You have reached your limit of 3 free stories. A story preview is shown instead.
To view more stories
(If your subscription is current,
click here to Login or Register.)
20-Ton Press Built From Scrap Iron
Larry Genge, Glovertown, Newfoundland; ph 709 533-2798, l_dgenge @yahoo.ca: "I built this 20-ton press from scrap metal, using 10-in. channel iron for the side posts and 6-in. channel iron for the bed. I can use 3 different sizes of interchangeable dies with it, ranging from 3/4 to 1 1/2 in. The hood springs off an old
..........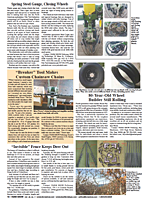
You must sign in, subscribe or renew to see the page.
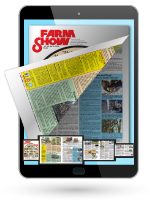
You must sign in, subscribe or renew to see the flip-book
20-Ton Press Built From Scrap Iron FARM SHOP Tools 34-4-37 Larry Genge, Glovertown, Newfoundland; ph 709 533-2798, l_dgenge @yahoo.ca: "I built this 20-ton press from scrap metal, using 10-in. channel iron for the side posts and 6-in. channel iron for the bed. I can use 3 different sizes of interchangeable dies with it, ranging from 3/4 to 1 1/2 in. The hood springs off an old car help raise the bed. My cost to build it was next to nothing - the biggest expense was $100 for the jack. I got the channel iron in return for repairing someone's road tractor, which was a day's work.
"I got tired of the flimsy handles coming unscrewed on my imported drill press. The press had three short, thin screw-in handles that stuck out at an angle and provided no leverage. The handles pulled hard, and I couldn't keep them tight because the threads often stripped where the handles were screwed on.
"To solve the problem I replaced the handles with a big 12-in. dia. wheel that came off a valve. The wheel has four l1 by 1/2-in. dia. metal handles welded on with knobs, scrounged from hydraulic control levers, friction-fitted to the ends. When using small bits with the drill press I just hold onto the wheel, but when using large bits I hold onto the handles to get more leverage. The improvement in the way my drill press handles now is beyond belief."
To read the rest of this story, download this issue below or click
here to register with your account number.