You have reached your limit of 3 free stories. A story preview is shown instead.
To view more stories
(If your subscription is current,
click here to Login or Register.)
He Doubled His Output With Twin Baler Hitch
Building a hitch that can pull and power two balers behind a single tractor just made sense to Dwayne Archer. "We were using large farm tractors and I figured a good operator would be capable of running more than a single baler," he says.
Archer could have gone to a single large baler, but his export market deman
..........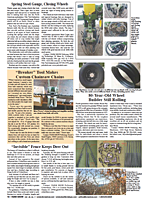
You must sign in, subscribe or renew to see the page.
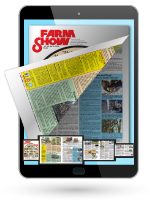
You must sign in, subscribe or renew to see the flip-book
He Doubled His Output With Twin Baler Hitch BALERS Balers 31-3-10 Building a hitch that can pull and power two balers behind a single tractor just made sense to Dwayne Archer. "We were using large farm tractors and I figured a good operator would be capable of running more than a single baler," he says.
Archer could have gone to a single large baler, but his export market demands small squares from his 1,500 acres of timothy hay.
Pulling two balers is the easy part. Powering them and designing a hitch that would let the operator control them individually were the tough parts. To figure it out, Archer turned to two specialists, a fluid power engineer and an electronics engineer. Even with their help, it took several years to complete.
With three years of field use under his belt now, he knows the investment was worth it in labor savings and more efficient use of equipment. It does everything he wanted and more. In addition to baling, the hitch is also used for raking and turning swaths.
"It can handle multiple swath widths and move quickly from field to transport," says Archer. "I can go from baling to rolling down the road in less than three seconds with the baler trailing directly behind the tractor."
The hitch hooks to the tractor's 3-pt. hitch or a drawbar receiver tube. The arch frame of the hitch running back to the axle is 8 by 16-in., 1/4-in steel tubing. The rear axle, including wheels, is from a Jiffy high dump. The 20-in. high axle allows Archer to drive over swaths and an occasional misplaced bale.
Hydraulic power is the key to the hitch unit. The tractor pto powers an 80-gal., two-stage fluid power pump. Oil from that pump powers 55 hp hydraulic motors at each baler hookup point. The motors power the balers' pto shafts and four electric-over-hydraulic valves for each baler.
While he can use the hitch on tractors as small as 110 to 120 hp, he also uses tractors as big as 255 hp.
"One of the key things we did was stage the pump so it could run at reduced engine rpm's and still get appropriate shaft speed out of the motors," says Archer. "An engine speed of 1,640 rpm's at the 1000 rpm pto shaft yields 540 rpm's on the motors. The lower engine speed lets us save fuel and optimize space between the gears. If need be, we can get the pto shaft yield to more than 800 rpm's at the motors."
Archer uses the 8 by 16-in. frame as a fluid reservoir. Oil is pumped under pressure on 1 1/4-in. lines and returns on 2 1/2-in. lines. The combination of the extended frame reservoir and the large capacity ensures that oil is naturally cooled. Two oil filters are located over the hitch axle.
Hydraulic rams on the baler hitches move them from trailing position to baling position. It adjusts to swaths from 9 to 19 ft. apart.
The hitch telescopes out to straddle a swath made by the lead rake or reconditioner and pulls back in to stay off swaths being baled. The fifth wheel nature of the axle allows the operator to "steer" the baler on side hills to prevent drift.
All baler hydraulics, other than the motor electro-hydraulic valves, are controlled from a specially wired control box that mounts in the cab of the tractor. Each baler pickup can be raised or lowered hydraulically and the baler adjusted up and down or from road to field position. Also, an electric outlet at each baler allows the addition of lights or other attachments.
Archer admits liking to tinker with the hitch. He is confident it is still better than anything he could have simply purchased, even though it wasn't cheap. "We probably have $24,000 in building costs," he says. "Perhaps it could be done for less if you had the iron and hydraulic components, but I probably spent as much on research and development as I did on building it."
Contact: FARM SHOW Followup, Dwayne Archer, P. O. Box 1298, Didsbury, Alberta, Canada T0M 0W0 (ph 403 335-4148).
To read the rest of this story, download this issue below or click
here to register with your account number.