2008 - Volume #32, Issue #5, Page #19
[ Sample Stories From This Issue | List of All Stories In This Issue | Print this story
| Read this issue]
Self-Propelled Splitter Carries Wood Home
![]() |
![]() |
![]() |
He built the unique splitting rig with help from his sons James, Timothy and Ryan. Glenn is a machinist and James is an engineering student at Youngstown State University.
The one-of-a-kind machine is built around the complete back end of a 1949 Allis Chalmers C tractor, including the rear end, axle, transmission, final drive, pinion gears, and differential as well as the seat. The rig rides on the tractor's original rear wheels with new 20-in. wheels on a home-built front axle. Power is provided by a Powertrain 13 hp engine on back. The engine belt-drives a pulley on the tractor's pto shaft. The pto shaft, in turn, belt-drives a hydraulic pump which operates all the rig's cylinders.
A hopper with flared sides on front is used to hold split wood, and there's a 7-ft. long splitter beam assembly on back built out of an 8 by 8-in. H-beam. Wood is split with the splitter in the vertical position. When the splitter isn't in use it drops hydraulically into a horizontal position for storage.
The cart is supported by a frame made from 2 by 3-in. rectangular tubing.
"This machine actually makes it fun to go out and split wood," says Neiheisel. "It lets us go into the woods and split wood with just one machine. There's no need for a separate tractor and wagon. It'll hold more than half a pickup load of wood.
"We came up with the idea because our family heats with wood, and we cut most of our firewood several miles from our home. In the past, we would haul our chain saws, homemade log splitter, tractor, and wagon along with us, but that got old real quick. So when the engine on our splitter gave out, we decided to build a new one from the ground up."
The men removed the pto unit from the rear of the tractor's pinion housing, machined a custom cover plate, and inputed the engine power through the pto shaft from the rear of the tractor instead of through the front of the transmission. "This worked fine except that now everything ran in reverse. We solved the problem by flipping the differential gear from the left side of the pinion to the right side, reversing everything," says Neiheisel.
The engine is belt-driven through a twin A-belt system with two custom machined pulleys. A belt clutch is used for shifting.
"The pump that we used is a Haldex 16 gpm two-stage splitter pump. From the pump, fluid enters the inlet port of a Prince 3-spool control valve," says Neiheisel.
A 3-spool valve mounts next to the operator and is used to control most operations. One valve operates a cylinder that steers the front wheels, one operates the splitter itself, and one is used to raise and lower the splitter beam assembly. A separate valve on back is used to operate the splitter.
"Using a spool valve to steer is a lot easier than operating a steering gear and eliminates the need for a steering shaft, which would get in the way of the wood cargo area. I just move the lever forward or backward to steer left or right," says Neiheisel.
"The splitting beam uses a customized hydraulic steering cylinder off a Caterpillar front-end loader and has a 2-in. dia. rod, 5-in. dia. piston, and 31-in. stroke. The wedge is a custom designed, double angle weldment, and the foot is made from 1-in. T-1 steel plate."
The machine didn't cost much to build. "We already had the Allis Chalmers tractor, which we had been keeping for parts. We bought the engine at an auction for $200," notes Neiheisel.
Contact: FARM SHOW Followup, Jamkes Neiheisel, 44864 Metz Road, Columbiana, Ohio 44408 (ph 330 831-8801; jmneiheisel@student.ysu.edu; www.arboristsite.com).
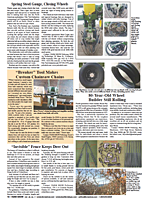
Click here to download page story appeared in.
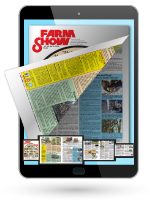
Click here to read entire issue