You have reached your limit of 3 free stories. A story preview is shown instead.
To view more stories
(If your subscription is current,
click here to Login or Register.)
Hoop Building House Dairy Farm's Manure
Laurelbrook Farm put up four new Farmtek hoop buildings this year to house composted manure from their 800-cow dairy herd.
Living in a highly populated area near East Canaan, Conn., the farm faces limitations on where manure can be spread.
So owner Bob Jacquier and family started composting manure and sel
..........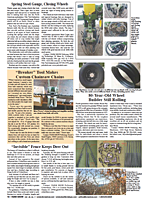
You must sign in, subscribe or renew to see the page.
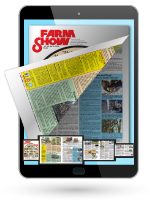
You must sign in, subscribe or renew to see the flip-book
Hoop Building House Dairy Farm's Manure MANURE HANDLING Miscellaneous 33-6-20 Laurelbrook Farm put up four new Farmtek hoop buildings this year to house composted manure from their 800-cow dairy herd.
Living in a highly populated area near East Canaan, Conn., the farm faces limitations on where manure can be spread.
So owner Bob Jacquier and family started composting manure and selling it locally.
"We composted outside for two years to see if the market was really there, before we committed the resources to put buildings up," says Bob Jacquier, who farms with his brother and father.
They sold compost to a couple of local nurseries, and without any advertising word spread. They soon had more demand than they could supply.
They moved the operation inside in early 2009 for a couple of reasons.
"We were concerned about runoff and wanted to do it in an environmentally friendly way," Jacquier explains. "For quality compost, being able to control the moisture in a pile makes a huge difference. If it gets too wet or dry it stops composting. Inside we can add moisture exactly when we need it."
Working with grants and support from four state and federal agencies, including the Connecticut Department of Environmental Protection, they set up four Farmtek ClearSpan Fabric structures (ph 800 327-6835; www.farmtek.com) on 4-in. asphalt pads. The galvanized steel truss buildings should last 25 years.
Manure is scraped every day from free-stall barns and collected in a small storage pit, where liquid and solids are separated with a mechanical separator. Liquid goes on the fields, and solids are hauled to the buildings.
One week's worth of manure is enough for one windrow in the two 100 by 250-ft. composting buildings. Each building holds five windrows. Old hay, horse barn sawdust, woodchips and other material is mixed into the manure pile.
The manure composts in the row for about four weeks and is regularly turned with a Backhus windrow turner that straddles the windrow. The material breaks down when it's between 130 and 160 degrees, so temperature is carefully monitored.
"We used to bucket-turn the manure with a loader when we were outside. The windrow turner is a big time saver," Jacquier says.
After four weeks, two rows are joined together. After eight weeks, the compost is hauled to an 80 by 200-ft. finishing shed for at least four weeks. Over the 3-month period the volume decreases by about half.
From there the material is screened and shipped out in bulk, or kept in storage during the off-season, from November to April. The Jacquiers plan to bag some of the compost next year.
"A big advantage is that it's stored indoors, so we always have dry product to sell," Jacquier says.
The Jacquiers have already developed different mixes - a garden mix, made of compost, subsoil and sand; and compost mulch, for example. By using different screens, they plan to add new products in the future.
The biggest challenge of composting may be the timing. Crops need to be planted the same time customers need compost for their gardens.
"We have two people working almost full time on composting at this point," Jacquier says. "We may need more in the future."
Besides labor, the farm's investment included the buildings ($7.50 to $9/ft.), asphalt, the windrow turner and screener.
Overall, adding composting to a dairy operation is a good fit. There is little to no odor, which is good for neighbor relations. The Jacquiers already had much of the equipment needed, including trucks and live-bottom trailers. And it's a way to diversify and bring in extra income.
Contact: FARM SHOW Followup, Bob Jacquier, Laurelbrook Farm, 390 Norfolk Rd., East Canaan, Conn. 06024 (ph 860 824-1287; laurelbrookfarm@sbcglobal.net).
To read the rest of this story, download this issue below or click
here to register with your account number.