2006 - Volume #30, Issue #3, Page #39
[ Sample Stories From This Issue | List of All Stories In This Issue | Print this story
| Read this issue]
Air Conditioner Provides "Air" On Service Truck
"I work for a local International truck dealer and use my 1992 Dodge Dakota 2-WD pickup as a service truck. To provide the truck with on-board compressed air, I mounted an air conditioner compressor out of a Chrysler car on the pickup's 2.5-liter, 4-cyl. gas engine," says Robert Pike, Hollandale, Minn. Pike uses the compressor to fill truck tires with air and to operate small impact wrenches. "It cost very little to set up and doesn't take up any space in the truck box like a commercial gas engine-driven compressor would," he told FARM SHOW.
Pike's pickup doesn't have power steering or air conditioning, which left plenty of room to install the belt-driven air conditioning compressor. It came out of a 1970's Chrysler. An electric pressure switch is used to turn the compressor clutch on or off.
He brazed air hose fittings to the compressor and ran the hose to a home-built air tank mounted behind the cab. He made the "tank" by welding four 4-in. dia. steel pipes together, one on top of the other.
He mounted a control panel just behind the driver's door, complete with air gauge, regulator, and pressure switch controls.
"It works great for filling tires and to operate small air tools, but not quite as well for operating die grinders and other large impact tools. The air tanks don't provide as much capacity as I had hoped," says Pike. "I plan to make the same conversion on a 1973 Dodge van equipped with a 225 cu. in., slant 6-cylinder engine so that I can use a bigger compressor. When you run the tubing from the compressor to the tanks, be sure to use a check valve in order to keep air from back-feeding through the compressor whenever it's not running."
The hardest part of the job was mounting the compressor to the engine and getting it lined up with the other pulleys. "To make the job easier, I took one of the original brackets that was used to mount the compressor to the Chrysler engine and cut an exact copy out of a sheet of 1/4-in. thick steel. Then I mounted one bracket on either side of the compressor so that a bolt could be used as a pivot, extending from one end of the compressor to the other."
He says he used the Chrysler compressor because it has a separate crankcase that allows for more reliable operation than rotary piston-type pumps, which require lubricant to be fed into them as they're running. "The Chrysler" compressor is built a lot like internal combustion engines equipped with a crankshaft, rods, reciprocating pistons, and a crankcase," says Pike. "Since the compressor already had a clutch, all I had to do was to wire it into the pressure control switch and to an on/off switch. The switch is just like the ones on ordinary plug-into-the-wall-outlet air compressors. You can set the cut-out pressure and the differential pressure with small screws inside the switch."
He used copper refrigerant tube to make an intercooler of sorts for the compressor. It's mounted to the radiator fan bracket. "I might switch to an aftermarket transmission cooler, because the weight of the copper one may be putting too much stress on my pickup's radiator," notes Pike.
Contact: FARM SHOW Followup, Robert (Fish) Pike, 27969 825th Ave., Hollandale, Minn. 56045 (ph 507 383-3985).
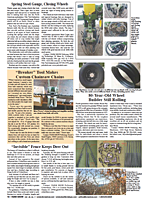
Click here to download page story appeared in.
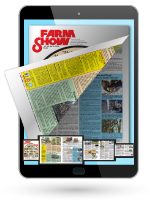
Click here to read entire issue
To read the rest of this story, download this issue below or click here to register with your account number.