2012 - Volume #36, Issue #3, Page #27
[ Sample Stories From This Issue | List of All Stories In This Issue | Print this story
| Read this issue]
King-Size Dually Took 2 Years To Build
![]() |
“When I started, all I had was an idea of what I wanted to build,” says Rothenbuhler. “To get parts that would fit was the biggest problem and took the most time. Pieces came from everywhere.”
The box and doors were from a Texas salvage yard and the four-door cab from a railroad company truck in Pennsylvania. The front hood came off a 1998 TopKick Chevy truck. The front end was taken from an over-the-road rig and the interior from a salvaged Suburban. The chassis is that of a 1998 2-ton Chevy used by a power company as a line truck.
Rothenbuhler started by stripping the chassis and chopping it back by about 9 ft. To get the height he wanted, he had a second frame made to match the first. Allfab, a supplier of boxes and other equipment to his trucking firm, did the fabrication out of new steel.
“We pulled the rear end up closer so the duals fit right in the fender wells,” says Rothenbuhler. “We had to change the interior of the cab quite a bit to make room for the engine.”
Rothenbuhler found a 3116 Caterpillar engine with an Allison automatic transmission. Its size required that firewalls in the cab be shifted. It also required cutting the rear driveshaft and cutting every crossmember in the chassis for it to fit.
“We had to lengthen the front driveshaft and add a drop box transfer case,” says Rothenbuhler. “It’s all air power to operate the front drive, no linkage. It makes it really smooth if we kick it into 4-WD as we’re going down the road.”
All used equipment was carefully overhauled with key components – such as U-joints on the front axle – rebuilt. All body parts were repainted. Some items were custom-designed, like the 10-ft. wide steps to match the 4-door cab at its new height. Rothenbuhler designed them to include storage spaces on the driver side and fuel tank and battery storage on the passenger side. He took his plans to Allfab.
“We tried out different ideas, such as gluing stuff together to see how it looked,” he recalls. “The storage side can hold folding chairs and stuff that’s nice to have at truck shows and such.”
As Rothenbuhler started assembling the various pieces, things didn’t always fit as intended. “We went through a lot of drill bits,” he says. “It took a lot of figuring to fit the cab on this frame.”
Other new components included a front bumper, which once it fit, was sent off to California along with the grill and other parts to be chromed. Rothenbuhler notes that the grill was plastic. The company made a metal form that fits on like a stencil. This was then chromed and attached to the grill.
He also added hood scoops, power windows, stainless steel mirrors and small chrome cubes for LED signals. LED’s were also installed in a chrome strip between the steps and the cab as well as in the box. Those, Rothenbuhler says, were the most difficult.
“We had to make them to fit where the regular lights had been,” he says.
Another customization was the 5-in. twin chrome stacks. They’re tied together by a Y pipe. Because the stacks come up beside the rear doors, Rothenbuhler had heat shields made for them as well as handles to grab as passengers climb into the cab.
The entire process took two years. Once complete, the big truck stands around 9 ft. tall and about 24 ft. long. It weighs in at 13,200 lbs. and gets more than its share of attention.
Contact: FARM SHOW Followup, Dean Rothenbuhler, P.O. Box 13, Cameron, Ohio 43914 (ph 740 458-1188).
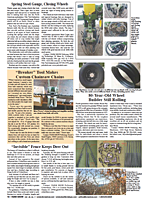
Click here to download page story appeared in.
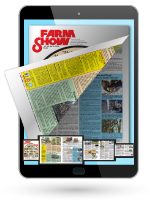
Click here to read entire issue
To read the rest of this story, download this issue below or click here to register with your account number.