2011 - Volume #35, Issue #4, Page #19
[ Sample Stories From This Issue | List of All Stories In This Issue | Print this story
| Read this issue]
Double Hitch Rakes And Balers Make Hay Fast
![]() |
![]() |
![]() |
While mechanical drive transfers power to the second rake, the Hallets wanted to avoid that with the high power baler. They also wanted to avoid having to unhook the second unit for transport.
"There are a lot of double baler hitches around, but most are mechanical drive to the second baler with multiple gearboxes and shafts," says Dale. "Our front baler attaches to the tractor conventionally, while the second baler's pto drive is powered by a hydraulic motor. We bought our baling tractor with extra hydraulic capacity so it could handle the load."
Dale made the rake hitch about 8 years ago. It was a learning experience that later was applied to the baler hitch. While the first rake is hitched to the tractor, the second is pulled by a two-wheel cart at the end of a 20-ft., 6-in. by 6-in. square tubing that arches over the first rake. At either end of the arch, flat steel plate reinforces the connection with vertical posts.
At the tractor, the arch pivots on a vertical pipe mounted to the 3-pt. hitch. The base of the pipe contains a gearbox from a mixer mill with a straight-through drive for the front rake. The gearbox also has an output shaft that on the mixer mill had powered the mixing auger. This was directed through the pipe, a pivot connection and a second length of pipe to a second right angle gearbox centered on and below the arch. The shaft runs through several pillow block bearings and universal joints, as well as several hydraulic hoses as it follows the arch to the trailing cart and on to the rake. One hydraulic line runs to a one-way cylinder to raise and lower the rake.
At the cart, the wheels pivot, not the post. A hydraulic cylinder running from the axle to the tie rod assembly turns the wheels to send the rake left or right.
"I used a front axle from an old truck," says Dale. "The wheels had camber, which caused them to plow sod when turning. I had to adjust the wheel mounts so the wheels would tip in to overcome the camber."
After Richard, Dale's son, joined the farming operation, they decided to replicate the double rake hitch for the baler. The connecting arch for the second baler is also based at the tractor's 3-pt. hitch. However, it contains no gearboxes or drive shafts, only hydraulic hoses. It does have a ball hitch connection to the 3-pt. and a jack for easy disconnect.
"Originally we had a single 6-in. by 6-in. steel tube arch, but it had too much flex," says Dale. "We added a 2-in. steel tubing bridge tied to the arch with 4-in. wide pieces of 1/4-in. flat iron to make it rigid."
The arch attaches to the cart axle with an A-frame. The cartwheels pivot on kingpin assemblies. A hydraulic cylinder û attached to the cart and the tie rods û steers the wheels.
To run the baler, the Halletts used a 30 hp Orbit motor-driven flywheel. A check valve between the two sets of hydraulic lines supplying oil to the motor allows it to free wheel as needed.
"If you shut down the hydraulics and the flywheel was still turning, it would blow the motor apart," notes Dale.
The hydraulic oil all dumps back into the tractor's rear end. This avoids a separate oil cooling system for the cart motor.
A drive shaft connects the cart flywheel to the pto shaft on the trailing baler and its flywheel. The cart flywheel and shaft assembly, as well as the trailing baler hitch, all pivot as one inside the A-frame. The pivot is a 2 1/2-in. shaft inside a slightly larger tube. The assembly is also connected to the tie rod cylinder so it turns as the wheels turn.
"With the flywheel/shaft/hitch assembly pivoting together, the drive line and hitch are always in line," says Dale. "The operator can swing the trailing baler 15 ft. to the left or right. When transporting between fields, we just swing it into line."
He estimates the entire baler hitch cost around $1,000 out of pocket. "Richard did most of the design work and welding, based on my ideas," says Dale. "We used a flywheel from an old Massey Ferguson baler and a drive shaft from a feed mill. The wheels and axle were off an old Chevy truck rear end, and the rest was mostly scrap from the farm's bone yard."
Contact: FARM SHOW Followup, Hallett's Hay & Seed, RR 2, Carstairs, Alta., Canada T0M0N0 (ph 403 337-2469; ddhallett@xplornet.com).
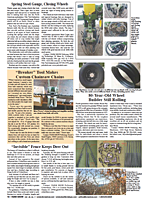
Click here to download page story appeared in.
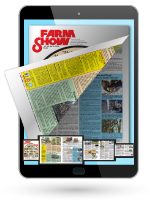
Click here to read entire issue
To read the rest of this story, download this issue below or click here to register with your account number.