Cotton Picker Converted To Self-Propelled Corn Chopper
Jim Anderson converted a used cotton picker into a silage chopper with a box that dumps. The self-propelled 2-row chopper doesn’t knock down corn rows like his pull-type chopper did. It also didn’t cost him as much as a conventional chopper.
“Why pay $100,000 or more for a self-propelled corn chopper when I only harvest 40 acres of silage?” asks Anderson. “The cotton picker only cost me $3,500, and even with all the changes, total cost was under $15,000.”
Making the transformation took Anderson more than a year of his spare time. He began by stripping down the 9920 Deere cotton picker. To improve visibility, he lowered the cab about 6 in. The cotton basket was replaced by a side-dump box from a silage wagon.
“We had to add a hydraulic valve for a second cylinder to handle the increased weight of silage,” says Anderson. “We mounted that cylinder over the steering axle. It helps to hold the dump box firm so it doesn’t flip over when it’s raised up.”
The chopper head is a converted chopper unit from a 3970 Deere pull-type chopper. It required extensive rebuilding, as he had to move the blower from the left side to the right side. That meant reversing the right-to-left feeding system.
“I had to change the auger direction and shorten it,” says Anderson. “It took quite a bit of tooling. I also had to shorten the frame so it would fit between the two front (drive) wheels.”
Anderson fabricated a bracket out of 5 by 5-in. steel tubing to hang the chopper header onto the original cotton picker header mount. Using the original cotton picker header lift system, he can lower the bracket with the chopper header about 6 to 8 in. He can then lower the chopper heads even closer to the ground using the chopper header’s lift system.
“It gives me up to 12 in. ground clearance at the fully raised position,” he says. “That makes for better handling on rough ground and gives me the option of leaving more stalk on the ground.”
Initially the chopper ran off the same hydrostatic pump as the picker head. Anderson quickly found he needed to modify it due to the occasional need to lug down. He moved the hydrostatic pump to the right side of the engine and the pto drive to the left side, running both off a jackshaft. Step-down pulleys on the pto drive run the chopper at 1,000 rpm’s when the engine is running at 2,000 rpm’s. Anderson installed an electromagnetic clutch between the pto driveshaft and the chopper drive.
With the changes, he’s able to control engine speed, ground speed and pto speed separately. An auxiliary hydraulic pump on the engine powers the steering, lift cylinders and other hydraulic needs.
“It was a challenge, but enjoyable,” says Anderson. “It ended up costing more than I expected due to the need for the electro-magnetic clutch.”
Contact: FARM SHOW Followup, Jim Anderson, P.O. Box 307, Blandon, Miss. 39043 (ph 601 832-2225; jba825@gmail.com).
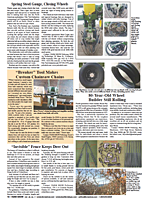
Click here to download page story appeared in.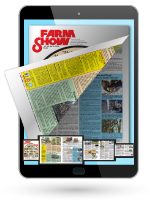
Click here to read entire issue
Cotton Picker Converted To Self-Propelled Corn Chopper FORAGE HARVESTERS Jim Anderson converted a used cotton picker into a silage chopper with a box that dumps The self-propelled 2-row chopper doesn’t knock down corn rows like his pull-type chopper did It also didn’t cost him as much as a conventional chopper “Why pay $100 000 or more for a self-propelled corn chopper when I only harvest 40 acres of silage?” asks Anderson “The cotton picker only cost me $3 500 and even with all the changes total cost was under $15 000 ” Making the transformation took Anderson more than a year of his spare time He began by stripping down the 9920 Deere cotton picker To improve visibility he lowered the cab about 6 in The cotton basket was replaced by a side-dump box from a silage wagon “We had to add a hydraulic valve for a second cylinder to handle the increased weight of silage ” says Anderson “We mounted that cylinder over the steering axle It helps to hold the dump box firm so it doesn’t flip over when it’s raised up ” The chopper head is a converted chopper unit from a 3970 Deere pull-type chopper It required extensive rebuilding as he had to move the blower from the left side to the right side That meant reversing the right-to-left feeding system “I had to change the auger direction and shorten it ” says Anderson “It took quite a bit of tooling I also had to shorten the frame so it would fit between the two front drive wheels ” Anderson fabricated a bracket out of 5 by 5-in steel tubing to hang the chopper header onto the original cotton picker header mount Using the original cotton picker header lift system he can lower the bracket with the chopper header about 6 to 8 in He can then lower the chopper heads even closer to the ground using the chopper header’s lift system “It gives me up to 12 in ground clearance at the fully raised position ” he says “That makes for better handling on rough ground and gives me the option of leaving more stalk on the ground ” Initially the chopper ran off the same hydrostatic pump as the picker head Anderson quickly found he needed to modify it due to the occasional need to lug down He moved the hydrostatic pump to the right side of the engine and the pto drive to the left side running both off a jackshaft Step-down pulleys on the pto drive run the chopper at 1 000 rpm’s when the engine is running at 2 000 rpm’s Anderson installed an electromagnetic clutch between the pto driveshaft and the chopper drive With the changes he’s able to control engine speed ground speed and pto speed separately An auxiliary hydraulic pump on the engine powers the steering lift cylinders and other hydraulic needs “It was a challenge but enjoyable ” says Anderson “It ended up costing more than I expected due to the need for the electro-magnetic clutch ” Contact: FARM SHOW Followup Jim Anderson P O Box 307 Blandon Miss 39043 ph 601 832-2225; jba825@gmail com