2010 - Volume #34, Issue #2, Page #08
[ Sample Stories From This Issue | List of All Stories In This Issue | Print this story
| Read this issue]
Mechanical Asparagus Harvester
![]() |
"A set of wafer thin photo sensors 6 ft. ahead of the cutting mechanism can be adjusted from 4 to 12 in. above the field surface to pick only those spears a certain height or taller," explains Haws. "When a light beam shooting from one sensor to another is broken at that height, it trips the mechanism to activate the cutter head."
Cutter heads that look like the spokes of a wheel rotate down to grasp the spear between two pads the size of a hand. As the pads close on the spear, a blade cuts it below the surface of the field. The pads lift the spear up and release it over a conveyer belt that carries it to the working platform above. The cutter head rotates as the next set of pads grasp a new spear, all operating within the 3.1-in. swath.
It's a complex process that requires exacting tolerances. The 36 cutter heads have a total of about 20,000 parts; Haws designed and fabricated around 100 of them in his shop. The number and uniqueness of many of the parts are part of the reason Haws expects the first few harvesters to be priced between $250,000 and $300,000.
"The price isn't so much the materials as it is the labor and equipment needed to make the parts," says Haws. "Over time we not only designed the parts, we had to learn how to make them. We now have the programming, tooling and fixtures needed to reproduce them."
Haws believes he's on the final prototype (no. 15 or 16) in a 40-year quest to automate the asparagus harvest. What he has built is unlike anything else in agriculture. The chassis is designed to carry the working components, including the row of sensors behind the front wheels, the row of cutter heads, conveyer beds and working platform. Various nuts and bolts, ball joints, tires, the engine and a handful of other components are among the few off-the-shelf components. Even the wheels have custom-designed hubs welded in them to match the transverse drive shaft that was machined by Haws.
"We use a 35 hp diesel engine from a New Holland industrial lawn mower," says Haws. "It has the pto and hydrostatic drive coming off the front. It powers the mechanical drive shaft that powers the drive wheels and the cutting bed. That way if the machine picks up ground speed, the cutter heads move faster, too."
The harvester measures about 16 ft. front to back and 12 ft. from the center of one rear tire to the other. The engine sits beneath the driver at the back of the work platform that rides only about 3 ft. above the field's surface. The workers stand ahead of the operator, selecting out asparagus spears as the conveyer drops them on the work table. The empty belt loops up and over the work platform through a steel bridge and back to the cutting heads. In the newest version of the machine, the bridge will also support a sunshade over the workers.
Selected spears are placed on a second conveyer that carries them through a trimmer to be loaded into boxes. With manual harvest, the boxes are left in the field for hours until the workers are finished. With the mechanical harvester, filled boxes will be left at field ends for regular pickup and cooling. The result will be fresher, higher quality asparagus, adds Haws.
Because they are directly in line with their triggering photo sensors, any deviation in driving will cause the cutters to miss the selected spear. Haws has redesigned the front steering system in the newest prototype for tighter, more exact steering. This will allow him to use GPS assisted steering with sub inch accuracy.
"That will free up the driver from steering and also make the harvester run straighter, missing fewer spears," he says.
"Our goal is a machine that can go 24/7 the entire length of the harvest without any maintenance outside of sharpening knives," he says. "We think we have that now. This will be our last year of field testing."
Contact: FARM SHOW Followup, Haws Company, 6671 Langford Rd., Mesa, Wash. 99343 (ph 509 265-4327; jhaws1001@gmail.com).
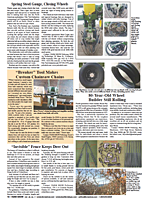
Click here to download page story appeared in.
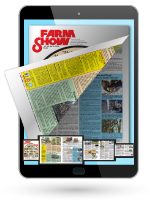
Click here to read entire issue
To read the rest of this story, download this issue below or click here to register with your account number.