2011 - Volume #35, Issue #6, Page #42
[ Sample Stories From This Issue | List of All Stories In This Issue | Print this story
| Read this issue]
Electric Drive Kit Boosts Planter Accuracy
![]() |
The kit contains a 4-row control board that mounts on the planter’s drawbar; a weatherproof harness using Deutsch connectors; and 4 electric motors. Each motor controls one row and replaces the chain and sprockets originally used to drive the seed plate. Each motor is controlled by a micro-processor-based drive system, which results in more precise seed placement, says Graham Equipment, Wray, Colo.
The system can be installed on both new and used planters of all brands, and interfaces with any of the major GPS guidance systems. It works with both single and twin-row planters.
“It replaces the need for both ground and hydraulic drive systems, and results in more planting accuracy and less maintenance, while also allowing for individual row shutoffs,” says inventor Toby Graham. “It’s much more accurate than ground and hydraulic drive systems. Our closed loop algorithm monitors the speed of each motor 1,000 times per second and adjusts accordingly. It allows our drives to be deadly accurate and respond to population rate changes at a blink of the eye.”
Less maintenance is another big advantage, says Graham, as the system completely eliminates the need for chains, sprockets and bearings. It also isn’t as cumbersome or maintenance intensive as hydraulic drive systems. The system also interfaces with individual row shutoffs on any GPS guidance system, “which makes it ideal for planting on odd-shaped fields and center pivot fields,” says Graham.
No-till farmers will like using a planter equipped with electric drive row units, says Graham. “Heavy trash can knock chains off their sprockets, but that isn’t a problem with electric drive.”
Graham says he came up with the idea because he wanted to use variable rate populations with his Monosem twin row planter. “I needed a way to change the timing between the paired rows in real time. Then I decided to expand the idea so it could be used with other planters. Last spring we installed electric drive kits on six different planters – five single row and one twin row – covering more than 5,000 acres. They worked great.”
An electric drive planter isn’t an entirely new idea, says Graham. “Back in the early 1970’s a major manufacturer came out with an electric motor drive system for its planters. However, they were way ahead of their time because back then the technology hadn’t been developed to accurately control electric motors.”
Graham plans to soon offer a cab-mounted touchscreen monitor for farmers who don’t have a GPS guidance system. “A monitor in the tractor will wirelessly communicate with the control board on the planter, eliminating the need for a wiring harness,” he says.
The motors are powered by the tractor’s battery. “Depending on the row count of your planter and your tractor’s alternator, you may need to add a hydraulically-driven alternator on the planter,” says Graham.
The electric planter drive kit sells for $949 per row plus S&H before Dec. 30, 2011; $999 per row plus S&H after Dec. 30. “That price may seem expensive, but it’s about $250 per row cheaper than installing a hydraulic drive system with row clutches and is a lot more accurate,” notes Graham.
Contact: FARM SHOW Followup, Toby Graham, 56251 Road QQ, Wray, Colo. 80758 (ph 970 520-7980 or 303 885-7428; toby@grahamelectricplanter.com; www.electricplanter.com).
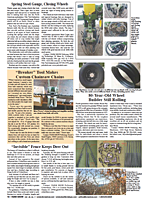
Click here to download page story appeared in.
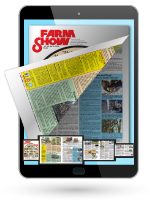
Click here to read entire issue
To read the rest of this story, download this issue below or click here to register with your account number.