2013 - Volume #37, Issue #4, Page #26
[ Sample Stories From This Issue | List of All Stories In This Issue | Print this story
| Read this issue]
Manure Spreader Retrofitted With Vertical Beaters
![]() |
![]() |
![]() |
“We had rented a vertical beater spreader, and it did a much better job than horizontal beaters do,” says Abram Bowman. “It chopped materials up fine and spread more evenly over a larger area. There are all kinds of options for new vertical spreaders, but they are expensive.”
Since the Bowmans have a custom manufacturing business on their farm, they decided to convert a horizontal beater spreader to vertical style. If it worked, they would have a better spreader and possibly an addition to their business.
They began by stripping off the old beater, trimming the sides to a 15° angle and reinforcing the spreader body to handle the strain. "We welded a heavy 4 by 4-in. steel beam (at the 15 degree angle) to each side," says Bowman. "We also added 6-in. wide steel side extensions to both sides to make the box more rigid, offer more load transfer across the box, and increase capacity."
The Bowmans jobbed out the construction of the beaters to an auger specialist. The flighting was made from 3/8-in. steel with each beater 36 in. in diameter.
"We mounted hammers at the edge of the flighting," says Bowman. "They are fixed, but will shear off if they hit something too hard. You can run it with one or two missing, but not more, as the beaters have to be carefully balanced end to end and side to side."
The beaters were mounted in a framework of 12-in. channel iron attached to the rear of the spreader. A gearbox mounted on the side drives a sprocket at the top. Heavy-duty, #80 roller chain drive powers the beaters. Drive sprockets and chain were boxed in with more channel iron.
"Because of the angle of the framework, we needed to put a double yoke on the beater driveshaft before it entered the gearbox," says Bowman. "We also added an override clutch to the beater shaft as the beaters continue to spin when you stop the pto. We added shear bolts as well for protection should we hit a rock or something."
Other changes to the spreader included converting the apron chain from pto drive to hydraulic. The hydraulic motor offers infinitely variable unloading speeds.
Bowman says they have had quite a bit of interest in their spreader, which is doing all they hoped it would as a manure handler. The key, he says, in deciding to do such a project is the condition of the existing spreader.
"You can spend $5,000 to $7,000 to convert one," he says. "If you’ve got a good spreader box and apron chain, you can avoid spending from $30,000 to $60,000 on a new vertical spreader."
Contact: FARM SHOW Followup, Lebanon Ag Service, 8450 Line 3, RR 3, Listowel, Ont., Canada N4W 3G8 (ph 519 291-6802).
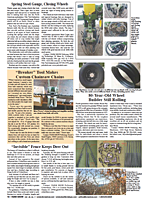
Click here to download page story appeared in.
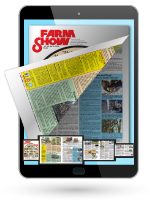
Click here to read entire issue