2004 - Volume #28, Issue #2, Page #27
[ Sample Stories From This Issue | List of All Stories In This Issue | Print this story
| Read this issue]
Portable Cattle Chute
![]() |
![]() |
![]() |
Michael Haynes pastures different groups of cattle in a variety of locations, so his chute needed to be portable.
"I mostly use it in the spring for castration, vaccination, branding, and worming of calves. They are scattered out at different places, many of which are leased or rented lands," he explains.
Haynes made the side panels from 2 3/8-in. oilfield pipe. The frames are 7 ft. tall by 8 ft 6 in. long. They are spaced 26 in. apart.
He then used some salvaged 1 1/4-in. pipe to make the swinging gate frames, filling in the voids with 1-in. pipe. Next, he used 1-in. round rod and pipe to make the gate hinges.
"I fashioned a sliding tailgate from 1-in. pipe and placed it in a track made from 1/4 by 1-in. flat bar. Small angle irons holding pulleys and ropes make the gate operate," Haynes says. "Gussets were used in the corners for support of the chute, as well as to hold it on its trailer."
He made the headgate from scratch out of angle iron, flat bar, round rod, pipe and channel iron. It's loosely patterned after a factory headgate, he says, but he made it heavier and changed a few things.
"I decided to make it operate from the other side, so that if I had to, the head gate could be bolted to my chute for opposite hand operation," he says.
The trailer he built to carry the chutes is patterned after propane tank-hauling trailers.
He started with some 4-in. channel iron and made a horseshoe-shaped frame 10 ft. long and 3 ft. wide at the front. He then boxed the channel iron in, using 10 ga. sheet steel. Haynes used some 2 3/8-in. and 1 1/2-in. pipe to make a tongue, and mounted a boat winch with strap about 12 in. above the frame, over the tongue.
"To make stub axles, I cut out and ground the spindles from an old Chevy Impala. Then I put them into my turning lathe and turned them until they fit perfectly into a 2 1/2-in. double strength pipe," he explains.
Haynes used some 2 3/8-in. pipes to make collars at the rear of the 4-in. channel to hold up the chute. A 2-in. pipe is inserted through the collars on both the trailer and the chute. A large washer is welded at one end, and a washer and pin secure the pipe onto the trailer at the other end. Two of those pipes are used.
Haynes says to load the chute in preparation for moving it, he backs the three-sided (horseshoe) trailer up to (around) it, and then hooks the winch strap to the top of the headgate. Next, he cranks the tongue of the trailer up in the air. This forces the rear of the trailer to the ground, where he can insert his pipe through the channel iron and his chute. He then disconnects the strap and hooks it on the bottom of the chute, where he had welded a hook. He's then able to winch the chute up in the air, which forces the tongue to come down until it's resting on the jack.
"When it's up high enough, I place another pipe pin under the chute and winch the chute down until it is resting on the pin, which is resting on the four inch channel iron," he says. "It can also be maneuvered by hand, since it's balanced, into the perfect location before unloading. The trailer can be moved by hand because of its light weight."
Contact: FARM SHOW Followup, Michael Haynes, 302 Charmont Drive, Charleston, Arkansas 72933 (ph 479 965-7504).
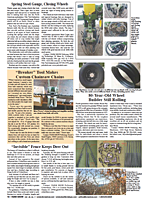
Click here to download page story appeared in.
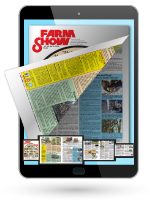
Click here to read entire issue
To read the rest of this story, download this issue below or click here to register with your account number.