You have reached your limit of 3 free stories. A story preview is shown instead.
To view more stories
(If your subscription is current,
click here to Login or Register.)
Three-Way "Reversed Loader Built For Bales"
There are lots of ways to move big round bales, but Robert Johnson likes his way best. He uses a rear-mount loader on a reversed WD Allis. It has a special bale fork that gives him an extra two feet of clearance and a pressure gauge on the lift cylinder that gives him bale weight within 25 lbs. Best of all, the whole t
..........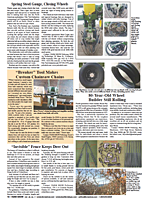
You must sign in, subscribe or renew to see the page.
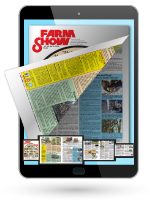
You must sign in, subscribe or renew to see the flip-book
Three-Way "Reversed Loader Built For Bales" TRACTORS Loaders 32-1-30 There are lots of ways to move big round bales, but Robert Johnson likes his way best. He uses a rear-mount loader on a reversed WD Allis. It has a special bale fork that gives him an extra two feet of clearance and a pressure gauge on the lift cylinder that gives him bale weight within 25 lbs. Best of all, the whole thing cost him only $5,700.
"You wouldn't believe the difference between a front-end and rear-mount loader," says Johnson. "The rear-mount takes so much less room and turns so much sharper. It's almost like a skid steer."
When Johnson bought the Allis from a neighbor in 2003 for $1,200, it had already been reversed. It had a good loader, but the engine was shot. The same neighbor had a 1957 potato harvester with a 223 Ford industrial power unit. Johnson bought it too. It came complete with radiator, hood, clutch, transmission and a front shaft to drive a hydraulic pump.
"I rebuilt the engine completely that winter," says Johnson. "Every moving part was new. A local machine shop did some work on the engine block. When it came back it, was painted Ford blue, so I stuck with those colors as I rebuilt the tractor. I now call it an Allis-Ford."
Johnson pulled everything out of the Allis, leaving only the drive wheels, final drive and transmission. He lengthened the frame 30 in. to make room for the rebuilt engine and connected the Ford transmission to the WD driveshaft with a chain coupler.
He attached a short steering axle from a 92 Massey Ferguson combine for an even tighter pivot. The front axle pedestal mount and orbit unit are from a 410 Massey Ferguson combine, and the fuel tank was from a 770 Oliver.
"The Ford transmission had a clutch that I use to put it in gear," says Johnson. "I added a second foot pedal for the WD oil clutch that I use for loader work."
While the loader worked great for most uses, loading bales on a trailer was a problem. The large drive wheels didn't allow him to get close enough to the trailer. While he knew he could buy a special bale fork for about $700, he decided to build one himself.
It consists of a double frame of 4 by 4-in. steel tubing about 4 ft. high and about 54 in. wide. The outside fixed frame attaches to the loader arms. The inside frame, to which the actual bale tines are attached, is about 46 in. wide with a 3 1/2-in. inside diameter pipe welded to the top of the sides of the frame.
To hinge the two frames, Johnson inserted a steel pipe with a 3-in. inside diameter inside the larger pipe and welded it to the tops of the uprights of the fixed frame.
"I put a couple of grease zerks on it and also had to shim the pipes so they would fit tight," explains Johnson. "I used some heavy sheet metal and tacked it inside."
A cross bar about 18 in. from the bottom of the inside frame reinforces it and serves as a mount for the arm of a hydraulic cylinder mounted to the cross bar of the loader. When the cylinder is extended, the bottom of the inside frame with the bale tines on it swings away from the fixed frame, extending the reach of the loader up to 2 ft. When the cylinder is drawn back, the inside frame nests within the fixed frame.
"The tines of the bale fork are also hinged," says Johnson. "Extending the third cylinder also lets me keep the tines parallel with the ground when I slip them under the bale instead of digging into the ground."
Johnson's final modification of the loader was to install a pressure gauge on the lift cylinder line near the controls. "I weighed a couple of bales and calibrated their weights with the readings on the gauge when I lifted them," he says. "Based on the pressure reading, I can estimate bale weight to within 25 lbs. of actual."
Contact: FARM SHOW Followup, Robert Johnson, 11248 398th St., Bagley, Minn. 56621 (ph 218 694-6798).
To read the rest of this story, download this issue below or click
here to register with your account number.