2006 - Volume #30, Issue #4, Page #39
[ Sample Stories From This Issue | List of All Stories In This Issue | Print this story
| Read this issue]
He Makes His Own Square Tubing
![]() |
![]() |
"The lightest weight square tubing I could find in the size I needed was 11 gauge, which was too heavy," says Petterson. "I decided to use 18 ga. stainless sheet metal to make my own tubing. But instead of cutting the sheet metal into strips and welding them together, which would have created a lot of distortion, I decided to build a hydraulic shop press. It allowed me to bend all four sides of the sheet metal into square tubes and greatly reduced the amount of welding."
The 24-in. wide press consists of a pair of 1 1/2-in. wide steel bars that form a bottom die. The distance between the bars can be adjusted by adding or subtracting spacers, which mount on a pair of threaded bolts that extend through both bars.
Two more horizontal threaded bolts, one on each side, are used to keep the dies in place. A pair of vertical threaded bolts, one on each side, serve as guides to keep the top punch perpendicular to the dies. Springs on the guides help return the punch when the hydraulic jack is released.
After marking where to bend the sheet metal, Petterson slip it under the punch and then presses the jack down until it makes contact with the sheet metal. The first bend leaves a 1/2-in. wide strip of metal, which serves as a lap joint that makes it easier to weld the seams together. The other bends are then made in the proper sequence until the square is closed up.
"This same shop press can be used on any project that requires multiple bends," says Petterson. "To bend thicker material I just open up the die spacing."
Each cross has six metal cloverleafs on it. To make cutting the cloverleafs an easier job, he came up with a jig that works something like a protractor. The main body has three hinged tabs on it, with a hole near the end of the tab where he inserts the head on his plasma cutter. The main body is then clamped in place on the sheet metal. Small bolts form the hinge points, which the plasma torch pivots around. "All the cloverleafs had to look the same, and this was the easiest way to make them all look alike. The circle radius always stays the same when using this simple tool," notes Petterson.
Contact: FARM SHOW Followup, Duane Petterson, 5894 409th St., Rice, Minn. 56367 (ph 320 656-5279; dspetterson@juno.com).
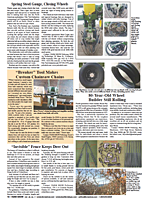
Click here to download page story appeared in.
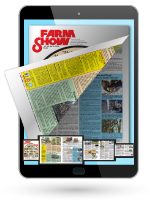
Click here to read entire issue
To read the rest of this story, download this issue below or click here to register with your account number.