Floaters Turned Into Giant Spreaders
When you can't charge more for what you do, you have to find ways to do it for less. That's what Bob Ward, Geneseo, Ill., has done. A custom manure hauler for 14 years, he has been unable to raise his rates for the past 10 due to hog producers getting bigger or getting out.
"I needed a big enough tank to unload a semi in one fill, but there isn't enough money in the business to go out and buy a new $400,000 manure application system," says Ward.
His solution was to retrofit a couple of his floaters that he had been using for herbicide application. He stripped away their 3,200-gal. tanks and added fifth wheel units from a junkyard, one of which he had to rebuild.
His first unit was a Big A 4500 floater with a repowered Cummins diesel engine. The second unit was a Terra-Gator 1804 that can go down the road at 40 mph.
"They are a lot faster in the field than tractors, smoother coming in empty and faster going down the road," explains Ward, adding that his customers appreciate the reduced compaction. "A floater leaves much less imprint on a field than a tractor does."
For his first manure tank, he attached a fifth-wheel bridge hitched to a 6,000-gal. Balzer tank that was equipped with an application toolbar. He says he made the mistake of following an engineer's recommendation instead of doing what farmers usually do, take the engineer's recommendation and double it.
"I learned my lesson on the first one," recalls Ward. "I used 4 by 8-in. 3/8-in. thick tubular steel on the first one, but it would get a sway in it under load. I had to keep reinforcing it. When I built the second one, I went with 1/2-in. thick, 4 by 12-in. tubular steel."
For his second tank, he took one of the 3,200-gal. tanks removed from the floater and had a welder cut the top off and lift it away. He then had a steel fabricator make flared sides for it to increase capacity to 4,200 gal. He built a chassis for it from 4 by 12-in. tubing and the single axle was salvaged from a Big A fertilizer spreader found at a junkyard.
Ward welded a heavy duty Balzer lift assembly and tool bar with Yetter coulters to the chassis. He then made new brackets for the disc closers, moving them two feet further back than normal. This made room for him to mount anhydrous ammonia delivery shanks to place the liquid manure in the ground before disc closers put the residue back.
"You can't tell we have been in the field after we leave," says Ward. "When Balzer saw what we were doing, they told me I was nuts. After we started using it, they ran a picture of my machine in their ads."
Ward likes the floater units as much for their hydraulic power and ease of servicing as for their speed. The floaters have separate hydraulic pumps and reservoirs for the application systems, as opposed to tractors where everything runs off the same pump.
One change he made on the Big A unit was to disconnect the front wheel drive. Originally each axle had its own hydraulic cylinder for turning with linkage to the middle of the machine that tied the axles together. As the rear system got worn, it allowed the rear axle to wander, not a good idea when speeding down a road. Ward pulled the rear cylinder and locked the rear axle with solid tie rods to hold it in place, leaving the front axle for steering the machine.
"They are so much easier to work on than tractors," he says. "If you have to pull a transmission, you don't have to pull it apart like on a tractor. They are built simpler and heavier to start with."
Contact: FARM SHOW Followup, Bob Ward, Ward Custom Application, 17623 Ford Rd., Geneseo, Ill. 61254 (ph 309 944-3957).
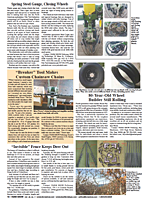
Click here to download page story appeared in.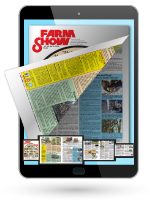
Click here to read entire issue
Floaters Turned Into Giant Spreaders FERTILIZER APPLICATION Fertilizer Application (58f) 28-2-19 When you can't charge more for what you do, you have to find ways to do it for less. That's what Bob Ward, Geneseo, Ill., has done. A custom manure hauler for 14 years, he has been unable to raise his rates for the past 10 due to hog producers getting bigger or getting out.
"I needed a big enough tank to unload a semi in one fill, but there isn't enough money in the business to go out and buy a new $400,000 manure application system," says Ward.
His solution was to retrofit a couple of his floaters that he had been using for herbicide application. He stripped away their 3,200-gal. tanks and added fifth wheel units from a junkyard, one of which he had to rebuild.
His first unit was a Big A 4500 floater with a repowered Cummins diesel engine. The second unit was a Terra-Gator 1804 that can go down the road at 40 mph.
"They are a lot faster in the field than tractors, smoother coming in empty and faster going down the road," explains Ward, adding that his customers appreciate the reduced compaction. "A floater leaves much less imprint on a field than a tractor does."
For his first manure tank, he attached a fifth-wheel bridge hitched to a 6,000-gal. Balzer tank that was equipped with an application toolbar. He says he made the mistake of following an engineer's recommendation instead of doing what farmers usually do, take the engineer's recommendation and double it.
"I learned my lesson on the first one," recalls Ward. "I used 4 by 8-in. 3/8-in. thick tubular steel on the first one, but it would get a sway in it under load. I had to keep reinforcing it. When I built the second one, I went with 1/2-in. thick, 4 by 12-in. tubular steel."
For his second tank, he took one of the 3,200-gal. tanks removed from the floater and had a welder cut the top off and lift it away. He then had a steel fabricator make flared sides for it to increase capacity to 4,200 gal. He built a chassis for it from 4 by 12-in. tubing and the single axle was salvaged from a Big A fertilizer spreader found at a junkyard.
Ward welded a heavy duty Balzer lift assembly and tool bar with Yetter coulters to the chassis. He then made new brackets for the disc closers, moving them two feet further back than normal. This made room for him to mount anhydrous ammonia delivery shanks to place the liquid manure in the ground before disc closers put the residue back.
"You can't tell we have been in the field after we leave," says Ward. "When Balzer saw what we were doing, they told me I was nuts. After we started using it, they ran a picture of my machine in their ads."
Ward likes the floater units as much for their hydraulic power and ease of servicing as for their speed. The floaters have separate hydraulic pumps and reservoirs for the application systems, as opposed to tractors where everything runs off the same pump.
One change he made on the Big A unit was to disconnect the front wheel drive. Originally each axle had its own hydraulic cylinder for turning with linkage to the middle of the machine that tied the axles together. As the rear system got worn, it allowed the rear axle to wander, not a good idea when speeding down a road. Ward pulled the rear cylinder and locked the rear axle with solid tie rods to hold it in place, leaving the front axle for steering the machine.
"They are so much easier to work on than tractors," he says. "If you have to pull a transmission, you don't have to pull it apart like on a tractor. They are built simpler and heavier to start with."
Contact: FARM SHOW Followup, Bob Ward, Ward Custom Application, 17623 Ford Rd., Geneseo, Ill. 61254 (ph 309 944-3957).
To read the rest of this story, download this issue below or click
here to register with your account number.