You have reached your limit of 3 free stories. A story preview is shown instead.
To view more stories
(If your subscription is current,
click here to Login or Register.)
Home-Built Tower Provides Great View
“Everyone who sees it wants to climb up for the view,” says Errol Borsky, Kamloops, B.C., about the 45-ft. tall concrete tower that he constructed “for fun” on his property.
The tower stands alongside a gravel road about 1/4 mile from his house and has a cage at the top with enough room to fit 2 people comfort
..........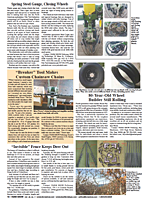
You must sign in, subscribe or renew to see the page.
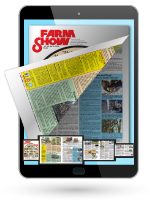
You must sign in, subscribe or renew to see the flip-book
Home-Built Tower Provides Great View FARM HOME Miscellaneous “Everyone who sees it wants to climb up for the view ” says Errol Borsky Kamloops B C about the 45-ft tall concrete tower that he constructed “for fun” on his property The tower stands alongside a gravel road about 1/4 mile from his house and has a cage at the top with enough room to fit 2 people comfortably It measures 4 ft sq by 5 ft tall with a castellated top edge added “just for fun” A ladder built from 1-in sq tubing bolts to the top 24 ft of the tower “I originally built it because I wanted some kind of camera tower for security after vandals raided my property I had some rock sculptures built for me but they were smashed to the ground and when I built 2 more the same thing happened again I added the cage on top as an after thought I figured that with all the time it took to build I may as well put something up there to stand on ” says Borsky “It makes quite a conversation piece I left the bottom 14 ft bare for liability reasons so no one can climb to the top without me knowing about it When someone wants to climb it I place a small aluminum ladder against the pole “The project took a lot longer than I thought it would because no one I knew had ever put up a 3 000-lb concrete pole I worked on it on and off for about one month a lot of the time scratching my head on how to go about it A lot of people told me I must have hired someone to set it up and can’t believe that I did the work myself ” He started out by building the cage and ladder and then securing them to the pole He used 1-in sq tubing to frame up the sides of the cage and used plywood and old sheet metal roofing for the sides leaving a hole for the ladder He screwed the plywood to the tubing and then bolted on sheet metal around the walls Metal braces on the cage and ladder were welded to brackets that bolt onto the pole and metal braces extend from the cage to the pole and ladder “The ladder bolts onto the pole at 5 different places with 5/8-in dia redi rod bolts going all the way through pre-cast holes to the other side ” says Borsky “I built the cage and ladder so that I could unbolt them and drag the pole to the installation site If I had welded everything solid it would have been too unwieldy to drag across the ground Once I dragged the pole out to the work site I reassembled everything ” He says the trickiest part of the project was putting the pole up “I used my Cat 12 road grader as my pulling machine I welded a bracket on top of the ROPS on the grader and chained a 30-ft long wooden pole down across it I then had two 7/16-in dia 60-ft long choker cables made up by a logging supply company and attached both chokers to the ends of the wooden pole and also to the top end of the concrete pole I attached another choker line from the concrete pole to my dump truck as a safety measure so in case the pole over-centered it wouldn’t come down on top of me “I used my excavator to dig a 7-ft hole and a trench leading into it Then I used a tractor equipped with a grapple fork to lift the top end of the pole and move it sideways into the hole The pole went up as slick as a whistle I had my wife hold a nut on the end of some old baler twine for a plumb bob She gave me directions as I used the excavator to ‘plumb’ the pole vertical Once the pole was all the way up I used a front-end loader to backfill the hole “The toughest part for me was climbing to the top because I have a fear of heights It took me a long time to get up there that’s for sure You’d think a concrete pole would be solid but they move around quite a bit when you’re up there ” Contact: FARM SHOW Followup Errol Borsky 1005 Barnhartvale Rd Kamloops B C Canada V2C 6Y1 ph 250 573-2164; eborsky@gmail com
To read the rest of this story, download this issue below or click
here to register with your account number.