Chicken House Truss Bridge
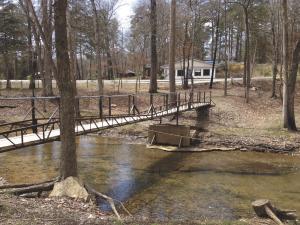 ✖  |
Ron Wrisinger needed a shortcut to his mailbox, so he built a walking bridge out of chicken house roof trusses. Combined with recycled fence, highline wire and other salvaged parts, he built an impressive bridge, as attractive as it is strong. About the only new parts were native oak used for the flooring.
“It took a lot of donated parts and help from neighbors to complete, but we got it done,” says Wrisinger. “Even with new lumber, I have only $250 in it. You could buy new trusses, and it would still be an inexpensive bridge.”
Knowing he wanted to build a bridge, a friend offered him 40-ft. trusses from a chicken barn he was tearing down. Wrisinger needed two pair to make the 80-ft. span. He also got the angle iron that had run from the foundation to support the trusses. These he cut up for uprights on the bridge and for crossbars.
Wrisinger butt-welded each pair of trusses and welded the uprights to them about every 6 1/2 ft. He welded 3-ft. lengths of angle iron between the bottoms of the trusses at 4-ft. intervals. Where the span pairs met, he added braces at an angle to the spans and the upright, reinforcing the connection.
Pipes from a friend’s recycled cyclone fence were welded to the bottom of the trusses and to the sides of the angle iron uprights to add more support. Longer lengths of pipe were screwed into standard fence connectors and welded to the uprights to form the handrail. To further reinforce the span, Wrisinger ran recycled highline cable through the uprights, end to end.
“I hooked the cable to the uprights at one end and put tensioners on the other end and tightened them up,” says Wrisinger. “A friend who is an architect advised me not to go more than 3 ft. wide based on the strength and length of the trusses. He said the narrow width would help avoid side sway.”
Wrisinger figured the narrow width would also keep ATV’s off the bridge. “Some people down here would drive their ATV’s on their mother’s grave,” he says.
Wrisinger bought native oak for the flooring and treated 2 by 4’s for supports underneath the flooring and over the metal crossbars. Even the flooring was a good deal.
“It was reject flooring returned to the local lumber mill and only cost me 10¢ a board foot,” he says. “I ran it through my planer to get it to size (1/2-in.). It wasn’t kiln dried, but I plan on using asphalt sealer on it with sand sprinkled in it for grip.”
“I did all the work in front of my shop and then with the help of a couple of friends, we moved it into place,” recalls Wrisinger. “We centered a camping trailer under it and pushed it down until the trailer was in the creek. Then one friend set his truck up on high ground across the creek and hooked on to the bridge with his winch to keep the end up off the bank. At the same time, my other friend pushed it across with his backhoe.”
One end of the bridge rests on a concrete stanchion that previously supported a car bridge. “I bolted it down to bedrock,” he says. “Neither it nor the bridge are going anywhere.”
Contact: FARM SHOW Followup, Ronald Wrisinger, HC 73 Box 23CC, Dogpatch, Ark. 72648 (ph 870 446-2781).
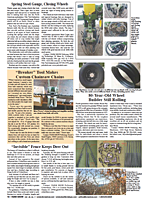
Click here to download page story appeared in.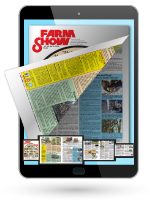
Click here to read entire issue
Chicken House Truss Bridge LIVESTOCK Poultry Ron Wrisinger needed a shortcut to his mailbox so he built a walking bridge out of chicken house roof trusses Combined with recycled fence highline wire and other salvaged parts he built an impressive bridge as attractive as it is strong About the only new parts were native oak used for the flooring “It took a lot of donated parts and help from neighbors to complete but we got it done ” says Wrisinger “Even with new lumber I have only $250 in it You could buy new trusses and it would still be an inexpensive bridge ” Knowing he wanted to build a bridge a friend offered him 40-ft trusses from a chicken barn he was tearing down Wrisinger needed two pair to make the 80-ft span He also got the angle iron that had run from the foundation to support the trusses These he cut up for uprights on the bridge and for crossbars Wrisinger butt-welded each pair of trusses and welded the uprights to them about every 6 1/2 ft He welded 3-ft lengths of angle iron between the bottoms of the trusses at 4-ft intervals Where the span pairs met he added braces at an angle to the spans and the upright reinforcing the connection Pipes from a friend’s recycled cyclone fence were welded to the bottom of the trusses and to the sides of the angle iron uprights to add more support Longer lengths of pipe were screwed into standard fence connectors and welded to the uprights to form the handrail To further reinforce the span Wrisinger ran recycled highline cable through the uprights end to end “I hooked the cable to the uprights at one end and put tensioners on the other end and tightened them up ” says Wrisinger “A friend who is an architect advised me not to go more than 3 ft wide based on the strength and length of the trusses He said the narrow width would help avoid side sway ” Wrisinger figured the narrow width would also keep ATV’s off the bridge “Some people down here would drive their ATV’s on their mother’s grave ” he says Wrisinger bought native oak for the flooring and treated 2 by 4’s for supports underneath the flooring and over the metal crossbars Even the flooring was a good deal “It was reject flooring returned to the local lumber mill and only cost me 10¢ a board foot ” he says “I ran it through my planer to get it to size 1/2-in It wasn’t kiln dried but I plan on using asphalt sealer on it with sand sprinkled in it for grip ” “I did all the work in front of my shop and then with the help of a couple of friends we moved it into place ” recalls Wrisinger “We centered a camping trailer under it and pushed it down until the trailer was in the creek Then one friend set his truck up on high ground across the creek and hooked on to the bridge with his winch to keep the end up off the bank At the same time my other friend pushed it across with his backhoe ” One end of the bridge rests on a concrete stanchion that previously supported a car bridge “I bolted it down to bedrock ” he says “Neither it nor the bridge are going anywhere ” Contact: FARM SHOW Followup Ronald Wrisinger HC 73 Box 23CC Dogpatch Ark 72648 ph 870 446-2781
To read the rest of this story, download this issue below or click
here to register with your account number.