You have reached your limit of 3 free stories. A story preview is shown instead.
To view more stories
(If your subscription is current,
click here to Login or Register.)
Silage Chopper Wood Chipper
"It handles branches up to 4 in. in dia. and works fast," says Steve Litchy who, along with his father Randy, designed and built a portable wood chipper. It's made out of an old Gehl silage chopper they bought for $200 from a local farmer. A Kohler 14 hp engine belt-drives the chopper's rotor.
Steve's grandpa,
..........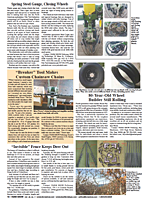
You must sign in, subscribe or renew to see the page.
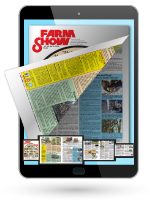
You must sign in, subscribe or renew to see the flip-book
Silage Chopper Wood Chipper FORAGE HARVESTERS Forage Harvesters (31F) 34-3-16
"It handles branches up to 4 in. in dia. and works fast," says Steve Litchy who, along with his father Randy, designed and built a portable wood chipper. It's made out of an old Gehl silage chopper they bought for $200 from a local farmer. A Kohler 14 hp engine belt-drives the chopper's rotor.
Steve's grandpa, Lloyd Litchy, previously had built a wood chipper out of a silage chopper that was featured in FARM SHOW (Vol. 33, No. 6). It was a stationary model, belt-driven off a Simplicity 18 hp garden tractor. Steve and Randy's model is mounted on a pair of trailer wheels, allowing them to pull it around with a garden tractor.
"Grandpa had a great idea. Hopefully we've improved on it," says Steve. "This model has more power and a much bigger cutting apparatus so it can handle bigger brush and branches. And there's no need to hook up any belts to a garden tractor."
The two men stripped away everything on the Gehl chopper except the chopper unit itself and replaced the sprockets with pulleys.
"The chopper was originally equipped with 9 knives, but we didn't like the chipping performance with that many knives so we took off 6 of them," says Steve.
The unit mounts on a pair of 15-in. trailer wheels. The engine mounts in back of the chipper where it helps balance out the weight and doesn't interfere with the placement of the hopper.
"The engine has a 3-in. dia. pulley on it and the rotor shaft has an 8 1/2-in. dia. pulley," explains Steve. "This combination spins the rotor shaft at about 630 rpm's with the engine running at 1,800 rpm's."
They used 5/8-in. thick treated plywood and heavy-duty angle iron to make the hopper. "We tilted the hopper at a slight angle relative to the blades so brush will fall in by gravity. The hopper is positioned high enough to prevent injury," says Steve.
To control the size of the chips, they fabricated a screen out of rebar. The screen reduces chip size to about 1 in. An idler is used to engage the chipper shaft and is held up by a sliding pin; once the engine is running, the pin is released and the idler is dropped down onto the belt by spring tension.
Ground up material exits at the bottom of the machine.
"It took about 5 months to build the chipper. A lot of that time was spent on planning and gathering all the materials," says Steve. "We paid $150 for the engine and about $50 for the axle and pulleys."
Contact: FARM SHOW Followup, Steve Litchy, 23250 30th St. S.E., Blomkest, Minn. 56216 (ph 320 995-6583; stevenllitchy@hotmail.com).
To read the rest of this story, download this issue below or click
here to register with your account number.