Custom Tools Re-Size Bolster And Kingpin Holes
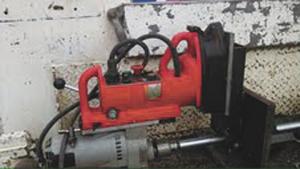 ✖  |
Wyoming machinist and mechanic Terry Peterson designed and built portable boring tools that he uses to re-size out-of-round holes on farm equipment. Peterson says he initially came up with the idea to repair the bolster on a Deere front end without removing it from the tractor. “I had to get the tractor fixed between Christmas and New Years so my customer could use it to move snow,” says Terry. “I looked into buying a commercial boring tool for the job, but that would’ve cost more than I could justify for my portable repair business.”
Peterson came up with his own method of repairing the bolster on the tractor. He can now use the device on Deere 10, 20, 30, 40, 50, 55 and 60 series tractors.
After he removes the damaged pin from the bolster, Peterson uses heavy-duty clamps to secure sealed bearing pillow blocks over the holes on both sides. Then he runs a solid piece of 1 1/4 -in. chrome steel through the pillow blocks to guide his boring bit. He adjusts the clamps to center the shaft in the holes, and then attaches the boring bit to the chuck on his Milwaukee magnetic drill. He uses a clamp set from a milling machine to attach the drill to the tractor, and then carefully bores the oval shape into a perfectly round and larger hole. Peterson says, “the key to getting a nice clean cut is to feed the bit at a slow and steady rate.”
Peterson has used his portable tool more than a dozen times for repairing bolsters on farm tractors and several more times for repairing oversized holes on backhoe buckets and articulating 4-WD tractor center pivots.
After a hole is bored to a larger and uniform size, Peterson installs a new bushing to hold the pin. “The bushing size I use depends on how much the owner let the old hole egg out,” Peterson says. “If the front was extremely worn and the back was okay, then I’ll center at 270 degrees of the old hole and bore it for a 1/8, a 1/4 or a 1/2- in. bushing.”
Peterson says equipment owners could avoid the problem of worn bolster holes and worn kingpin holes if they’d pay more attention to greasing. “Some people don’t grease at all, which is the worst, because metal on metal wears the pin and the bushings real fast. Others grease too much, and that’s almost as bad as not greasing, because the grease pressure dislocates seals in pivots.” Peterson says, “there’s so much hired help nowadays without a clue about when and how to grease equipment that I have plenty of work on projects like this.”
Another reason Peterson is seeing more problems is because many farmers in his area operate heavily ballasted tractors in 22-in. row crops. “Tractor front ends with wheels spaced 88 in. on center experience extreme stress in pivot areas because of the extra ballasting,” Terry says. He also says that farmers who use satellite-assisted steering on their tractors should remember to grease the front-end pivot points at least with every tank of fuel.
After his success with the bolster boring tool, Peterson made a different tool to repair the kingpin bearings on International Magnum tractors. To use that device he first welds a damaged hole undersized, and then machines it out to the size he needs to replace the bearing race. “This idea has been a work in progress,” Peterson says, “but repairing those kingpins is definitely less expensive than replacing them with a new or salvaged part.”
After more than 30 years as a Deere mechanic, Peterson now has a mobile service business that he operates from a 2002 Sterling service truck with a 16-ft. crane. His business takes him to farms, ranches and commercial outfits within a 100-mile radius of Powell, Wyo. “I’ve built up a relationship with a lot of customers over the years and I’m still working with them today,” says Peterson. “I also get calls from people who try repairing their own equipment and don’t realize simple things, like the fact that bushings are directional. If they’re put in the right way they’ll last 15 to 20 years, but if they’re put in backwards they might last a year at best. Peterson says people are also quick to use JB weld and Belzona metal, which is a fresh fit repair that doesn’t work on bushings because it’s not designed to repair a large hole. Peterson uses 4140 steel. After he re-sizes the hole, original equipment pins and bushings are used to complete the repair.
Contact: FARM SHOW Followup, Terry Peterson, 1967 Lane 9, Powell, Wyo. 82435 (ph 307 202-0700).
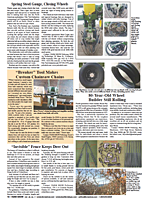
Click here to download page story appeared in.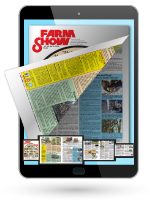
Click here to read entire issue
Custom Tools Re-Size Bolster And Kingpin Holes FARM SHOP Miscellaneous Wyoming machinist and mechanic Terry Peterson designed and built portable boring tools that he uses to re-size out-of-round holes on farm equipment Peterson says he initially came up with the idea to repair the bolster on a Deere front end without removing it from the tractor “I had to get the tractor fixed between Christmas and New Years so my customer could use it to move snow ” says Terry “I looked into buying a commercial boring tool for the job but that would’ve cost more than I could justify for my portable repair business ” Peterson came up with his own method of repairing the bolster on the tractor He can now use the device on Deere 10 20 30 40 50 55 and 60 series tractors After he removes the damaged pin from the bolster Peterson uses heavy-duty clamps to secure sealed bearing pillow blocks over the holes on both sides Then he runs a solid piece of 1 1/4 -in chrome steel through the pillow blocks to guide his boring bit He adjusts the clamps to center the shaft in the holes and then attaches the boring bit to the chuck on his Milwaukee magnetic drill He uses a clamp set from a milling machine to attach the drill to the tractor and then carefully bores the oval shape into a perfectly round and larger hole Peterson says “the key to getting a nice clean cut is to feed the bit at a slow and steady rate ” Peterson has used his portable tool more than a dozen times for repairing bolsters on farm tractors and several more times for repairing oversized holes on backhoe buckets and articulating 4-WD tractor center pivots After a hole is bored to a larger and uniform size Peterson installs a new bushing to hold the pin “The bushing size I use depends on how much the owner let the old hole egg out ” Peterson says “If the front was extremely worn and the back was okay then I’ll center at 270 degrees of the old hole and bore it for a 1/8 a 1/4 or a 1/2- in bushing ” Peterson says equipment owners could avoid the problem of worn bolster holes and worn kingpin holes if they’d pay more attention to greasing “Some people don’t grease at all which is the worst because metal on metal wears the pin and the bushings real fast Others grease too much and that’s almost as bad as not greasing because the grease pressure dislocates seals in pivots ” Peterson says “there’s so much hired help nowadays without a clue about when and how to grease equipment that I have plenty of work on projects like this ” Another reason Peterson is seeing more problems is because many farmers in his area operate heavily ballasted tractors in 22-in row crops “Tractor front ends with wheels spaced 88 in on center experience extreme stress in pivot areas because of the extra ballasting ” Terry says He also says that farmers who use satellite-assisted steering on their tractors should remember to grease the front-end pivot points at least with every tank of fuel After his success with the bolster boring tool Peterson made a different tool to repair the kingpin bearings on International Magnum tractors To use that device he first welds a damaged hole undersized and then machines it out to the size he needs to replace the bearing race “This idea has been a work in progress ” Peterson says “but repairing those kingpins is definitely less expensive than replacing them with a new or salvaged part ” After more than 30 years as a Deere mechanic Peterson now has a mobile service business that he operates from a 2002 Sterling service truck with a 16-ft crane His business takes him to farms ranches and commercial outfits within a 100-mile radius of Powell Wyo “I’ve built up a relationship with a lot of customers over the years and I’m still working with them today ” says Peterson “I also get calls from people who try repairing their own equipment and don’t realize simple things like the fact that bushings are directional If they’re put in the right way they’ll last 15 to 20 years but if they’re put in backwards they might last a year at best Peterson says people are also quick to use JB weld and Belzona metal which is a fresh fit repair that doesn’t work on bushings because it’s not designed to repair a large hole Peterson uses 4140 steel After he re-sizes the hole original equipment pins and bushings are used to complete the repair Contact: FARM SHOW Followup Terry Peterson 1967 Lane 9 Powell Wyo 82435 ph 307 202-0700
To read the rest of this story, download this issue below or click
here to register with your account number.