You have reached your limit of 3 free stories. A story preview is shown instead.
To view more stories
(If your subscription is current,
click here to Login or Register.)
Heat Recovery Unit Adds Value To Genset
You can get more out of a stationary diesel engine than just electricity. Add a heat recovery unit and you can produce either hot water or steam.
While Martin Machinery's main business is building gensets for primary power. Their heat recovery units have been used with their gensets to produce hot water for every
..........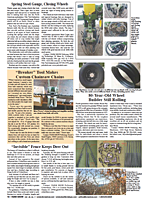
You must sign in, subscribe or renew to see the page.
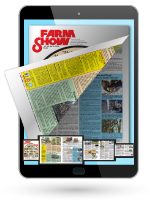
You must sign in, subscribe or renew to see the flip-book
Heat Recovery Unit Adds Value To Genset ENGINES Engines 33-2-4 You can get more out of a stationary diesel engine than just electricity. Add a heat recovery unit and you can produce either hot water or steam.
While Martin Machinery's main business is building gensets for primary power. Their heat recovery units have been used with their gensets to produce hot water for everything from therapeutic swimming pools in Russia to shrimp ponds in Venezuela to warming a floor in a welding shop.
Heat recovery units are largely custom made for the situation and the customer's needs, explains Marcus Martin. Heat can be recovered from any or all of the engine jacket, oil or exhaust systems. In all cases, he cautions that heat removal needs to be controlled and balanced against heat needed for the engine to operate efficiently.
"There's an acceptable operating temperature range determined by the engine manufacturer," explains Martin. "We design systems that operate within that range. For example, engine jacket water will not be cycled through our recovery heat exchanger until the water temperature reaches the recommended operating range."
The same parameters hold true for removal of exhaust or engine oil heat. Martin adds that exhaust temperature depends in part on the quality of the fuel, with higher quality fuel allowing more heat to be removed.
"Just like with a wood stove flue, you have to maintain a certain temperature to avoid condensation in the flue and buildup of particulates," he says.
Sensors determine when there is "excess" heat that can safely be removed, and the computerized control system adjusts valves accordingly. When the excess heat is no longer needed, such as for heating a floor in the summer, engine jacket water is cycled to a radiator or other cooling system.
Martin also cautions against heat recovery units that attempt to use the OEM water pump. "Engine water pumps are designed to circulate water through the engine components," he says. "We install a high flow pump that can push water through the jacket and then through a heat exchanger and back to the engine."
Martin uses standard boiler tube for the heat exchanger and recommends yearly or twice yearly cleaning with approved boiler cleaning equipment. The company also builds biogas generators for use on dairies. Recovered heat warms water that is then piped through the manure to boost methane production.
The company builds all sizes of gensets and matching heat recovery units starting at 45 kW. While the price varies by application, Martin says the basic heat recovery unit for the 45 kW genset would start at about $3,500. However, a complete package with computerized controls and fully assembled would run about $8,500.
Contact: FARM SHOW Followup, Martin Machinery, 39425 Excelsior Dr., Latham, Mo. 65050 (ph 660 458-7000; fax 660 458-7100; mmartin@martinmachinery.com).
To read the rest of this story, download this issue below or click
here to register with your account number.