You have reached your limit of 3 free stories. A story preview is shown instead.
To view more stories
(If your subscription is current,
click here to Login or Register.)
Urethane Foam: Latest New Insulator For Farm Buildings
"I wouldn't run a drying bin without it," notes Nolan Harms, Colfax, Ill., who 10 years ago insulated the bottom 4 to 5 ft. of his 7,000 bu. grain drying bin with spray-on urethane foam insulation.
Harms figures he cut his fuel costs 33%, saving over $1,000 each year. The 2-in. thick layer of insulation, with an
..........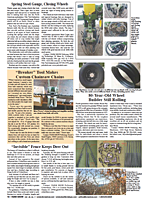
You must sign in, subscribe or renew to see the page.
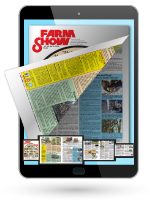
You must sign in, subscribe or renew to see the flip-book
Urethane Foam: Latest New Insulator for Farm Buildings BUILDINGS Miscellaneous I wouldn t run a drying bin without it notes Nolan Harms Colfax Ill who 10 years ago insulated the bottom 4 to 5 ft of his 7 000 bu grain drying bin with spray-on urethane foam insulation Harms figures he cut his fuel costs 33% saving over $1 000 each year The 2-in thick layer of insulation with an R-value of 14 3 cost $700 Meanwhile Ken Heberer and Tom Dutkanych Belleville Ill applied the same type of urethane foam insulation to the roof side and end walls of their rebuilt 56 x 128 ft modified open front hog building Urethane foam is an incredible insulator It resists external temperature variations and stabilizes the internal environment of the building says Heberer The above cases are just two examples of the versatility with which urethane foam can be used on farms say contractors who have applied the foam to industrial buildings for over 10 years Typically the contractors apply about 2 in of urethane foam which adheres as well to metal as to concrete On top of the urethane another coat of waterproof coating is applied to seal the foam and protect it from the sun s rays Once protected the urethane should last for the life of the bin or building say contractors For Harms there s no question about the payback Without keeping records we can tell we re drying grain 33% cheaper and faster The problem is that in a drying bin metal transfers heat very fast especially when the heat is under pressure A drying fan creates a tremendous amount of pressure so you lose a lot of heat in the bottom three or four feet of the bin The foam insulation saves the heat making the drying bin more efficient So far the foam has been maintenance free says Harms However moisture from the roof has been dripping on the coating wearing holes in it so that some foam is beginning to show through Where holes develop the foam will deteriorate within a year or two says Harms so we ll need to repaint the insulation Besides insulating the bottom of his drying bin Harms also foam insulated two bin roofs intending to reduce condensation However I m not sure it did any good he says He also applied urethane foam to the 3-ft high brick foundation of his house It worked In the winter it used to be so cold in the basement that even with the furnace going I almost needed a jacket Now I can take a shower downstairs no matter how cold it is outside Triple T Roofing Colfax Ill applied the foam insulation Our business has in-creased substantially over the last few years says Jerry Deavers area manager There are big energy savings at the point where the metal walls of the bin meet the concrete The tar commonly used to seal this seam dries and cracks every year letting a lot of heat escape Insulating the lower part of the outside walls which is in contact with heated air beneath the drying floor also provides great savings According to Deavers bin insulation costs about $3 per square foot or about $864 for a 30-ft dia bin Spraying over existing aluminum gave Heberer and Dutkanych a new roof and insulation with considerably less labor and cost than they d have experienced with replacement A protective coating covers and seals the foam to provide water and weatherproofing The building had been abandoned by the Heberer family several years ago and leased to another farmer When Heberer and Dutkanych took possession of it it was a mess The roof had some 6 ft holes and wouldn t hold weight The outside walls were covered with holes What little interior insulation was left was hanging from the ceiling The building was past the point of no return says Heberer It was demolish and start over or spray on foam When we considered the cost of labor plus the cost of reinsulation urethane foam came out the best Cost of the foam and a double layer of coating was $18 000 They gutted the building pouring new concrete walls for pen dividers replacing slats and inserting a 12 in baffled ridge vent the length of the building New curtains went in on both sid
To read the rest of this story, download this issue below or click
here to register with your account number.