You have reached your limit of 3 free stories. A story preview is shown instead.
To view more stories
(If your subscription is current,
click here to Login or Register.)
Mega Composter Saves Dairies Big Money
Big dairies are saving money by turning manure into bedding, and as a result, reducing manure handling and storage. BeddingMaster composting machines from DariTech, Inc. do the job up to 50 percent faster than similar competitive systems.
"We've delivered 6 of them to Oregon dairies so far and more elsewhere," sa
..........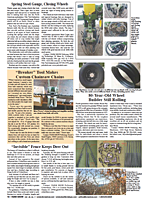
You must sign in, subscribe or renew to see the page.
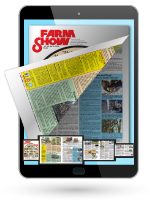
You must sign in, subscribe or renew to see the flip-book
Mega Composter Saves Dairies Big Money DAIRY EQUIPMENT & IDEAS Dairy Equipment & Ideas 34-5-20 Big dairies are saving money by turning manure into bedding, and as a result, reducing manure handling and storage. BeddingMaster composting machines from DariTech, Inc. do the job up to 50 percent faster than similar competitive systems.
"We've delivered 6 of them to Oregon dairies so far and more elsewhere," says Andy Ward, Ore. manager, DariTech, Inc.
The 6-ft. diameter composters come in 16, 32 and 40-ft. lengths. A heavy-duty electric motor keeps the drum rotating 24/7.
The manure first goes through separators to remove most of the liquid. The solids are passed into the composter drum that turns constantly, tumbling the manure, keeping it aerated, and feeding decomposing bacteria.
"We like to feed the drum for 20 to 30 min. out of every hour," explains Ward. "When you start with an empty drum, it takes 24 to 30 hours to fill it and then run it until product comes out the discharge end."
Ward explains that ideally the solids should turn in the drum for about two days. He has one dairy where they run material through in 28 to 30 hours, which is actually enough time to produce pathogen-free bedding with no odor.
"The exhaust fan draws cool air through the discharge opening, maintaining oxygen flow, bacterial levels and pasteurization," says Ward.
The ideal ambient temperature for optimum composting is 55 to 60 degrees. However, the composter can handle lower temperatures.
"We had one that was installed last summer, and winter temperatures got down in the 20's and 30's," says Ward. "They never had a problem all winter. The internal temperature cooled down some, but the machine still maintained the target level of 140 to 150 degrees."
The units are very low maintenance, requiring about an hour a day once set up for automatic filling and discharge. Temperature levels need to be checked, as do the separator amperage levels. Ward explains that amp levels indicate the dryness of material feeding into the drum.
One part of the daily routine includes greasing the wheels on which the drum turns. The mid-size steel drum weighs 28,000 lbs. empty.
"We went with a steel drum on steel idler wheels to handle the weight," he says. "To keep the steel from flaking, a little grease needs to be added each day."
Ward says the machines are very simple in their design. Linear boards on the inside of the drum provide temperature-maintaining insulation. Spaces between the boards host bacteria. The boards also protect the interior of the drum from the abrasive affects of the revolving solids.
Suggested herd size for the three models is 600 head for the 16-ft. unit, up to 1200 head for the 32-ft. unit, and up to 3,000 head or more for the 40-ft. unit. Prices vary depending on how manure is currently handled.
Contact: FARM SHOW Followup, DariTech, Inc., 8540 Benson Rd., Lynden, Wash. 98264 (ph 360 354-6900; toll free 800 701-3632; info@daritech.com; www.daritech.com).
To read the rest of this story, download this issue below or click
here to register with your account number.