You have reached your limit of 3 free stories. A story preview is shown instead.
To view more stories
(If your subscription is current,
click here to Login or Register.)
Self-Propelled Grain Cart Looks Factory-Built
If Deere ever comes out with a self-propelled grain cart, it'll probably look a lot like Harlan Schlaak's. Schlaak combined an 8820 Deere combine with a 674 Brent grain cart. The result is a self-propelled grain hauler that won't stop for anything and is easy to operate.
"I picked the 8820 for its heavy final dr
..........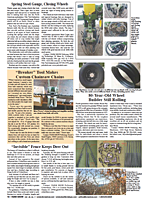
You must sign in, subscribe or renew to see the page.
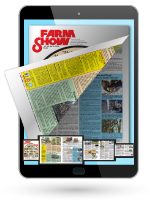
You must sign in, subscribe or renew to see the flip-book
Self-Propelled Grain Cart Looks Factory-Built WAGONS/TRAILERS New Wagons 90-10-87 If Deere ever comes out with a self-propelled grain cart, it'll probably look a lot like Harlan Schlaak's. Schlaak combined an 8820 Deere combine with a 674 Brent grain cart. The result is a self-propelled grain hauler that won't stop for anything and is easy to operate.
"I picked the 8820 for its heavy final drives," says Schlaak. "If I had a hitch on back, I could pull a semi with it. With the rear wheel assist, all four wheels are pulling. It carries the weight of 674 bushels instead of pulling it."
Schlaak started by tearing the combine apart. He made the job easier by welding steel tubing under the engine and cab. This allowed him to use a forklift to pick up the two as a single unit and set them aside for storage. Later the temporary frame would make it easy to reposition the two.
"I used 4 by 7-in., 1/4-in. wall tubing to build a new 14 1/2-ft. undercarriage," says Schlaak. "That was long enough to hold the grain box with the cab and engine on front."
He attached the axles, setting the steering axle as far to the rear as possible so the heavier front drive wheels would carry more weight. The drive wheels were positioned as close to the front of the auger box as possible for the same reason.
"I set the auger box on top of the new frame, bolting it in place with a little welding," says Schlaak. "I did it so it can be returned to its original axles if we ever want. I even left the hitch on the front."
To reattach the engine and cab, Schlaak used the original mounts. With everything matching the original frame, he was able to simply set them back in place with the forklift, bolt them in and cut away the temporary frame.
"It worked slick," says Schlaak. "With the frame holding them, I could use the forklift to shift them around and tilt them as needed."
With the aid of a two-way hydraulic valve he found at a parts store, Schlaak was able to use the controls that had lifted the head and reel (one-way valves originally) to fold the auger and open and close the grain door.
"I used the gearbox and handle that had started and stopped the separator to activate the auger," says Schlaak. "The new setup included the old pulley, belt, and shaft to connect the gearbox to the pto. It wasn't perfect engineering, but it works nice."
Positioning of the cab worked out great as well. Because the auger extends out ahead of the cab, the operator doesn't have to turn around to watch when unloading. The hydrostatic drive makes it easy to match speed with a combine when it's unloading on the go.
"You don't have to sit there, riding the clutch and looking out your back window," says Schlaak. "We even mounted a side spot mirror on the right side so it looks right into the grain box."
Contact: FARM SHOW Followup, Harlan Schlaak, P.O. Box 383, 22069 130th St., New Richland, Minn. 56072 (ph 507 465-3677).
To read the rest of this story, download this issue below or click
here to register with your account number.