You have reached your limit of 3 free stories. A story preview is shown instead.
To view more stories
(If your subscription is current,
click here to Login or Register.)
One-Piece Steel Doors Are Custom-Built
Doug Loder's overhead doors are generally installed on airport hangars, but the Marquette, Kansas, entrepreneur is finding strong demand for them in agricultural buildings. His Condor Hangar Systems use 110-volts to run a 1/2 hp motor to open and close the one-piece door anchored to a counterweight by stainless steel c
..........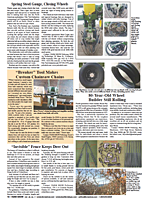
You must sign in, subscribe or renew to see the page.
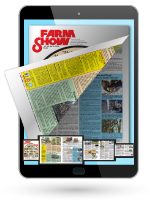
You must sign in, subscribe or renew to see the flip-book
One-Piece Steel Doors Are Custom-Built BUILDINGS New Techniques 33-4-20 Doug Loder's overhead doors are generally installed on airport hangars, but the Marquette, Kansas, entrepreneur is finding strong demand for them in agricultural buildings. His Condor Hangar Systems use 110-volts to run a 1/2 hp motor to open and close the one-piece door anchored to a counterweight by stainless steel cables, each capable of lifting more than twice the door's weight.
"That's the main reason I believe mine is better," Loder says. "If the drive system stops, it just stops. The counterweight holds the door in place. From a safety standpoint it's safer than a bi-fold door that is held up by a winch, which can fail." If the power is out, Loder's door can be opened with a chain.
Loder had experience building hangars and installing doors for a company and saw firsthand what worked and what didn't. He started manufacturing his system in his farm shop
in 1986.
Loder and his son build the frames out of steel tubing, and the weight tower is made of I-beam and channel iron. Doors are custom-finished with insulation (to suit the region) and covered with materials that match the building.
"This system has very few wear points," Loder says. "It has drive chain and sprockets, cables and pulleys. The door is designed for all weather operation. There are no exposed tracks to freeze the door shut."
The single door design only requires 6 to 14-in. of headspace compared to 36 to 48-in. on a bi-fold door. With about half of the door inside in the open position it's also less susceptible to strong winds.
Loder custom-builds the door in sizes from 20 to 75-ft. wide. Hangars typically require a 60 by 18-ft. door. Agriculture shops usually only require a 15-ft. clearance. One of Loder's doors served two purposes - to house a combine and an airplane.
Most of Loder's customers are in the Kansas/Missouri area, because he prefers to install the doors himself. He'll work with customers in other U.S. locations, however, and has come up with kit directions for do-it-yourselfers.
Loder says his prices are competitive, and he offers a 5-year warranty. A farming neighbor is building two shops, for example; the 36-ft. and 24-ft. doors installed will cost $11,000, altogether.
Contact: FARM SHOW Followup, Condor Hangar Systems, Doug Loder, 2466 28th. Rd., Marquette, Kansas 67464 (ph 785 614-1700; condor@lrmutual.com; www.condor hangars.com).
To read the rest of this story, download this issue below or click
here to register with your account number.