You have reached your limit of 3 free stories. A story preview is shown instead.
To view more stories
(If your subscription is current,
click here to Login or Register.)
Swather-Rake WIndrows Field Fast
Chuck Palmer rakes 20 acres per hour with his self-propelled twin tandem Kuhn rake. The adjustable rake lets him clear a 12 or 16-ft. swath, depending on how he sets the rake and whether he uses one or both sides.
"I bought it from Dave Holt, a local farmer who has since passed away," says Palmer. "His uncle use
..........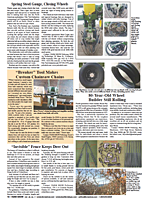
You must sign in, subscribe or renew to see the page.
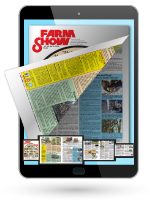
You must sign in, subscribe or renew to see the flip-book
Swather-Rake WIndrows Field Fast SWATHERS 30-5-28 Chuck Palmer rakes 20 acres per hour with his self-propelled twin tandem Kuhn rake. The adjustable rake lets him clear a 12 or 16-ft. swath, depending on how he sets the rake and whether he uses one or both sides.
"I bought it from Dave Holt, a local farmer who has since passed away," says Palmer. "His uncle used to call him the Thomas Edison of farm machinery. He could do most anything. When a dealer wouldn't give him anything for his Deere 3830 swather on trade, he decided to make a self-propelled rake with it."
Holt dropped the header and welded a clevis hitch to the center of the front cross frame on the swather. He then modified an old Kuhn twin tandem rake to be pushed instead of trailing. Holt swapped the tandem units to opposing sides and replaced the 2-pt. hitch with a bar that connects with the swather at the new clevis.
Pushing the rake required stabilizing the bar against the swather. To accomplish this, Holt welded and bolted a piece of 4 by 5-in. channel iron centered on and perpendicular to the 3 1/2 by 6 1/2-in. tubular steel tow bar. Eyebolts were fastened to either end of the cross bar and connected in turn to the upper arms that previously supported the header frame.
The cross bar was also anchored to the swather from its underside. At either end of the cross bar, a short section of 4 by 4-in. tubular steel was welded in place. Welded to the bottom of the 4 by 4 pieces are short pieces of 2 by 6-in. channel iron, which in turn rests on what were the lower support arms for the header.
Holt found out that these five points of connection were not enough to push the rake, especially on turns. "The torque was too great," says Palmer. "Holt attached steel cables to the ends of the cross bar and angled them back about 3 to 4 ft. to the hitch bar, just ahead of the gear box on the rake for added support."
Palmer found that even the cables couldn't handle the strain. When one of them snapped he had a local metal fabricator weld 6-ft. long 2 by 6-in. channel iron from the ends of the cross bar to the tow bar. The steel A-frame handles the torque fine.
Getting power to the pto driven rake heads was handled by mounting a sprocket to the swather header drive. A no. 60 chain connects it to a second drive sprocket with a splined pto stub in line with the rake pto shaft mounted below the tow bar.
"The rake goes into gear just like the header used to, using the same controls," explains Palmer.
Holt mounted a caster wheel at the end of the new hitch bar and uses the header lift hydraulic hoses, activated by the header lift pedal in the cab, to power the rake lift cylinders. Road transit is a snap with the two rakes lifted into vertical position. Palmer reports he can travel at about 15 mph between fields.
"It works great," he says. "It takes the place of a tractor and a couple of rakes."
Contact: FARM SHOW Followup, Charles Palmer, W4211 Palmer Rd., Lake Geneva, Wis. 53147 (ph 262 248-9261).
To read the rest of this story, download this issue below or click
here to register with your account number.