You have reached your limit of 3 free stories. A story preview is shown instead.
To view more stories
(If your subscription is current,
click here to Login or Register.)
Collector Turns Cobs Into Cash
Ty and Jay Stukenholtz have been making cash from cobs with cob catchers for nearly 10 years. Now they're getting ready to cash in on their cob collector, too.
When they built their first cob collector, it was to supply a local plant with cobs in southeast Nebraska. The plant closed in 1998, but they continued to
..........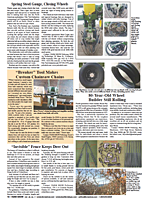
You must sign in, subscribe or renew to see the page.
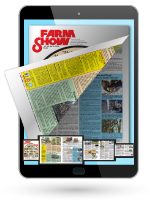
You must sign in, subscribe or renew to see the flip-book
Collector Turns Cobs Into Cash 31-5-9
Ty and Jay Stukenholtz have been making cash from cobs with cob catchers for nearly 10 years. Now they're getting ready to cash in on their cob collector, too.
When they built their first cob collector, it was to supply a local plant with cobs in southeast Nebraska. The plant closed in 1998, but they continued to work on the collector as they searched for markets for cobs. Now they can't get enough cobs to supply the demand for feed and even fuel.
"We collect cobs and husks and grind and sell them to cattle feeders," explains Jay Stukenholtz. "We have also supplied cobs to the University of Missouri for a study on displacing coal in generators. Others are looking at them for gasification, anaerobic digestion, and a long list of uses that will change the dynamics of the cob industry."
Then, of course, there is the big push for developing ethanol from cellulose. Cobs and husks could play a major role in that, points out Jay. He notes that while the value of corn stover to future crops is beginning to be recognized, cobs and husks have little nutrient value. In fact, cobs tie up nitrogen in corn on corn. Removing them may be the best practice, and the Stukenholtz brothers have the machine to do it. Jay estimates they can harvest 3/4 ton of cobs per acre with their collector when corn is yielding 200 bu./a.
Their current cob collector bolts to the rear and top of a Case IH combine without modification to the combine itself. A combination of sieves and air pressure separates stalk and leaf parts from cobs as they exit the combine. Sieves can be adjusted to collect only cobs. Selected material is blown up and over the combine to a 320 cu. ft. storage basket that sits above the grain hopper on the combine. Basket extensions fold down when the combine is in transit.
The system is designed so the cob basket can be emptied at the same time as the grain tank. The cob basket can be installed for emptying to either or both sides. When the receiving cart is alongside, the basket slides to the edge of the combine, a door opens and an apron chain moves the cobs out and drops them into the cart.
"This year we will be using a 1,250 bu. Balzer grain cart with a divider so we can haul both cobs and grain from the field with the same cart," explains Jay. "We sized the cob basket so it would fill at about the same rate as the grain tank. However, the operator can stop or start collecting cobs on the fly, so if the cob tank is full, but the grain tank isn't, he can keep going."
Now on their 12th generation machine, the Stukenholtzs feel they have the design just about ready for production. Each machine has had to pay for itself through custom harvesting and cob collection on their farm. The brothers charge $35 per acre to harvest cobs and corn. If allowed to keep the cobs, they may charge as little as $10 or even less depending on cob value.
"With the collector, we can double what the combine normally does, and it only uses about 25 hp," says Jay. "This fall we'll be using it on soybean residue, and next summer will test it on wheat chaff."
The Stukenholtzs have patented and trademarked the system. They and business partner Beth Pihlblad have formed Ceres Agriculture Consultants to market the cob collector.
Contact: FARM SHOW Followup, Ceres Agriculture Consultants, LLC, 620 Woodcrest Dr., Waukee, Iowa 50263 (ph 515 480-4575; elphabais@mchsi.com).
To read the rest of this story, download this issue below or click
here to register with your account number.