They Put Up 9,000 Bales A Day With 30-Bale Accumulator
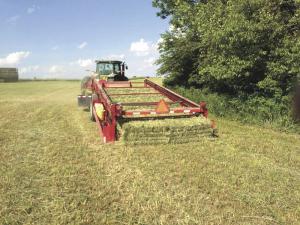 ✖  |
Ray Sponcil and his farm crew make 60,000 to 80,000 bales of wheat straw a year for sale to horse farms in Kentucky, plus several thousand bales of hay. They needed a faster way to handle them. Ray’s father, Ollie, solved the problem by building three 30-bale accumulators to fit their New Holland 5070 balers. Now they can bale, transport and store 9,000 bales a day.
“At one time, we had four 10-bale accumulators and handlers in the field,” recalls Sponcil. “I off-loaded the bales back at the barn with a 30-bale handler and had so much time between loads that I could have double-cropped soybeans while I waited.”
The 30-bale handler was built by Dave Steffen, Steffen Systems, Salem, Ore. “Dave was the only one who would build what we needed,” says Sponcil. “He put two 15-bale handlers together, and we built the brackets for our telehandler.”
After using the big handler to unload, Sponcil decided they needed bigger accumulators as well. He made a scale model for a 30-bale unit out of Erector set parts and then went full size. The accumulator worked even better than expected.
A paddle on the baler flips bales on a cut edge as they come off the baler. A grab chain channels them to the accumulator platform and between a press arm and a guide bar. As two bales move into place end to end, an electronic switch is triggered. The press arm pushes the pair and the guide bar back before resetting. As each set of bales is pushed back, the guide bar, which also is attached to 557 chain, moves to the rear. At the same time, a second bar called the unloading bar also mounted to the drive chain is moving forward above the bales.
When the platform is full, the guide bar has reached the rear of the platform, and the unloading bar has reached the front. This triggers hydraulic cylinders that tilt the platform so the rear edge touches the ground. Within seconds, a hydraulic motor on the chain drive kicks in, and the unloading bar pushes the load of bales off and onto the ground as the tractor and baler continue forward.
“Although we didn’t plan it, the first time we ran the accumulator, we realized the tilt cylinders require so much hydraulic fluid that there is a slight delay before the unloading bar starts pushing the bales off,” says Sponcil. “This helps keep the bales from dropping. They slide onto the ground in such a tight bundle that you can’t pull a bale out of the center.”
When his son started using the first accumulator, Sponcil was surprised to discover it packed 32 bales into the space of 30. Likewise the 30-bale handler picked up 32 bales, and they stayed compact and tight, fitting on a 30-bale per layer wagon. In fact, they are so tight that you can only pull bales loose at either end.
“We can load 160 bales (5 layers) on a wagon in less than 5 min. and pull two wagons to the barn at a time,” says Sponcil. “We had one guy tie down at the field, and another untie loads at the barn. Now we are going to 40-ft. semitrailers that hold 320 bales, with sides that eliminate the need for tie downs. They move the bales faster between field and barn.”
Sponcil built 4 of the big accumulators and sold one. He also had a second handler built for use in the field. It replaced the four 10-bale handlers used previously.
“The combination of accumulators, handlers and semi trailers lets us put up straw bales about five times as fast as before,” says Sponcil. “Now I have trouble keeping up with the balers.”
While each accumulator has been refined a bit, they all follow the same basic design. Sponcil says they have minimal interest in building accumulators for sale.
“If we did build to sell, we would be asking at least $40,000 for the accumulator due to all the hydraulics and electronics,” he says. “We would be more interested in selling the design to a manufacturer.”
Contact: FARM SHOW Followup, Ollie Sponcil, 11168 Bonner Rd., Greenfield, Ohio 45123 (ph 937 763-2392; osponcil@yahoo.com).
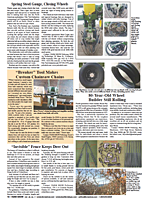
Click here to download page story appeared in.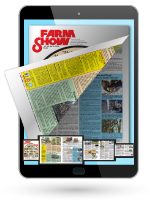
Click here to read entire issue
They Put Up 9 000 Bales A Day With 30-Bale Accumulator BALE HANDLING Ray Sponcil and his farm crew make 60 000 to 80 000 bales of wheat straw a year for sale to horse farms in Kentucky plus several thousand bales of hay They needed a faster way to handle them Ray’s father Ollie solved the problem by building three 30-bale accumulators to fit their New Holland 5070 balers Now they can bale transport and store 9 000 bales a day “At one time we had four 10-bale accumulators and handlers in the field ” recalls Sponcil “I off-loaded the bales back at the barn with a 30-bale handler and had so much time between loads that I could have double-cropped soybeans while I waited ” The 30-bale handler was built by Dave Steffen Steffen Systems Salem Ore “Dave was the only one who would build what we needed ” says Sponcil “He put two 15-bale handlers together and we built the brackets for our telehandler ” After using the big handler to unload Sponcil decided they needed bigger accumulators as well He made a scale model for a 30-bale unit out of Erector set parts and then went full size The accumulator worked even better than expected A paddle on the baler flips bales on a cut edge as they come off the baler A grab chain channels them to the accumulator platform and between a press arm and a guide bar As two bales move into place end to end an electronic switch is triggered The press arm pushes the pair and the guide bar back before resetting As each set of bales is pushed back the guide bar which also is attached to 557 chain moves to the rear At the same time a second bar called the unloading bar also mounted to the drive chain is moving forward above the bales When the platform is full the guide bar has reached the rear of the platform and the unloading bar has reached the front This triggers hydraulic cylinders that tilt the platform so the rear edge touches the ground Within seconds a hydraulic motor on the chain drive kicks in and the unloading bar pushes the load of bales off and onto the ground as the tractor and baler continue forward “Although we didn’t plan it the first time we ran the accumulator we realized the tilt cylinders require so much hydraulic fluid that there is a slight delay before the unloading bar starts pushing the bales off ” says Sponcil “This helps keep the bales from dropping They slide onto the ground in such a tight bundle that you can’t pull a bale out of the center ” When his son started using the first accumulator Sponcil was surprised to discover it packed 32 bales into the space of 30 Likewise the 30-bale handler picked up 32 bales and they stayed compact and tight fitting on a 30-bale per layer wagon In fact they are so tight that you can only pull bales loose at either end “We can load 160 bales 5 layers on a wagon in less than 5 min and pull two wagons to the barn at a time ” says Sponcil “We had one guy tie down at the field and another untie loads at the barn Now we are going to 40-ft semitrailers that hold 320 bales with sides that eliminate the need for tie downs They move the bales faster between field and barn ” Sponcil built 4 of the big accumulators and sold one He also had a second handler built for use in the field It replaced the four 10-bale handlers used previously “The combination of accumulators handlers and semi trailers lets us put up straw bales about five times as fast as before ” says Sponcil “Now I have trouble keeping up with the balers ” While each accumulator has been refined a bit they all follow the same basic design Sponcil says they have minimal interest in building accumulators for sale “If we did build to sell we would be asking at least $40 000 for the accumulator due to all the hydraulics and electronics ” he says “We would be more interested in selling the design to a manufacturer ” Contact: FARM SHOW Followup Ollie Sponcil 11168 Bonner Rd Greenfield Ohio 45123 ph 937 763-2392; osponcil@yahoo com
To read the rest of this story, download this issue below or click
here to register with your account number.