You have reached your limit of 3 free stories. A story preview is shown instead.
To view more stories
To view more stories
SUBSCRIBE OR RENEW NOW
(If your subscription is current, click here to Login or Register.)2010 - Volume #34, Issue #3, Page #28
[ Sample Stories From This Issue | List of All Stories In This Issue]
Guillotine Wood Splitter
No chainsaw is needed with Darrell Inkster's firewood "guillotine". The double-edged blade slices through whole trees, cutting them into 16-in. lengths and splitting them at the same time."I go through 20 cords of firewood a winter and decided to find a way to make the job easier," says Inkster. "My wife ..........
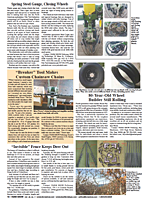
You must sign in, subscribe or renew to see the page.
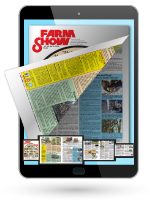
You must sign in, subscribe or renew to see the flip-book
Guillotine Wood Splitter WOODLOT EQUIPMENT Miscellaneous No chainsaw is needed with Darrell Inkster s firewood guillotine The double-edged blade slices through whole trees cutting them into 16-in lengths and splitting them at the same time
I go through 20 cords of firewood a winter and decided to find a way to make the job easier says Inkster My wife uses a Bobcat to load logs onto the feeder chain and I run the shears
Everything about the guillotine shears is massive starting with the log feeding channel It s a 28-ft long 14-in wide 1-in thick I-beam removed from a nearby bridge when it was rebuilt To move logs in the 14-in wide I-beam channel Inkster used combine feeder chain cutting down the cross bars to fit
The cutting blade is 22 in wide by 16 in high and 1-in thick Recycled from the steel cutting edge of a Caterpillar dozer blade Inkster says he got it for almost nothing though he spent around 8 hours grinding the edge razor sharp with a disk grinder
The splitter blade is a second piece of steel 6 in long and also 1- in thick One end of the wedge is welded to a 1/4-in steel plate that is bolted to the shears blade The wedge has been ground to a sharp edge The splitting wedge is mounted at the blade s center point but about 4 in up from the blade edge While only 6 in long Inkster says it s more than enough to split a 16-in length of log after the shears have done their job
Green wood splits clean as a whistle says Inkster When the blade and wedge hit older dry wood they tend to squash the wood fiber pulverize and then split it
To mount the blade Inkster fabricated a reinforced arch above the output end of the feeder channel He used sections of 1/4-in thick 3 by 4-in rectangular steel tubing with curved ends He welded them together at the peak to form a mount for the heavy-duty hydraulic cylinder that drives the blade
The curved arch distributes the pressure from the cylinder better than square beams would have says Inkster I run the cylinder off a hydraulic pump on my truck I set the pressure at 2 100 psi which gives the blade about 40 tons of down pressure
The curved pieces were structurally sound but had slight imperfections They had been fabricated by a local bus manufacturer but rejected for the intended bus frames
I was able to buy a truckload for scrap metal prices says Inkster They were already bent just right for use as the arch and for support legs to raise the feeder chain I-beam off the ground I just cut them to fit the width of the feeder track
The arch creates a 22-in high 14-in wide throat for trunks and branches to slide through Inkster reinforced the arch with added lengths of steel tubing welded to either side As the blade moves up and down it s held in place by 1 by 2-in steel bar stock that s welded to the sides of the arch Inkster bolted pairs of 1-in long 2-in dia roller bearings to the output sides of the blade They run against the steel retention bars and keep the blade from kicking sideways
I plan to add bearings on the input side of the blade as well says Inkster I may grind a longer bevel into the blade also Right now it is only tapered at the last 1 1/2 in which creates quite an angle I d like it sloped more to work more like a cheese slicer than a cleaver
Inkster mounted two hydraulic valves on the operator side of the shears One works the blade while the other controls the feeder chain While he runs the shears his wife loads logs onto the feeder chain and clears away split wood
We can process about two cords per hour says Inkster I can cut and split a chunk every 25 seconds
He estimates that total cash expenditures for new hydraulic hose bearings and a few other new parts ran less than $1 000 However he thinks he may have spent around 100 hours building it an investment that he says has paid off When not using it to slice and split whole trees he can do individual sections of tree trunks
It goes through 12-in poplar like nothing he says The way it s designed I can chainsaw logs up to 20-in diameter feed them through on end and use it like a normal splitter
Contact: FARM SHOW Followup Darrel Inkster Box 854 Dauphin Man Canada R7N 3J5 ph 204 638-7297; darink@inetlink ca
I go through 20 cords of firewood a winter and decided to find a way to make the job easier says Inkster My wife uses a Bobcat to load logs onto the feeder chain and I run the shears
Everything about the guillotine shears is massive starting with the log feeding channel It s a 28-ft long 14-in wide 1-in thick I-beam removed from a nearby bridge when it was rebuilt To move logs in the 14-in wide I-beam channel Inkster used combine feeder chain cutting down the cross bars to fit
The cutting blade is 22 in wide by 16 in high and 1-in thick Recycled from the steel cutting edge of a Caterpillar dozer blade Inkster says he got it for almost nothing though he spent around 8 hours grinding the edge razor sharp with a disk grinder
The splitter blade is a second piece of steel 6 in long and also 1- in thick One end of the wedge is welded to a 1/4-in steel plate that is bolted to the shears blade The wedge has been ground to a sharp edge The splitting wedge is mounted at the blade s center point but about 4 in up from the blade edge While only 6 in long Inkster says it s more than enough to split a 16-in length of log after the shears have done their job
Green wood splits clean as a whistle says Inkster When the blade and wedge hit older dry wood they tend to squash the wood fiber pulverize and then split it
To mount the blade Inkster fabricated a reinforced arch above the output end of the feeder channel He used sections of 1/4-in thick 3 by 4-in rectangular steel tubing with curved ends He welded them together at the peak to form a mount for the heavy-duty hydraulic cylinder that drives the blade
The curved arch distributes the pressure from the cylinder better than square beams would have says Inkster I run the cylinder off a hydraulic pump on my truck I set the pressure at 2 100 psi which gives the blade about 40 tons of down pressure
The curved pieces were structurally sound but had slight imperfections They had been fabricated by a local bus manufacturer but rejected for the intended bus frames
I was able to buy a truckload for scrap metal prices says Inkster They were already bent just right for use as the arch and for support legs to raise the feeder chain I-beam off the ground I just cut them to fit the width of the feeder track
The arch creates a 22-in high 14-in wide throat for trunks and branches to slide through Inkster reinforced the arch with added lengths of steel tubing welded to either side As the blade moves up and down it s held in place by 1 by 2-in steel bar stock that s welded to the sides of the arch Inkster bolted pairs of 1-in long 2-in dia roller bearings to the output sides of the blade They run against the steel retention bars and keep the blade from kicking sideways
I plan to add bearings on the input side of the blade as well says Inkster I may grind a longer bevel into the blade also Right now it is only tapered at the last 1 1/2 in which creates quite an angle I d like it sloped more to work more like a cheese slicer than a cleaver
Inkster mounted two hydraulic valves on the operator side of the shears One works the blade while the other controls the feeder chain While he runs the shears his wife loads logs onto the feeder chain and clears away split wood
We can process about two cords per hour says Inkster I can cut and split a chunk every 25 seconds
He estimates that total cash expenditures for new hydraulic hose bearings and a few other new parts ran less than $1 000 However he thinks he may have spent around 100 hours building it an investment that he says has paid off When not using it to slice and split whole trees he can do individual sections of tree trunks
It goes through 12-in poplar like nothing he says The way it s designed I can chainsaw logs up to 20-in diameter feed them through on end and use it like a normal splitter
Contact: FARM SHOW Followup Darrel Inkster Box 854 Dauphin Man Canada R7N 3J5 ph 204 638-7297; darink@inetlink ca
To read the rest of this story, download this issue below or click here to register with your account number.