You have reached your limit of 3 free stories. A story preview is shown instead.
To view more stories
(If your subscription is current,
click here to Login or Register.)
Home-Built Log Processor
Wood processors don't come cheap at $30,000 or more. When you've got a part-time firewood business, that's hard to justify. Lewis Legge figured he could build his own using parts put together from a multitude of different sources. He can now cut up and split two cords per hour, working with logs from 4 to 22 in. in dia
..........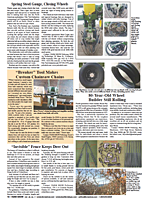
You must sign in, subscribe or renew to see the page.
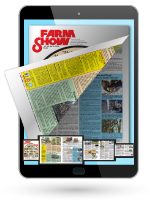
You must sign in, subscribe or renew to see the flip-book
Home-Built Log Processor WOODLOT EQUIPMENT Miscellaneous 31-1-4 Wood processors don't come cheap at $30,000 or more. When you've got a part-time firewood business, that's hard to justify. Lewis Legge figured he could build his own using parts put together from a multitude of different sources. He can now cut up and split two cords per hour, working with logs from 4 to 22 in. in diameter.
"I saw a picture of one and got an idea of how they work and what they do," he says. "It took me about a year to gather all the parts, about two months solid to put them together, and about $7,000 out of pocket."
What Legge got for his efforts was the "Wood Butcher". Everything is hydraulically powered, and each step is controlled separately by a manually activated control.
Legge says his best investment was in a home study course on hydraulics. "I bought it to learn more about the subject, and I know it saved me time and money simply by not overbuilding," he says.
His plan called for two separate hydraulic systems. A saddle tank off an old semi-tractor serves as oil reservoir. One pump came off an old highway truck and does 25 to 30 gpm at 2,500 psi. A second pump pulled off a tractor puts out 25 to 30 gpm at 1,500 psi.
"With these two pumps, you need that big a reservoir just to keep the oil cool," he says, noting that a rule of thumb is a gallon of reservoir volume for every gallon pumped.
The 366 Chevy engine came off a wrecked truck, and trailer axles came from an old horse trailer. While most of the orbit motors and other parts were picked up used, Legge did buy a new hydraulic powered chain saw bar, chain and sprocket.
"It is a very aggressive 3/4 pitch saw used on tree harvesters," he explains. "I built the oiler to supply the bar as I wanted something that would pump old axle grease. It's nice and sticky."
Legge rigged up a hydraulic cylinder as a pump for bar oil. Using a spring on one end of the cylinder as a trigger, he set it so pulling the lever to activate the saw would also activate the cylinder. He had removed the rod, but retained the piston action. Instead of rod, the piston pulls axle grease into the cylinder through a check valve as it's retracted. On the return, it pushed grease out and onto the chain and bar.
The "Wood Butcher" sits on a frame made from I-beams. Wood is split on another I-beam that's 12 in. deep by 10 in. wide and powered by a 5-in. ram.
Logs are set on a table fabricated from 2 by 4-in. tubing, which also creates a channel for the chain on which the logs ride. The chain is old elevator chain from a Massey 21A combine. Logs are carried to a trough with a green ash bed and more paddle elevator chain that conveys the logs to the chain saw. Separate orbit motors power each set of chains.
A flexible rod hanging in the path of the log signals to Legge that the correct length has been reached for sawing. A small hydraulic cylinder moves the chain saw into position and down through the log while a high-speed orbit motor powers the chain.
When the chunk falls into the splitting box, Legge can adjust the splitter with one cylinder before activating the 5-in. ram.
The large hydraulic pump supplies the chain saw and the splitter, while the smaller one handles all the individual orbit motors and cylinders.
"There is a chunk going through the splitter about every 10 seconds," says Legge, who says all the time and effort was well worth it. "Bending over logs with a chain saw is a fate worse than death. This thing handles every kind of tree from cottonwood to ash and cedar."
Contact: FARM SHOW Followup, Lewis Legge, Legge's Portable Milling, 3212 115 Ave. S.E., Valley City, N. Dak. 58072 (ph 701 845-4762; fax 701 845-9226; jlegge@daktel.com).
To read the rest of this story, download this issue below or click
here to register with your account number.