You have reached your limit of 3 free stories. A story preview is shown instead.
To view more stories
To view more stories
SUBSCRIBE OR RENEW NOW
(If your subscription is current, click here to Login or Register.)2007 - Volume #31, Issue #2, Page #25
[ Sample Stories From This Issue | List of All Stories In This Issue]
Big Bale Furnace Shreds As It Burns
Burning whole uncut big round bales to heat your shop or house is an idea that has come and gone, as far as Dave Goff is concerned."We think it's far more efficient to burn loose or chopped material," says the owner of Heatwerks, Inc., Morland, Kansas.
FARM SHOW previously featured Go..........
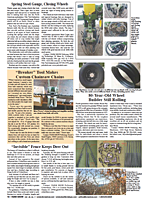
You must sign in, subscribe or renew to see the page.
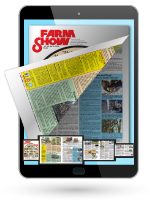
You must sign in, subscribe or renew to see the flip-book
Big Bale Furnace Shreds As It Burns ENERGY Alternative Fuels Burning whole uncut big round bales to heat your shop or house is an idea that has come and gone as far as Dave Goff is concerned
We think it s far more efficient to burn loose or chopped material says the owner of Heatwerks Inc Morland Kansas
FARM SHOW previously featured Goff s Bale Burner which burned big bales to heat farm buildings Vol 27 No 3 He has since redesigned the system to burn any kind of chopped straw grass hay or corn stalks
Chopping up the material makes it burn more efficiently than burning the whole bale says Goff
In most cases the farmer comes up with his own equipment to chop the material and feed it into the burner
The Big Woody system is far more efficient than the bale burner we sold in the past says Goff With the bale burner by the time we got a fire hot enough to matter all the heat was going out the stack There was no way to control the amount of heat so you ended up with either a power plant-sized fire or just a smoulder The Big Woody has multiple water-bearing heat exchangers over the firebox which makes it much more efficient A small pump and a loop of hot water can carry more heat than a giant squirrel cage fan The bale burner was averaging only 3 500 btu s per lb of material burned whereas the Big Woody averages 7 000 btu s
Dairyman Rick Lawrence installed the Big Woody on his farm near Cape Vincent N Y He uses the system to pre-heat hot water that s delivered through underground pipes to his house and dairy barn including the milking parlor
Lawrence uses a Krohn Roto multi-cut round baler on native grass The baler is equipped with knives that slice the grass as they bale it He uses a 3-pt mounted Tomahawk bale shredder to further cut the material and blow it into a Badger self-unloading silage wagon The wagon is equipped with a live floor and is used to unload the material into a modified Badger elevator The elevator delivers the material into the burner s input auger The wagon s live floor and conveyor as well as the elevator are all operated by an electric gear reduction motor
The burner is located in a small shed that Lawrence added onto his farm shop He uses a poly pipe rated for 200 degree water to deliver heated water more than 300 ft to his house and to his shop and dairy barn Lawrence and his neighbor designed an ash stirrer belt-driven by an electric motor to stir the ashes and knock them down through grates into a compartment at the bottom of the burner For now he s using a shovel to remove the ashes but he plans to install an automatic ash removal auger
I think this idea will work for anyone who has excess grass or poor quality hay says Lawrence In some years we have two or three times as much grass hay as we need If the grass gets rained on it s too tough and too low in protein to make good quality feed My total cost for the equipment was less than $25 000 I had been spending about $7 000 per year on oil and propane to heat the same buildings The burner has reduced that to zero so the system will pay for itself in only about three years
The system runs 24 hours a day with the wagon s live floor and conveyor operating continuously on fractional horsepower low energy consumption gear reducers A thermostat is used to turn the burner on and off Lawrence installed a Radio Shack wireless camera and monitor so that he can observe the conveyor from his house
To keep the system s cost down Goff uses as many off-the-shelf parts and components as possible For example a rebuilt big block Chevrolet water pump is used to circulate water throughout the system The water pump belt-driven by a 1/2 hp electric motor pulls hot water out of a nearby reservoir and circulates it through the firebox and heat exchanger then back to the reservoir Rebuilt Chevy water pumps are widely available and can be purchased for only about $30 They work as good as $700 commercial water pumps says Goff
If you need more pressure for longer distances you can feed one pump into another one And if the pump ever fails you can buy another one cheap at any junk yard
The Big Woody is equipped with a shaft-driven stirring mechanism that breaks up free-standing ashes which fall through a grate into the ash box area The burner has a Murphy switch for fail-safe operation
Goff is setting up a similar system for a Minnesota farmer who will use 1-in dia pellets produced from field residues by a local company to dry his grain He has also modified a Kelly Ryan mixer box for delivering poultry manure to the burner The more we work on the manure burner the better we like it says Goff
One of his burners will be used in a Kansas ethanol plant with an estimated production of 40 000 gal per year using shredded corn stalks to produce steam
We don t actually have a steam boiler in operation yet However we ve achieved the continuous feed of alternate fuels with our firebox and are now forging ahead with adapting our cleanable heat exchangers to be able to take steam pressure says Goff This is fairly straightforward stuff because we re only talking 15 to 20 psi on the steam Conventional ethanol plants are running about 100 psi or so but that has more to do with distance requirements etc We should have that unit in full production by midsummer
Contact: FARM SHOW Followup Dave Goff Heatwerks Inc Morland Kan 67650 ph 785 627-6085; davegoff@ruraltel net; www heatwerks net
We think it s far more efficient to burn loose or chopped material says the owner of Heatwerks Inc Morland Kansas
FARM SHOW previously featured Goff s Bale Burner which burned big bales to heat farm buildings Vol 27 No 3 He has since redesigned the system to burn any kind of chopped straw grass hay or corn stalks
Chopping up the material makes it burn more efficiently than burning the whole bale says Goff
In most cases the farmer comes up with his own equipment to chop the material and feed it into the burner
The Big Woody system is far more efficient than the bale burner we sold in the past says Goff With the bale burner by the time we got a fire hot enough to matter all the heat was going out the stack There was no way to control the amount of heat so you ended up with either a power plant-sized fire or just a smoulder The Big Woody has multiple water-bearing heat exchangers over the firebox which makes it much more efficient A small pump and a loop of hot water can carry more heat than a giant squirrel cage fan The bale burner was averaging only 3 500 btu s per lb of material burned whereas the Big Woody averages 7 000 btu s
Dairyman Rick Lawrence installed the Big Woody on his farm near Cape Vincent N Y He uses the system to pre-heat hot water that s delivered through underground pipes to his house and dairy barn including the milking parlor
Lawrence uses a Krohn Roto multi-cut round baler on native grass The baler is equipped with knives that slice the grass as they bale it He uses a 3-pt mounted Tomahawk bale shredder to further cut the material and blow it into a Badger self-unloading silage wagon The wagon is equipped with a live floor and is used to unload the material into a modified Badger elevator The elevator delivers the material into the burner s input auger The wagon s live floor and conveyor as well as the elevator are all operated by an electric gear reduction motor
The burner is located in a small shed that Lawrence added onto his farm shop He uses a poly pipe rated for 200 degree water to deliver heated water more than 300 ft to his house and to his shop and dairy barn Lawrence and his neighbor designed an ash stirrer belt-driven by an electric motor to stir the ashes and knock them down through grates into a compartment at the bottom of the burner For now he s using a shovel to remove the ashes but he plans to install an automatic ash removal auger
I think this idea will work for anyone who has excess grass or poor quality hay says Lawrence In some years we have two or three times as much grass hay as we need If the grass gets rained on it s too tough and too low in protein to make good quality feed My total cost for the equipment was less than $25 000 I had been spending about $7 000 per year on oil and propane to heat the same buildings The burner has reduced that to zero so the system will pay for itself in only about three years
The system runs 24 hours a day with the wagon s live floor and conveyor operating continuously on fractional horsepower low energy consumption gear reducers A thermostat is used to turn the burner on and off Lawrence installed a Radio Shack wireless camera and monitor so that he can observe the conveyor from his house
To keep the system s cost down Goff uses as many off-the-shelf parts and components as possible For example a rebuilt big block Chevrolet water pump is used to circulate water throughout the system The water pump belt-driven by a 1/2 hp electric motor pulls hot water out of a nearby reservoir and circulates it through the firebox and heat exchanger then back to the reservoir Rebuilt Chevy water pumps are widely available and can be purchased for only about $30 They work as good as $700 commercial water pumps says Goff
If you need more pressure for longer distances you can feed one pump into another one And if the pump ever fails you can buy another one cheap at any junk yard
The Big Woody is equipped with a shaft-driven stirring mechanism that breaks up free-standing ashes which fall through a grate into the ash box area The burner has a Murphy switch for fail-safe operation
Goff is setting up a similar system for a Minnesota farmer who will use 1-in dia pellets produced from field residues by a local company to dry his grain He has also modified a Kelly Ryan mixer box for delivering poultry manure to the burner The more we work on the manure burner the better we like it says Goff
One of his burners will be used in a Kansas ethanol plant with an estimated production of 40 000 gal per year using shredded corn stalks to produce steam
We don t actually have a steam boiler in operation yet However we ve achieved the continuous feed of alternate fuels with our firebox and are now forging ahead with adapting our cleanable heat exchangers to be able to take steam pressure says Goff This is fairly straightforward stuff because we re only talking 15 to 20 psi on the steam Conventional ethanol plants are running about 100 psi or so but that has more to do with distance requirements etc We should have that unit in full production by midsummer
Contact: FARM SHOW Followup Dave Goff Heatwerks Inc Morland Kan 67650 ph 785 627-6085; davegoff@ruraltel net; www heatwerks net
To read the rest of this story, download this issue below or click here to register with your account number.