You have reached your limit of 3 free stories. A story preview is shown instead.
To view more stories
(If your subscription is current,
click here to Login or Register.)
Stubble Roller Saves Money On Tires, Fuel
Eliminate GMO hybrid damage to tires and other equipment with the Kitchel stalk roller. Unlike the various stalk choppers on combines and post harvest or bush hogging alternatives, Brandon Kitchel's solution reduces wear without adding significant fuel costs and time in the field.
"The stiff GMO stubble r
..........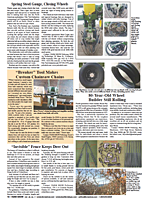
You must sign in, subscribe or renew to see the page.
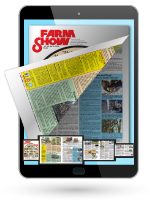
You must sign in, subscribe or renew to see the flip-book
Stubble Roller Saves Money On Tires Fuel COMBINES Accessories Eliminate GMO hybrid damage to tires and other equipment with the Kitchel stalk roller Unlike the various stalk choppers on combines and post harvest or bush hogging alternatives Brandon Kitchel s solution reduces wear without adding significant fuel costs and time in the field
The stiff GMO stubble rips up tires and speeds the wear on planter seed tubes wiring harness covers and hoses anything that s made of plastic says Kitchel Stalk choppers on combines are a drain on power and during or following harvest all choppers take added fuel Plus they often leave 4 in or more of the stiffest stubble in place
Kitchel s stalk roller has little impact on fuel use and doesn t require an added trip across the field The only power required is to pull the rollers across the field as the combine moves forward The 2-row rollers lower to the ground when the head lowers
I knew I needed more down pressure than just the rollers says Kitchel I ve seen rollers that push over the stalk and then the stalk stands up again as they go by
Spring tension added to the weight of the units presses the stalks down and crushes them at the crown Initially the springs added about 100 lbs of pressure to each roller Kitchel has since added another 50 lbs of pressure though that may be more than is needed
I knew we needed to damage the root ball where the resins and sugars all collect when the stalk dries down explains Kitchel Those sugars set up like a rock as they dry With the springs my rollers have enough down pressure to break the root ball off uproot it or shatter it into the ground
Kitchel s first design was a single ground-driven roller that ran the length of the corn head However it didn t allow for contours waterways and benches After rolling more than 2 000 acres for several years he worked with a local mechanical engineer to redesign it Now multiple 44-in long sections each crush two rows of stubble Kitchel notes that installation of the shorter sections is easier too
Rebar cleating that wraps around the steel rollers in a chevron pattern enhances the ground action of the roller Kitchel uses 5/8-in rebar welding it to the smooth steel rollers
The chevron pattern grabs the ground and walks over rocks better than the angle iron I first tried he says It also smoothes out the ride
Kitchel tried his new patent pending design out on a few acres last fall It worked well enough that he s now negotiating manufacturing rights with several companies It s unsure at this time what the price will be or when the rollers will be available
I am collecting emails and letters from people interested in buying rollers for their combines he says When the details are worked out I ll let people know
Contact: FARM SHOW Followup Kitchel Enterprises LLC 3426 Union Pike Richmond Ind 47374 cognity7@gmail com; www kitchelcornroller com
To read the rest of this story, download this issue below or click
here to register with your account number.