You have reached your limit of 3 free stories. A story preview is shown instead.
To view more stories
(If your subscription is current,
click here to Login or Register.)
Forge Furnace Made From Beer Keg
Brian Johnson turns steel cable into Damascus steel bars, bending and forging as many as 56 layers for strength and appearance. The steel bars, or “billets”, are used for making knife blades. He has also made a steel vise, anvil and a multitude of other tools out of the metal. To reshape the hard steel, he uses heating
..........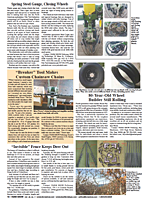
You must sign in, subscribe or renew to see the page.
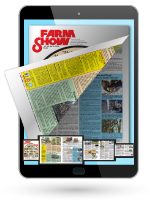
You must sign in, subscribe or renew to see the flip-book
Forge Furnace Made From Beer Keg FARM SHOP Miscellaneous Brian Johnson turns steel cable into Damascus steel bars bending and forging as many as 56 layers for strength and appearance The steel bars or “billets” are used for making knife blades He has also made a steel vise anvil and a multitude of other tools out of the metal To reshape the hard steel he uses heating and forging furnaces that he built himself using a beer keg and a propane tank
“My single burner forge furnace puts out more than 2 600°F says Johnson The body is a 16-gal stainless steel beer keg with castable refractory interior
Making the flux-proof forging furnace was a more complex job The easy part was cutting a hole for the fire chamber The refractory cement had to be poured all at once
I cut one end off the beer keg and centered a cylinder for the fire chamber inside the keg recalls Johnson Insulation anchors had to be welded inside the shell to anchor the refractory material should it crack I bought some anchors and made more placing them every 6 in on center They give the refractory mud something to hold to while it cures
Refractory material also had to be formed for the furnace mouth An earlier furnace had a steel mouth but it oxidized with heating and cooling With this furnace he made an outside form for the door and mouth with an inside square tube Once the refractory cement was poured and cured the form and the inside tube were cut away and Johnson had a furnace with no interior steel to oxidize
Johnson reattached the keg end first fabricating 1/2-in grooved rings in each edge Using 3/8-in thick 1-in bar stock he made a steel ring to fit inside the two grooves for a tongue and grooved effect
“I split the ring so it can expand and contract as the forge heats ” he says
The forge sits on a 10-ga steel cone with a shelf and door The cone serves as both a base and storage for fluxes and other materials Heavy-duty caster wheels provide mobility Each wheel is mounted on a steel tube within a tube for easy height leveling
He also fabricated a Venturi tube to feed the burner He describes the Venturi as a tube within a tube that he slides back and forth to achieve the right mix of oxygen and fuel to the burner Because he runs the propane at tank pressure the flow of fuel pulls the air into the burner
“I like a slightly fuel-rich flame ” he explains “If you have an oxygen-rich flame you have more problems with oxidation ”
Johnson mounted a small electric fan at the end of the mouth It blows a curtain of air across the handle of pieces being forged keeping them cooler and easier to work with It also disperses heat coming out of the forge making it more comfortable to work around
“The furnaces make it easy to work with metal which I enjoy ” says Johnson “I make tools and Damascus knife billets but not the knives I let others do that ”
Contact: FARM SHOW Followup Brian Johnson 16777 County Rd 751 N W Clearwater Minn 55320 ph 320 558-6898
To read the rest of this story, download this issue below or click
here to register with your account number.