You have reached your limit of 3 free stories. A story preview is shown instead.
To view more stories
(If your subscription is current,
click here to Login or Register.)
Hybrid Retrofit "Boosts MPG 30 Percent"
Fuel-saving hybrid engine retrofits for start and stop drivers will soon hit the market. While fleets of shuttles, busses and delivery trucks will be the first to be hybridized, individual retrofitting is expected to follow. Since announcing the system, Larry Zepp, Variable Torque Motors, LLC (VTM), says the company ha
..........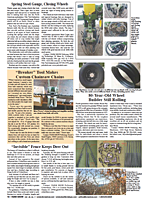
You must sign in, subscribe or renew to see the page.
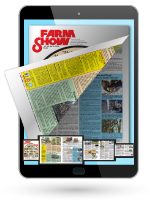
You must sign in, subscribe or renew to see the flip-book
Hybrid Retrofit "Boosts MPG 30 Percent ENGINES Engines 32-4-26 Fuel-saving hybrid engine retrofits for start and stop drivers will soon hit the market. While fleets of shuttles, busses and delivery trucks will be the first to be hybridized, individual retrofitting is expected to follow. Since announcing the system, Larry Zepp, Variable Torque Motors, LLC (VTM), says the company has been swamped with requests for information. The system is still in beta testing, but VTM is getting ready for the next step.
"We're in the process of establishing a network of outfitters who can retrofit fleets," says Zepp. "We're researchers and developers and will sell the system through dealers."
The company is far enough along that they can estimate prices to be in the $25,000 to $30,000 range. "At $30,000, if you install it in a shuttle that runs 30,000 miles a year and uses $4/gal. diesel fuel, it'll pay for itself in 23 months," says Zepp. "We estimate that start and stop applications like school busses will save 30 percent in fuel."
VTM's system consists of a permanent magnet electric motor powered by ultracapacitors. The motor is powered up or down by adjusting the magnetic field. Regenerative braking harvests energy and stores it in the ultracapacitors, which in turn feed it back on demand. The beauty of the system is that it can be quickly and easily installed in an existing drivetrain between the transmission and the differential. It can also be transferred from one vehicle to another.
The parallel system requires no modification of the existing engine, transmission or other vehicle systems. Standard brake and accelerator pedal activity is integrated electronically to activate the electric motor through a VTM controller.
During acceleration, the electric motor does the bulk of the work. As speed increases, the diesel engine takes over and the VTM motor supplies less and less torque. When it's time to brake, the electric motor becomes a generator, harvesting energy for the next acceleration. Not only is fuel saved, brake wear is reduced and tailpipe emissions are severely reduced. At the same time, response is immediate from the 60 hp motor.
Zepp says most people don't ask more than to be able to go from zero to 30 in 10 to 12 seconds. Fulfilling that expectation was how they sized their motor.
"When you tromp on the accelerator, you can get 400 lbs. of torque at the driveshaft because electric motors deliver full torque at zero speed, something diesel and gas engines can't do," says Zepp. "We figured we needed 60 hp peak available to launch and stop the vehicle. A wimpy motor doesn't have the power to accelerate or catch enough energy from braking to handle the next acceleration."
That type of acceleration and regeneration meant tremendous draw down on the energy storage source and equally fast recharge. Batteries simply couldn't handle the task. Zepp says the company turned to ultracapacitors from Maxwell Technologies.
Ultracapacitors are similar to batteries with their cells and use of electrolytes. Unlike batteries, energy is stored electrostatically rather than chemically. As a result, they can provide quick bursts and withstand hundreds of thousands of charge and discharge cycles. Maxwell makes modules of cells.
"We use two 48-volt modules and once charged up, they can give you 1,000 amps per second, though we don't need that much" says Zepp. "Most other comparable hybrids require 300 to 500 volts DC."
VTM's lower voltage requirement helped get their unit approved for school busses. Zepp says it makes the system much safer for mechanics to work with, as even skilled electricians treat high voltage with extreme care.
Contact: FARM SHOW Followup, Variable Torque Motors, LLC, 4501 Earhart Lane, Suite C, Fort Wayne, Ind. 46809 (ph 260 747-3633; fax 260 747-4140; toll free 888 747-6633; larryzepp@variabletorquemotors.com; www.variabletorquemotors.com).
To read the rest of this story, download this issue below or click
here to register with your account number.