"Breakthrough" Systems Makes Building Panels Out Of Straw
According to the story about the three little pigs, straw isn't a good building material. But that hasn't stopped David R. Ward, a former building contractor from Ashland, Ore., from putting 10 years of research into his Strawjet process that converts straw into a low-cost building material.
Ward was recently named the 2006 Inventor of the Year by The History Channel, National Inventors Hall of Fame Foundation, and Time Magazine for his invention that's expected to make a significant global impact. He beat out nearly 4,500 other inventors and was awarded a $25,000 grant.
His Strawjet technology is actually a multi-stage system that involves four machines.
"The Strawjet system harnesses the strength of straw by tightly bundling the plant stems into tightly-bound 2-in. diameter cables. These cables can be used in a variety of ways," says Ward.
Three prototypes of the main field machine have been built so far. Here's how the system works:
The machine works a lot like a baler. It picks up a windrow of straw, and makes four cables out of it. These four cables are dropped on the ground behind the machine. Depending on the crop, a clay-based binding material can be applied to the straw during this process to keep the individual pieces from sliding against each other. In this case, the cables then need to dry in the field for a day or two. Some crops, such as sunflowers or cotton, don't require this application.
Another machine picks up the four cables, cuts them into 8-ft. lengths, and weaves them into a mat, similar to a giant bamboo window blind. The machine then rolls the mats into 5-ft. dia. rolls.
A third machine unrolls the mats and sprays on a layer of binding material to bond one layer of mat to another in stacks, until the desired thickness is achieved.
Once the stacks are dry, a fourth machine cuts them to size, based on the design of the building to be constructed. At this point the machines can also be used to cut out windows and doors, saving labor after they're delivered to the construction site. At the building site, all sides of the panels are then coated with plaster.
Ward points out that Strawjet panels replace the drywall, studs, insulation, and siding.
Strawjet Inc., hopes to introduce a stationary, hand-fed version of the machine in countries where people harvest small grain crops by hand. Although the hand-fed machine will be more labor intensive, it will be able to turn almost any type of straw or fiber into a uniform building material.
Ward has successfully experimented with the straw from wheat, hemp, flax, cotton, sunflowers, tobacco, rice, bamboo and palm fronds.
He expects the Strawjet system to be priced at under $200,000.
Contact: FARM SHOW Followup, ASET, 5765 Colver Road, Talent, Ore. 97540 (ph 541 535-5822; dward@ jeffnet.org or greeninventor@jeffnet.org; www.strawjet.com or www.greeninventor.org).
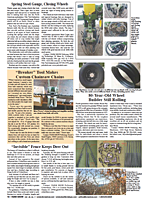
Click here to download page story appeared in.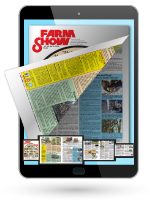
Click here to read entire issue
Breakthrough Systems Makes Building Panels Out Of Straw BUILDINGS Miscellaneous According to the story about the three little pigs straw isn t a good building material But that hasn t stopped David R Ward a former building contractor from Ashland Ore from putting 10 years of research into his Strawjet process that converts straw into a low-cost building material
Ward was recently named the 2006 Inventor of the Year by The History Channel National Inventors Hall of Fame Foundation and Time Magazine for his invention that s expected to make a significant global impact He beat out nearly 4 500 other inventors and was awarded a $25 000 grant
His Strawjet technology is actually a multi-stage system that involves four machines
The Strawjet system harnesses the strength of straw by tightly bundling the plant stems into tightly-bound 2-in diameter cables These cables can be used in a variety of ways says Ward
Three prototypes of the main field machine have been built so far Here s how the system works:
The machine works a lot like a baler It picks up a windrow of straw and makes four cables out of it These four cables are dropped on the ground behind the machine Depending on the crop a clay-based binding material can be applied to the straw during this process to keep the individual pieces from sliding against each other In this case the cables then need to dry in the field for a day or two Some crops such as sunflowers or cotton don t require this application
Another machine picks up the four cables cuts them into 8-ft lengths and weaves them into a mat similar to a giant bamboo window blind The machine then rolls the mats into 5-ft dia rolls
A third machine unrolls the mats and sprays on a layer of binding material to bond one layer of mat to another in stacks until the desired thickness is achieved
Once the stacks are dry a fourth machine cuts them to size based on the design of the building to be constructed At this point the machines can also be used to cut out windows and doors saving labor after they re delivered to the construction site At the building site all sides of the panels are then coated with plaster
Ward points out that Strawjet panels replace the drywall studs insulation and siding
Strawjet Inc hopes to introduce a stationary hand-fed version of the machine in countries where people harvest small grain crops by hand Although the hand-fed machine will be more labor intensive it will be able to turn almost any type of straw or fiber into a uniform building material
Ward has successfully experimented with the straw from wheat hemp flax cotton sunflowers tobacco rice bamboo and palm fronds
He expects the Strawjet system to be priced at under $200 000
Contact: FARM SHOW Followup ASET 5765 Colver Road Talent Ore 97540 ph 541 535-5822; dward@ jeffnet org or greeninventor@jeffnet org; www strawjet com or www greeninventor org
To read the rest of this story, download this issue below or click
here to register with your account number.