You have reached your limit of 3 free stories. A story preview is shown instead.
To view more stories
To view more stories
SUBSCRIBE OR RENEW NOW
(If your subscription is current, click here to Login or Register.)2010 - Volume #34, Issue #4, Page #16
[ Sample Stories From This Issue | List of All Stories In This Issue]
Amazing System Feeds 400-Lb. Logs To Furnace
Jim Struble can load 400-lb. logs into his wood-fired boiler with his fingertips thanks to his log loader that lets him or his wife stoke the boiler with up to 4-ft. chunks."The problem with big outdoor boilers is that it's really hard to slide big chunks of wood in on top of each other," says Struble. "W..........
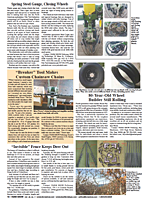
You must sign in, subscribe or renew to see the page.
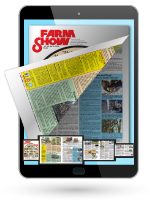
You must sign in, subscribe or renew to see the flip-book
Amazing System Feeds 400-Lb Logs To Furnace ENERGY Wood Burners 65 Jim Struble can load 400-lb logs into his wood-fired boiler with his fingertips thanks to his log loader that lets him or his wife stoke the boiler with up to 4-ft chunks
The problem with big outdoor boilers is that it s really hard to slide big chunks of wood in on top of each other says Struble With my log loader I can do it without even getting smoke in my face
At 63 Struble wanted a way to fire his furnace easily for years to come He and his wife run a bed and breakfast in their 2 000-sq ft northern Michigan home They heat it and a 4 500-sq ft addition with wood The boiler also provides hot water year round
I burn 20 to 25 pulp cords or more than 80 000 lbs of wood a year says Struble We couldn t afford to live here without wood
His tower style log loader consists of a pivoting center post or mast with a 10-ft boom and a travelling hoist He has 360-degree movement for the hoist within a 20-ft circle
Once a load of 8-ft pulp logs is delivered Struble uses a tractor loader to position them near his boiler He then cuts them in two and drills a 4-in deep 1-in dia hole in one end of each log
I use an Irwin three-point cutting bit and a low speed high torque drill says Struble
Using a hand-held remote control on a cable he activates the hoist to drop the log handle to the log
The handle is a 10-ft length of 1 1/2-in square tubing attached to the hoist cable in such a way that 10 in extends past the mount A piece of 1-in round steel rod extends out of the end of the tube
I ground down the top of the rod so it s rounded off Behind the rounded-off tip I ground down the shaft so it s about 1/4 in smaller in diameter than the rest of the rod says Struble When I slide the rod into the hole in the log and lift the hoist cable it picks the log up by the one end The knob left on the end of the rod catches and holds the log
Pushing on the long end of the handler Struble can guide the log pivoting the boom on the mast and sliding the hoist down the length of the boom until he reaches the door of the furnace
The hoist hangs from a trolley that tracks on a 10-ft long 4-in I-beam boom The boom rests on and is bolted to a steel stub welded to the mast A chain runs from the end of the boom to a chain tightener that is anchored to the top of the mast This allows Struble to adjust the tension on the chain always maintaining the boom without load slightly above a horizontal position
When the boom carries a heavy piece of wood it levels out explains Struble If it isn t horizontal the trolley will settle at the lowest end of the boom
The mast is a length of 3-in dia irrigation pipe mounted between two wheel hubs that act as pivot points To create the pivot points Struble cut the differential out of a car axle stripping away all but the hubs with their bolts and the remaining axle stubs
To anchor the mast I buried a 3-ft pipe vertically in the ground says Struble Pieces of angle iron are welded to the pipe to keep it anchored in the soil An 8-in dia plate is welded to it at soil level
I welded the bolts from one of the hubs to the plate and slipped the 3-in pipe over the axle stub he says With the tapered roller bearings in the hub it rotates freely even under heavy load
Struble then slipped the second axle stub into the top of the pipe with the hub and bolts pointing upwards Two 2 1/2-in pipes that connect the mast to a nearby wall attach to the hub
The pipes from the wall form a triangle of support to the top of the mast explains Struble The pipes have 1 by 2-in rectangular steel tubing welded in their ends
At the hub end the rectangular pieces each are clamped between two bolts on the hub At the other end they are pinned in a U-shaped bracket attached to the wall
The chain tightener attaches to a stub welded to the top of the pipe The setup makes it easy for Struble to disassemble the mast and boom if necessary or to adjust it to keep it vertical
To strengthen the mast itself Struble reinforced it with rebar He used two lengths of 1/2-in rebar welded at the top of the pipe and to the end of a foot long length of 3-in C-channel that extends perpendicular from the pipe and opposite the boom The rebar continues to the bottom of the pipe where it s again welded in place Additional pieces of rebar create more triangulated supports for the long rebar pieces
Using the rebar on the pipe gives it the strength of a 24-in deep beam explains Struble Yet it s light enough that I can pick it up and set it in place or take it down
To protect the trolley and hoist from rain and snow he covered the top of the I-beam with two cedar boards They are raised on blocks so they don t interfere with trolley movement
The cable from the hoist loops through a pulley at the log handler and back to the hoist This effectively doubles capacity of the 650-lb hoist
I ve replaced the motor on the hoist twice in 8 years and replaced switches a few times says Struble Otherwise it has worked well I can stack a couple of weeks worth of wood in half a day and then it only takes 15 min a day to load the stove
Contact: FARM SHOW Followup James Struble 2363 S Hill Island Rd Cedarville Mich 49719 ph 906 484-2976; jim@dancingwatersbnb com; www dancingwatersbnb com
The problem with big outdoor boilers is that it s really hard to slide big chunks of wood in on top of each other says Struble With my log loader I can do it without even getting smoke in my face
At 63 Struble wanted a way to fire his furnace easily for years to come He and his wife run a bed and breakfast in their 2 000-sq ft northern Michigan home They heat it and a 4 500-sq ft addition with wood The boiler also provides hot water year round
I burn 20 to 25 pulp cords or more than 80 000 lbs of wood a year says Struble We couldn t afford to live here without wood
His tower style log loader consists of a pivoting center post or mast with a 10-ft boom and a travelling hoist He has 360-degree movement for the hoist within a 20-ft circle
Once a load of 8-ft pulp logs is delivered Struble uses a tractor loader to position them near his boiler He then cuts them in two and drills a 4-in deep 1-in dia hole in one end of each log
I use an Irwin three-point cutting bit and a low speed high torque drill says Struble
Using a hand-held remote control on a cable he activates the hoist to drop the log handle to the log
The handle is a 10-ft length of 1 1/2-in square tubing attached to the hoist cable in such a way that 10 in extends past the mount A piece of 1-in round steel rod extends out of the end of the tube
I ground down the top of the rod so it s rounded off Behind the rounded-off tip I ground down the shaft so it s about 1/4 in smaller in diameter than the rest of the rod says Struble When I slide the rod into the hole in the log and lift the hoist cable it picks the log up by the one end The knob left on the end of the rod catches and holds the log
Pushing on the long end of the handler Struble can guide the log pivoting the boom on the mast and sliding the hoist down the length of the boom until he reaches the door of the furnace
The hoist hangs from a trolley that tracks on a 10-ft long 4-in I-beam boom The boom rests on and is bolted to a steel stub welded to the mast A chain runs from the end of the boom to a chain tightener that is anchored to the top of the mast This allows Struble to adjust the tension on the chain always maintaining the boom without load slightly above a horizontal position
When the boom carries a heavy piece of wood it levels out explains Struble If it isn t horizontal the trolley will settle at the lowest end of the boom
The mast is a length of 3-in dia irrigation pipe mounted between two wheel hubs that act as pivot points To create the pivot points Struble cut the differential out of a car axle stripping away all but the hubs with their bolts and the remaining axle stubs
To anchor the mast I buried a 3-ft pipe vertically in the ground says Struble Pieces of angle iron are welded to the pipe to keep it anchored in the soil An 8-in dia plate is welded to it at soil level
I welded the bolts from one of the hubs to the plate and slipped the 3-in pipe over the axle stub he says With the tapered roller bearings in the hub it rotates freely even under heavy load
Struble then slipped the second axle stub into the top of the pipe with the hub and bolts pointing upwards Two 2 1/2-in pipes that connect the mast to a nearby wall attach to the hub
The pipes from the wall form a triangle of support to the top of the mast explains Struble The pipes have 1 by 2-in rectangular steel tubing welded in their ends
At the hub end the rectangular pieces each are clamped between two bolts on the hub At the other end they are pinned in a U-shaped bracket attached to the wall
The chain tightener attaches to a stub welded to the top of the pipe The setup makes it easy for Struble to disassemble the mast and boom if necessary or to adjust it to keep it vertical
To strengthen the mast itself Struble reinforced it with rebar He used two lengths of 1/2-in rebar welded at the top of the pipe and to the end of a foot long length of 3-in C-channel that extends perpendicular from the pipe and opposite the boom The rebar continues to the bottom of the pipe where it s again welded in place Additional pieces of rebar create more triangulated supports for the long rebar pieces
Using the rebar on the pipe gives it the strength of a 24-in deep beam explains Struble Yet it s light enough that I can pick it up and set it in place or take it down
To protect the trolley and hoist from rain and snow he covered the top of the I-beam with two cedar boards They are raised on blocks so they don t interfere with trolley movement
The cable from the hoist loops through a pulley at the log handler and back to the hoist This effectively doubles capacity of the 650-lb hoist
I ve replaced the motor on the hoist twice in 8 years and replaced switches a few times says Struble Otherwise it has worked well I can stack a couple of weeks worth of wood in half a day and then it only takes 15 min a day to load the stove
Contact: FARM SHOW Followup James Struble 2363 S Hill Island Rd Cedarville Mich 49719 ph 906 484-2976; jim@dancingwatersbnb com; www dancingwatersbnb com
To read the rest of this story, download this issue below or click here to register with your account number.