2013 - Volume #BFS, Issue #13, Page #69
[ Sample Stories From This Issue | List of All Stories In This Issue | Print this story
]
Tractor Shed Built Out Of Tire “Bricks”
![]() |
“It’s not the fanciest shed in the world, but it’s built sturdy and keeps my tractors out of the weather. And, it only cost about $1,000.”
The one-of-a-kind building measures 20 ft. square and is open in front, with a gravel floor. The metal roof is supported by a steel frame and slopes from 15 ft. high in front to 10 ft. at the back. The walls are made from tires filled with crushed rock and measure 7 ft. high, with an opening between the walls and roof.
The car and truck tires overlap and interlock with the row below, just like bricks. The tires in the first 2 rows line up with each other, with the next 2 rows overlapping them.
The roof is supported by a series of steel trusses welded to 4 steel posts, one at each corner of the building. The roof is screwed onto 2 by 6 and 2 by 8 rafters on 16-in. centers.
To build the walls, Myrick first laid a row of tires on the ground. Then he used 4 short 1 by 4 sticks (old hardwood flooring) to prop each tire open, jamming the pieces between the tire beads to prop the sides of the tire open. That way, when crushed rock was dumped out of a loader bucket it wouldn’t flatten the tire out. Once the crushed rock was dumped, he removed the sticks and then used longer sticks to finish working crushed rock into the tires.
To contain crushed rock where the tires overlap, he cut circles out of tractor inner tubes and laid them in the bottom of each tire.
“Packing the tires was the most labor-intensive part of construction. It took at least 20 minutes to pack each tire. I never counted how many tires I used. It would probably be better to overlap each row of tires, but I didn’t have enough inner tubes,” he says.
He stood in a loader bucket and used a sledge hammer to drive the steel posts into the ground, without using any concrete as anchors. To help keep the roof from sagging, in some places he welded horizontal steel plates onto the posts. “The plates are wedged in between the tires so the posts won’t sink into the ground,” notes Myrick.
Contact: FARM SHOW Followup, Shane Myrick, 17758 Vail Rd., Pleasanton, Kan. 66075 (ph 913 757-3309).
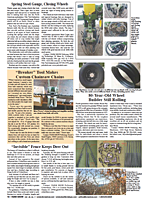
Click here to download page story appeared in.
To read the rest of this story, download this issue below or click here to register with your account number.