You have reached your limit of 3 free stories. A story preview is shown instead.
To view more stories
(If your subscription is current,
click here to Login or Register.)
Irrigation Pipes Make Sturdy Buildings
Kenny Cemper started installing irrigation systems in 1969. A few years later, he made his first calving shed out of discarded pipes that he had replaced.
"Ranchers just loved the sheds," says Cemper, who has built nearly 20 of them. Then a gas station owner asked him to build a 40 by 60-ft. shed for
..........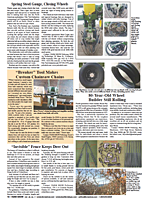
You must sign in, subscribe or renew to see the page.
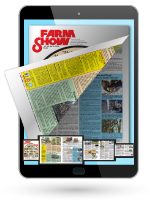
You must sign in, subscribe or renew to see the flip-book
Irrigation Pipes Make Sturdy Buildings IRRIGATION Irrigation Systems Kenny Cemper started installing irrigation systems in 1969 A few years later he made his first calving shed out of discarded pipes that he had replaced
Ranchers just loved the sheds says Cemper who has built nearly 20 of them Then a gas station owner asked him to build a 40 by 60-ft shed for storing bulk oil barrels
Since that time Cemper has built many buildings out of irrigation pipe
The main thing is that you make it perfectly square Cemper emphasizes If you don t you ll have problems with the steel siding It s got to be perfect
He starts by making straight cuts on the pipes tearing out hoses and welding holes shut He squares up a base of large pipes and welds them together Then he tack welds upright pipes every 9 to 10 ft and welds another rung of pipes around the top He measures often to make sure everything remains level and square before he makes final welds ů sometimes using a come-along to pull pipes into line
He joins the vertical and horizontal pipes together with brackets made from angle iron He welds longer pieces of the angle iron horizontally to the upright pipes for strength and to support the steel siding and roofing
Cemper explains that the old irrigation pipe he uses comes in two gauges of steel He uses the heavier gauge with 1/8-in walls for the horizontal pieces and the lighter weight pieces for the uprights
The sheds are welded to steel bars laid into concrete footings or simply lag-bolted into the concrete Cemper usually builds the frame in his Quonset building during the winter and moves the frame with angle supports on a trailer to the final site He cuts out the pipe for door openings after it has been moved
I figure out dimensions so that they come out perfect with the steel siding and the overlap Cemper says A couple of his recent buildings were 30-ft by 27-ft for example He added a loft in one made of recycled hog confinement grates supported by 5/16-angle iron every 2 ft
His largest building was 40 by 60-ft with 14-ft walls With the help of an assistant he framed and put on the steel for the roof section on the ground and lifted the roof on to the irrigation pipe frame with six loader tractors
With the welded angle iron supports Cemper says he believes his sheds will outlast any commercial sheds on the market Using recycled material for the frame also saves money
Contact: FARM SHOW Followup Kenny Cemper 87175 504th Ave Page Neb 68766 ph 402 394-1603
To read the rest of this story, download this issue below or click
here to register with your account number.