You have reached your limit of 3 free stories. A story preview is shown instead.
To view more stories
(If your subscription is current,
click here to Login or Register.)
"Made It Myself" Grain Handling System
Buying an efficient and high-speed on-farm grain handling system these days can easily run several hundred thousand dollars. “I really got a jolt when I heard those numbers,” says grain farmer Tim Kelly of Cokato, Minn. “That’s when my sons, Matthew and Shannon, and I started designing a system ourselves. We put it tog
..........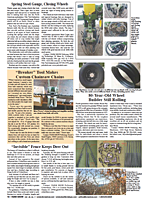
You must sign in, subscribe or renew to see the page.
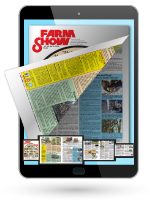
You must sign in, subscribe or renew to see the flip-book
Made It Myself Grain Handling System CROP STORAGE Grain Storage Buying an efficient and high-speed on-farm grain handling system these days can easily run several hundred thousand dollars “I really got a jolt when I heard those numbers ” says grain farmer Tim Kelly of Cokato Minn “That’s when my sons Matthew and Shannon and I started designing a system ourselves We put it together using new and used components and a lot of our own labor ” Kelly is an experienced do-it-yourselfer In recent years he’s built a high-capacity grain dryer augers for grain handling a lift mechanism for a 50-ft door on his machine shed a giant 60-ft field roller and a huge snow blade “Everything I’ve made I could’ve bought ” Tim says “but making things gives me a lot of satisfaction and saves money ” The showpiece of Kelly’s grain system is a 120-ft tall tower made of hot dipped galvanized steel It has a 127-ft belt and cup grain leg that discharges dry grain through 8-in spouts into 4 bins He plans to add a 70-ft leg that will send wet grain directly into his dryer A 7 000 bushel semi load-out bin stands on a 21-ft tall steel frame between his new 95 000 bu grain bin and the tower Kelly also built a grain pit and a high-capacity conveyor that will dump a semi in 6 to 7 min The electrical system controls and office are in a 12 by 26-ft building next to the tower with windows that overlook the pit and semi load-out “We thought a lot about how a system needs to work together before we started designing and building things ” says Kelly “It took almost a year for design and another year to get it manufactured and installed Making sure it functions properly is just as important as how much capacity it has ” Kelly is quick to point out that everything he makes is built to last He engineered the tower to have 1/2-in deflection at 120 ft and be able to withstand tornado-velocity winds The tower has four 6 by 6-in legs of 3/8-in steel up to 60 ft and the top 60 ft has 5 1/2 by 5 1/2-in legs Diagonal braces on each 10-ft section provide lateral support A floor at the top of the tower is 2 ft wider than the overall structure All of the steel is hot dipped galvanized The tower is supported by a concrete pad 10 ft square and 10 ft deep “This tower looks like big grain legs on many farms ” says Kelly “but it’s built stronger and it definitely has one unique feature that others don’t have ” That would be the 28-in square by 7-ft tall man lift The enclosed metal box rides inside 2 by 4-in rails up one side of the tower It raises and lowers as the operator manually pulls a continuous loop chain aided by a counterweight equal to the combined weight of the box and the person riding “We can get to the top of the tower in 15 seconds which sure beats the heck out of walking up 120 steps ” says Tim Kelly had a local supplier build the tower and deliver it to his farm unassembled He priced out having it erected on site but that would’ve required extra man hours for assembling the lift A few phone calls later he located a 150-ton crane that could raise the completely assembled tower in place for several thousand dollars less “I’m always happy to replace writing a check with labor ” says Tim “so the boys and I assembled the tower in the machine shed ” In the summer of 2012 the huge crane arrived and lifted the 27 000-lb tower onto the pad in less than a day They also used the crane to lift the frame and bin for the 7 000 bu load-out On that structure Kelly made the legs from steel tubes he bought from a salvage yard The 10-in diameter steel legs with 3/8-in sidewalls are filled with concrete and re-bar “A structural engineer told me that setup is stronger than I-beams and more resistant to weather and rust ” says Tim Part of this project also involved increasing the capacity of his home-built dryer by adding a third chamber on top of the two existing ones He can expand the dryer by another chamber and also has room to build additional bins that can be served by the 120-ft tower Contact: FARM SHOW Followup Tim Kelly 74861 262nd St Dassel Minn 55325 ph 320 286-2371
To read the rest of this story, download this issue below or click
here to register with your account number.