You have reached your limit of 3 free stories. A story preview is shown instead.
To view more stories
(If your subscription is current,
click here to Login or Register.)
Liquid Manure Composting System
In only three days, Herman Tripp's patented "Compo*Starr" system produces composted "non-smelly" material that he says makes excellent fertilizer. It'll take care of up to a 600-sow operation.
Through slatted floors, Tripp catches all of the sows' waste in a 2-ft. wide by 1-ft. deep gutter system. The waste move
..........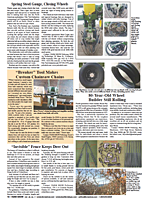
You must sign in, subscribe or renew to see the page.
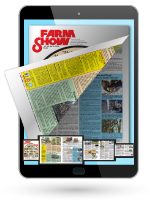
You must sign in, subscribe or renew to see the flip-book
Liquid Manure Composting System MANURE HANDLING Equipment 31-2-19 In only three days, Herman Tripp's patented "Compo*Starr" system produces composted "non-smelly" material that he says makes excellent fertilizer. It'll take care of up to a 600-sow operation.
Through slatted floors, Tripp catches all of the sows' waste in a 2-ft. wide by 1-ft. deep gutter system. The waste moves down to an underground holding tank. A back-flush system ensures that no solids are left behind in the gutters.
Next, the manure is mixed with ground-up corn stalks which are conveyed into the Compo*Starr unit - a 20-in. auger mixer inside a 24-in. plastic tube. Manure and stalks are mixed at a ratio (by weight) of 70 percent manure and 30 percent stalks. The Compo*Starr mixes it for three days.
The system produces 6 to 8 tons of commercially saleable fertilizer per day, which steadily trickles out of the tube into a pile or truck.
"We kept experimenting until we found the right ratio of corn stalks to manure," Tripp says.
He adds that by very slowly and continuously mixing the liquid pig waste and the fiber, he learned that it would heat up. His recipe brings the overall moisture content down to an ideal range of 50 to 60 percent. The natural increase in temperature results in composting action and creates a "very powerful fertilizer" with no smell.
"Within 24 to 36 hours it gets hot - usually between 140 and 160 degrees -which lasts for two full days. Then on the third day, it begins to cool down and goes back to the original temperature of 60 to 80 degrees, depending on the weather."
Tripp says the steam is captured so no moisture is lost. "Some people have said they detected a slight sweet smell, like dirt," he says. "It's a very potent fertilizer that we're marketing for use on indoor house plants."
The composted machine has a nutritional value of $50 per ton, he says. Two tons will replace $80 to $100 worth of commercial fertilizer.
"I've learned the incredible value of manure and am realizing $148 of value (after costs) per sow, by replacing commercial fertilizer with this material," he says.
Tripp's mixing auger is made out of plastic. It has a stainless steel shaft, and a plastic auger-mixer in a 24-in. dia. plastic tube. He patented the unit four years ago and it has just now received patent protection in Canada.
"We feed everything into the auger, which turns one revolution every two or three minutes. For example, with 600 sows, we have 410 ft. of auger mixer, which mixes the material continuously," he explains. "We use a corn stalk shredder to shred two bales a day of corn stalks."
Tripp has been working on developing this system for 10 years, but he just recently began offering it for sale. He recently sold a system in Missouri. It can be installed under the alleyway of a new barn, or retrofitted to an existing barn. It can be trenched under the ground outside the building, or placed above ground.
About eight inches of Compo*Starr is needed for one sow, he says.
It costs between $100,000 and $150,000 for the tube, auger mixer, power unit and insulation, depending on if it's on a new or existing barn.
Contact: FARM SHOW Followup, Herman and Clara Tripp, 2047-100th St., Patton, Iowa 50217 (ph 515 968-4341; fax 515 968-4347; spring45@wccta.net).
To read the rest of this story, download this issue below or click
here to register with your account number.