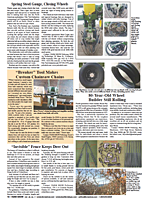
Click here to download page story appeared in.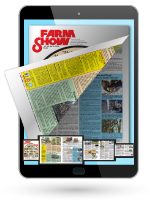
Click here to read entire issue
Mini Biodiesel Refinery Up And Running ENERGY Miscellaneous 30-2-28 Every community could have its own biodiesel plant if they followed the lead of Jay Idzorek and Ryan Hunt. The two have pieced together tanks and pipe to start a biodiesel refinery in northern Minnesota called Green Range Renewable Energy.
"Anybody can produce biodiesel for themselves," says Idzorek. "All you need is a 55-gal. barrel, an agitator like a paint paddle, lye for a catalyst, a barrel of methanol, and the grease or oil you're going to refine."
Idzorek admits the process of doing batch refining is a little complicated, but not too difficult to master. He had been making biodiesel in his garage for several years before he and Hunt decided to build a large-scale batch system. They hope to be in full production soon with initial goals of a quarter million gallons per year.
"We hope to get to a million gallons a year, producing for the local market," says Idzorek, who plans to sell direct to several local trucking fleets and interested individuals.
Whether your goal is 50 gallons or 250,000 gallons, the process is essentially the same. If local restaurants have used fryer oil and grease that they want to get rid of, your feedstock may even be free. Idzorek adds that some lab equipment, such as a pH tester and a scale accurate to 1/10 of a gram, are also required.
"You need to wear a good respirator, eye protection, apron and gloves," says Idzorek. "When you add the catalyst lye (sodium hydroxide) to the methanol, you create sodium methoxide which is an extremely caustic liquid, and vapors can burn mucous membranes. I always mix mine outdoors and stand upwind just to be sure."
The goal of the process is to use the catalyst to separate the glycerin in the oil from the refined oil or biodiesel. Once it has separated, it can be siphoned off. An easier way, suggests Idzorek, is to install ball valves on the sides of the barrel, one at the bottom of the barrel and one about 8 to 10 in. up.
For a 50-gal. batch, collect about 40 gal. of used vegetable oil. First determine the pH of the oil. This requires heating it. Idzorek uses a barrel band heater that goes around the base of a barrel and plugs into any outlet. Once it has been heated and stirred, he checks the pH level, which tells him how much catalyst is needed.
This is perhaps the most complicated step in the entire process. Idzorek highly recommends visiting the website: http://www.journeytoforever.org/biodiesel.html for detailed directions.
Once the amount of lye has been determined, it is added to the methanol and the mix is added to the oil. Idzorek adds 20 percent, or in this case 10 gal. of methanol to 40 gallons of oil.
Using the paint paddle or other agitator, the oil mixture is then agitated for about 2 hours. Then Idzorek lets it sit over night until the glycerin separates out. The barrel and contents are again warmed before either draining off the glycerin from the bottom valve or the biodiesel from the top valve. He runs the biodiesel through a 30-micron screen to remove large particles and into a second barrel. After sitting for about a week, excess or free methanol will collect on the surface. Commercial grade biodiesel requires that all of the free methanol be removed. Idzorek uses the two-valve barrel system to remove most of it.
"I have never had any problems with a little free methanol floating around in the biodiesel I use in my pickup, skid steer or backhoe," he says. "For $30 worth of methanol, I get about 40 gallons of biodiesel and 10 gallons of glycerin."
Contact: FARM SHOW Followup, Green Range Renewable Energy, Attn: Jay Idzorek, P.O. Box 354, Ironton, Minn. 56455 (ph 218 545-2186; fax 218 545-7337; greenrange@ emily.net; www.greenrange energy.com).
To read the rest of this story, download this issue below or click
here to register with your account number.