2012 - Volume #36, Issue #1, Page #20
[ Sample Stories From This Issue | List of All Stories In This Issue | Print this story
| Read this issue]
Double Hitch Cuts Baling Time In Half
![]() |
![]() |
“I sell a lot of small bales of hay to the horse market,” explains Hanson. “I couldn’t go to a large baler, so operating two balers at once was the only way to get the job done faster. After using this setup, I would hate to go back to a single baler.”
Originally, Hanson envisioned using square tubing for the hitch’s main crossbeam. However, a 10-in. wide, 12-ft. long I-beam salvaged from an old creamery was the right length and height. The 12-ft. width provides ample room for the two in-line balers to track in parallel.
Hanson recognized that the hitch had to be sized to provide the right height for the baler hitches and pto connecting gearboxes. He chose to go with mechanical drives instead of hydraulic for cost and repairability.
“I looked at a commercial hitch, but it cost $14,000 and used hydraulic motors to power each baler,” says Hanson. “The gearboxes I used cost about $6,000 new, but if they break down I just replace a gear, bearing or possibly a shaft. When a hydraulic motor goes, it’s gone.”
Hanson welded a 12-ft. length of 12-in. wide channel iron over the top of the I-beam. It provided a mounting plate for bolting the gearboxes in place and also gave the beam more end-to-end strength.
“It ended up like a large T-beam with wheels mounted to spindles welded to either end,” says Hanson.
The tongue is a heavy wall length of 6-in. dia. steel pipe angle braced to the hitch crossbeam. Baler hitches are mounted on the backside of the beam at the height needed by the baler tongues. Hanson says he overbuilt the bale hitch projections and is glad he did.
“The baler tongues put a lot more weight on the hitch than I expected,” he says.
Hanson admits he also over-engineered the gearboxes. Though the balers require only 50 to 70 hp each, the gearboxes driving each is rated for 150 hp. The center gearbox that drives the outer boxes is rated at 250 hp. He used 1 1/2-in. shafts to connect the gearboxes. New U-joints added roughly $2,000 to the overall cost.
“I didn’t want the gearboxes to be the weak link,” explains Hanson. “I wanted to be sure I had plenty of capacity. “
Hanson says designing the gearbox set up was one of the more complex steps in building the hitch. “I sketched out where they would go, as I needed a three-shaft center one and two-shaft right and left drives to either side,” notes Hanson. “My supplier, Curtis Machine Company, was a big help.”
Going heavy-duty has paid off. Hanson notes that while the double baler hitch runs smoothly most of the time, occasionally a problem shows up that tests the hitch’s durability.
“Once in a great while, the balers get in sync with each other, and for a couple of minutes they really bang the tractor and the gearboxes,” says Hanson. “That’s when I’m glad the gearboxes are oversized.”
Contact: FARM SHOW Followup, Dane Hanson, 414 Spruce St., Jamestown, Kan. 66948 (ph 785 439-6518; dhanson73@gmail.com).
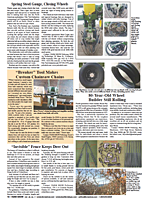
Click here to download page story appeared in.
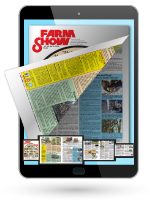
Click here to read entire issue
To read the rest of this story, download this issue below or click here to register with your account number.